- お役立ち記事
- For managers of production technology departments in the plastic molding industry! In-mold labeling (IML) technology implementation example
For managers of production technology departments in the plastic molding industry! In-mold labeling (IML) technology implementation example
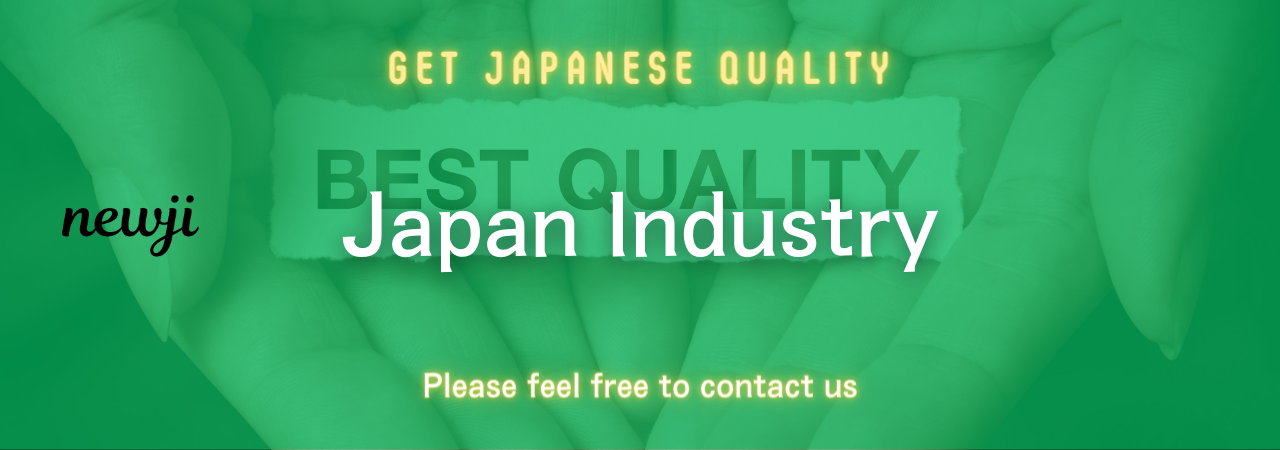
Implementing in-mold labeling (IML) technology in the plastic molding industry can offer significant advantages for production technology departments.
This method, which integrates labels with molded plastic products during manufacturing, enhances the durability and aesthetics of products, while streamlining the production process.
In this article, we’ll explore an implementation example to offer insights and strategies for managers who are considering adopting this innovative technology.
目次
Understanding In-Mold Labeling (IML) Technology
In-mold labeling is a process where pre-printed paper or plastic labels are placed in a mold before injecting polymer into the mold.
The label becomes an integral part of the final product, providing several benefits over traditional labeling methods.
IML enhances product aesthetics by offering high-quality and vibrant graphics.
Moreover, the technology enables the use of labels that resist moisture, chemicals, and abrasion, making the products suitable for various challenging environments.
Another significant advantage includes the opportunity for production efficiency.
By merging the labeling and molding processes, manufacturers can reduce production steps, shorten cycle times, and lower overall costs.
Implementation Example: A Case Study
Consider a mid-sized consumer products company specializing in household plastics.
The company’s management decided to implement IML to improve product appearance and streamline operations.
Step 1: Feasibility Study and Planning
The first phase of the implementation was a feasibility study.
The production technology manager gathered a cross-functional team, including representatives from research and development, production, and marketing.
The team evaluated the technical requirements of IML, such as the availability of machines capable of handling specific label types and thermoplastics.
Additionally, they considered the potential return on investment by analyzing current production costs and the anticipated savings from IML integration.
Their analysis revealed that adopting IML would allow for the elimination of a separate labeling stage, thereby reducing labor costs and materials.
With the positive results from this study, the company decided to proceed.
Step 2: Choosing the Right Equipment and Materials
The next step was selecting suitable machinery and materials to facilitate IML.
The company opted for robotic and automatic label feeding systems to ensure precision and efficiency.
Regarding materials, they selected labels and adhesives compatible with their plastic resins, ensuring strong adhesion and seamless integration.
By consulting with suppliers, they identified labels with optimized print quality and durability that would withstand the end-use conditions of their products.
Step 3: Staff Training and Process Optimization
Implementing new technology required thorough staff training.
Operational staff, including machine operators and maintenance technicians, were trained on the IML process, potential troubleshooting techniques, and quality control procedures.
The company also redesigned their production processes to accommodate IML.
By adjusting mold designs and cycle times, they maximized efficiency and quality.
Regular monitoring was conducted to ensure the process met the desired standards.
Challenges and Solutions
While implementing IML provides clear benefits, challenges can arise for managers in a production technology department.
Here are some common challenges and their solutions:
Label Placement and Quality Control
One challenge is achieving consistent and correct label placement in the mold.
To address this, the company used automated robotic arms for precise placement and integrated sensors for real-time monitoring.
Quality control was also improved by leveraging advanced inspection systems.
These systems detected misalignments or defects early, allowing for immediate corrective actions and minimizing waste.
Cost of Equipment and Materials
The initial cost of new machinery and materials required for IML can be substantial.
To mitigate costs, the company explored leasing options and negotiated payment terms with suppliers.
Furthermore, by conducting a thorough cost-benefit analysis, they demonstrated the long-term financial benefits to stakeholders, resulting in management buy-in and support.
Conclusion: Embracing In-Mold Labeling for Future Success
The successful implementation of in-mold labeling technology offers a valuable reference for managers in the plastic molding industry.
By understanding the process and potential challenges, companies can effectively integrate IML into their operations, unlocking benefits such as enhanced product quality, streamlined production, and reduced costs.
Adopting IML requires careful planning, investment in technology, and a commitment to staff training.
However, when executed well, it positions manufacturers to better meet customer demands and gain a competitive edge in the market.
For managers aiming to innovate and improve their production systems, in-mold labeling presents a transformative opportunity worth exploring.
資料ダウンロード
QCD調達購買管理クラウド「newji」は、調達購買部門で必要なQCD管理全てを備えた、現場特化型兼クラウド型の今世紀最高の購買管理システムとなります。
ユーザー登録
調達購買業務の効率化だけでなく、システムを導入することで、コスト削減や製品・資材のステータス可視化のほか、属人化していた購買情報の共有化による内部不正防止や統制にも役立ちます。
NEWJI DX
製造業に特化したデジタルトランスフォーメーション(DX)の実現を目指す請負開発型のコンサルティングサービスです。AI、iPaaS、および先端の技術を駆使して、製造プロセスの効率化、業務効率化、チームワーク強化、コスト削減、品質向上を実現します。このサービスは、製造業の課題を深く理解し、それに対する最適なデジタルソリューションを提供することで、企業が持続的な成長とイノベーションを達成できるようサポートします。
オンライン講座
製造業、主に購買・調達部門にお勤めの方々に向けた情報を配信しております。
新任の方やベテランの方、管理職を対象とした幅広いコンテンツをご用意しております。
お問い合わせ
コストダウンが利益に直結する術だと理解していても、なかなか前に進めることができない状況。そんな時は、newjiのコストダウン自動化機能で大きく利益貢献しよう!
(Β版非公開)