- お役立ち記事
- For new leaders in equipment maintenance departments in the steel industry! How to streamline pressure vessel inspection using ultrasonic flaw detection technology
For new leaders in equipment maintenance departments in the steel industry! How to streamline pressure vessel inspection using ultrasonic flaw detection technology
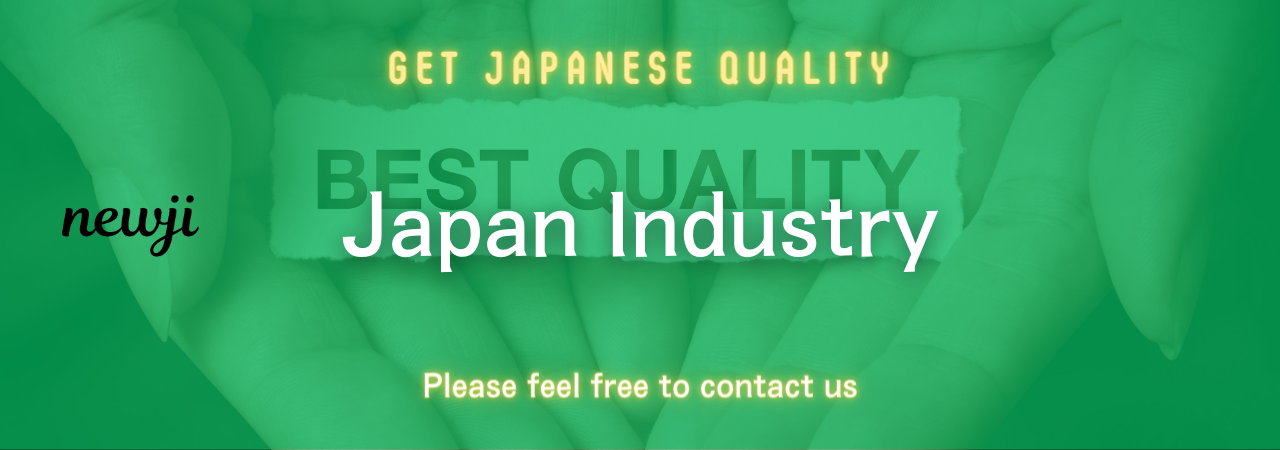
目次
Introduction to Pressure Vessel Inspection
Pressure vessels are critical components in the steel industry, often used to store and transport gases or liquids under high pressure.
The safety and integrity of these vessels are paramount, as failures can lead to catastrophic consequences, including accidents and costly downtime.
For new leaders in equipment maintenance departments, understanding how to effectively inspect these vessels is essential.
Ultrasonic flaw detection technology offers a powerful solution to streamline the inspection process, ensuring safety and efficiency.
What is Ultrasonic Flaw Detection?
Ultrasonic flaw detection is a non-destructive testing (NDT) method that uses high-frequency sound waves to detect imperfections, such as cracks or voids, within a material.
The technology sends ultrasonic pulses through the pressure vessel, and by analyzing the reflected waves, inspectors can identify flaws with remarkable precision.
The technique is particularly beneficial in assessing the integrity of pressure vessels without causing any damage or downtime.
The Benefits of Ultrasonic Testing
There are several reasons why ultrasonic flaw detection is favored in the steel industry:
1. **Accuracy**: The high-frequency sound waves used in ultrasonic testing offer unparalleled accuracy in detecting even the smallest of flaws.
2. **Safety**: As a non-destructive method, ultrasonic testing does not compromise the structural integrity of the vessel, ensuring continued safe operation.
3. **Efficiency**: Inspections can be performed quickly, without the need to disassemble or disturb the operation of the pressure vessel, minimizing downtime.
4. **Cost-effectiveness**: By preventing potential failures and reducing downtime, ultrasonic testing can lead to significant savings in maintenance costs.
Implementing Ultrasonic Flaw Detection
For new leaders in the field, implementing ultrasonic flaw detection requires understanding both the technology and the operational needs of your equipment maintenance department.
Training and Expertise
To maximize the benefits of ultrasonic testing, ensure that your team is adequately trained.
Ultrasonic testing requires a skilled operator to interpret data correctly, as misinterpretation can lead to inaccurate assessments.
1. **Certification Programs**: Enroll team members in NDT certification programs to ensure they are well-versed in the latest techniques and safety protocols.
2. **Continuous Learning**: Encourage ongoing education to keep up with technological advancements and improve inspection methodologies.
Integrating Technology
Integrating ultrasonic flaw detection technology into your inspection regimen involves a combination of appropriate equipment and systematic procedures.
1. **Selecting Equipment**: Choose reliable ultrasonic testing equipment that suits the specific requirements of your pressure vessel inspections.
2. **Developing Protocols**: Establish well-defined inspection protocols that outline how and when inspections should take place, ensuring consistency and reliability.
3. **Data Management**: Implement a robust data management system to track inspection results, identify trends, and plan maintenance schedules accordingly.
Challenges and Solutions
Despite its advantages, ultrasonic flaw detection can present certain challenges.
As a new leader, being prepared to address these issues will help ensure smooth operations.
Detecting Subtle Flaws
One of the primary challenges in ultrasonic testing is detecting extremely subtle flaws.
Advanced equipment and highly skilled operators are essential to effectively identify these imperfections.
Complex Geometries
Pressure vessels can have complex geometries that may complicate ultrasonic inspections.
Adapting inspection techniques and developing customized solutions are necessary to address these challenges.
Environmental Conditions
Environmental factors such as temperature and surface conditions can affect the accuracy of ultrasonic testing.
Implement strategies to mitigate these factors, like using specialized couplants or adjusting inspection parameters.
Conclusion
For new leaders in equipment maintenance departments in the steel industry, adopting and mastering ultrasonic flaw detection technology is crucial for ensuring the safety and efficiency of pressure vessel inspections.
By understanding the benefits of ultrasonic testing, investing in proper training, and preparing for potential challenges, leaders can streamline the inspection process and significantly enhance the reliability of these critical components.
資料ダウンロード
QCD調達購買管理クラウド「newji」は、調達購買部門で必要なQCD管理全てを備えた、現場特化型兼クラウド型の今世紀最高の購買管理システムとなります。
ユーザー登録
調達購買業務の効率化だけでなく、システムを導入することで、コスト削減や製品・資材のステータス可視化のほか、属人化していた購買情報の共有化による内部不正防止や統制にも役立ちます。
NEWJI DX
製造業に特化したデジタルトランスフォーメーション(DX)の実現を目指す請負開発型のコンサルティングサービスです。AI、iPaaS、および先端の技術を駆使して、製造プロセスの効率化、業務効率化、チームワーク強化、コスト削減、品質向上を実現します。このサービスは、製造業の課題を深く理解し、それに対する最適なデジタルソリューションを提供することで、企業が持続的な成長とイノベーションを達成できるようサポートします。
オンライン講座
製造業、主に購買・調達部門にお勤めの方々に向けた情報を配信しております。
新任の方やベテランの方、管理職を対象とした幅広いコンテンツをご用意しております。
お問い合わせ
コストダウンが利益に直結する術だと理解していても、なかなか前に進めることができない状況。そんな時は、newjiのコストダウン自動化機能で大きく利益貢献しよう!
(Β版非公開)