- お役立ち記事
- A must-see for processing engineers in the precision machinery industry! A practical guide to machining carbide materials and designing electrodes using EDM
A must-see for processing engineers in the precision machinery industry! A practical guide to machining carbide materials and designing electrodes using EDM
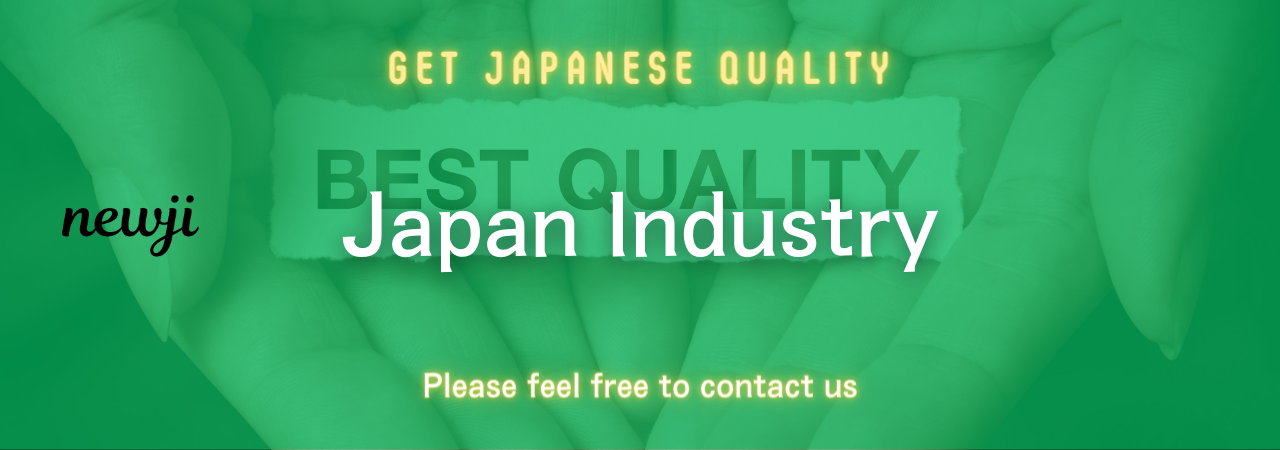
目次
Understanding Carbide Materials in Precision Machining
Carbide materials are a staple in the realm of precision machining, known for their hardness and resistance to high temperatures and wear.
These characteristics make them ideal for producing components that demand high precision and durability.
However, machining carbide materials is no easy feat.
It requires specialized techniques and tools to achieve desired results without damaging the material or compromising its properties.
Carbide is primarily composed of tungsten combined with a binder like cobalt.
This composition gives it its remarkable hardness.
However, this same hardness makes carbide challenging to machine using traditional methods.
Common Challenges in Machining Carbide
One of the key challenges in machining carbide materials is their brittleness.
Despite being hard, carbide is prone to chipping and cracking under improper machining conditions.
Additionally, carbide materials have a high thermal conductivity, which can lead to rapid tool wear due to excessive heat buildup.
Machining carbide also demands advanced cutting tools made from materials that can withstand the hardness without becoming dull quickly.
Diamond-tipped tools or other specialized inserts are usually recommended for these operations.
EDM: An Effective Technique for Machining Carbide
Electrical Discharge Machining (EDM) has emerged as a viable solution for machining carbide materials.
EDM uses electrical discharges or sparks to cut through materials, eliminating the direct contact between the tool and the workpiece.
This process is particularly advantageous for materials like carbide that are difficult to machine using conventional methods.
Benefits of EDM for Carbide Machining
1. **Precision**: EDM offers exceptional precision, capable of producing intricate details and complex shapes that are challenging to achieve through traditional machining techniques.
2. **Minimal Tool Wear**: Since there is no physical contact between the tool and the carbide workpiece, the tool wear is significantly reduced, prolonging the tool’s life.
3. **Surface Finish**: EDM produces a superior surface finish, reducing the need for additional finishing processes and minimizing defects on the carbide surface.
4. **Complex Shapes**: The ability to create complex shapes and fine details makes EDM a preferred choice for precision components in industries ranging from aerospace to electronics.
Designing Electrodes for EDM
Electrodes are crucial in the EDM process as they determine the shape and size of the machined cavity.
Designing effective electrodes is essential to maximizing the efficiency and precision of the EDM process.
Material Selection for Electrodes
When designing electrodes, choosing the right material is paramount.
Copper and graphite are commonly used due to their excellent electrical conductivity and capability to withstand the EDM process’s high-temperature conditions.
– **Copper Electrodes**: Known for their excellent conductivity and ability to produce fine finishes, copper electrodes are favored for applications requiring precision and detailed work.
– **Graphite Electrodes**: Graphite offers good electrical conductivity and is suitable for roughing operations where wear resistance is crucial.
Design Tips for Effective Electrodes
1. **Shape and Size**: The electrode’s shape and size directly influence the cavity’s accuracy and finish.
Ensure the electrode is designed to closely match the desired cavity geometry.
2. **Tolerances**: Consider tolerances carefully during the design phase, as precision is key to achieving the desired outcome.
3. **Sparkgap**: Account for the sparkgap in your design, which is the space between the electrode and the workpiece where the electrical discharge occurs.
The sparkgap can affect dimensions and surface finish.
4. **Thermal Considerations**: Account for thermal expansion in your electrode design, especially when working with materials that experience significant temperature changes during the EDM process.
Best Practices for Machining Carbide with EDM
Adopting best practices can further enhance the efficiency and outcomes of machining carbide materials using EDM.
Optimize Machining Parameters
– **Current and Voltage Settings**: Carefully set the current and voltage to optimize the balance between material removal rates and electrode wear.
– **Pulse Duration and Frequency**: Adjust pulse duration and frequency settings to control the material removal process, balancing speed and precision.
Maintain Proper Cooling
Ensuring proper cooling during the EDM process is crucial to prevent overheating and minimize thermal damage to both the carbide workpiece and the electrode.
Use appropriate dielectric fluids to aid in cooling and removing debris from the machining area.
Regular Equipment Maintenance
Regular maintenance of the EDM machine ensures optimal performance.
Inspect electrical connections, check for wear and tear on key components, and keep the machine clean to prevent disruptions.
By understanding the nature of carbide materials and utilizing techniques like EDM, engineers in the precision machinery industry can successfully machine carbide components effectively.
The combination of proper electrode design and best practices for EDM ensures high-quality, precision-machined parts that meet demanding industry standards.
資料ダウンロード
QCD調達購買管理クラウド「newji」は、調達購買部門で必要なQCD管理全てを備えた、現場特化型兼クラウド型の今世紀最高の購買管理システムとなります。
ユーザー登録
調達購買業務の効率化だけでなく、システムを導入することで、コスト削減や製品・資材のステータス可視化のほか、属人化していた購買情報の共有化による内部不正防止や統制にも役立ちます。
NEWJI DX
製造業に特化したデジタルトランスフォーメーション(DX)の実現を目指す請負開発型のコンサルティングサービスです。AI、iPaaS、および先端の技術を駆使して、製造プロセスの効率化、業務効率化、チームワーク強化、コスト削減、品質向上を実現します。このサービスは、製造業の課題を深く理解し、それに対する最適なデジタルソリューションを提供することで、企業が持続的な成長とイノベーションを達成できるようサポートします。
オンライン講座
製造業、主に購買・調達部門にお勤めの方々に向けた情報を配信しております。
新任の方やベテランの方、管理職を対象とした幅広いコンテンツをご用意しております。
お問い合わせ
コストダウンが利益に直結する術だと理解していても、なかなか前に進めることができない状況。そんな時は、newjiのコストダウン自動化機能で大きく利益貢献しよう!
(Β版非公開)