- お役立ち記事
- For new employees in the production technology department of the electrical equipment manufacturing industry! How to maximize productivity by implementing LEAN production methods
For new employees in the production technology department of the electrical equipment manufacturing industry! How to maximize productivity by implementing LEAN production methods
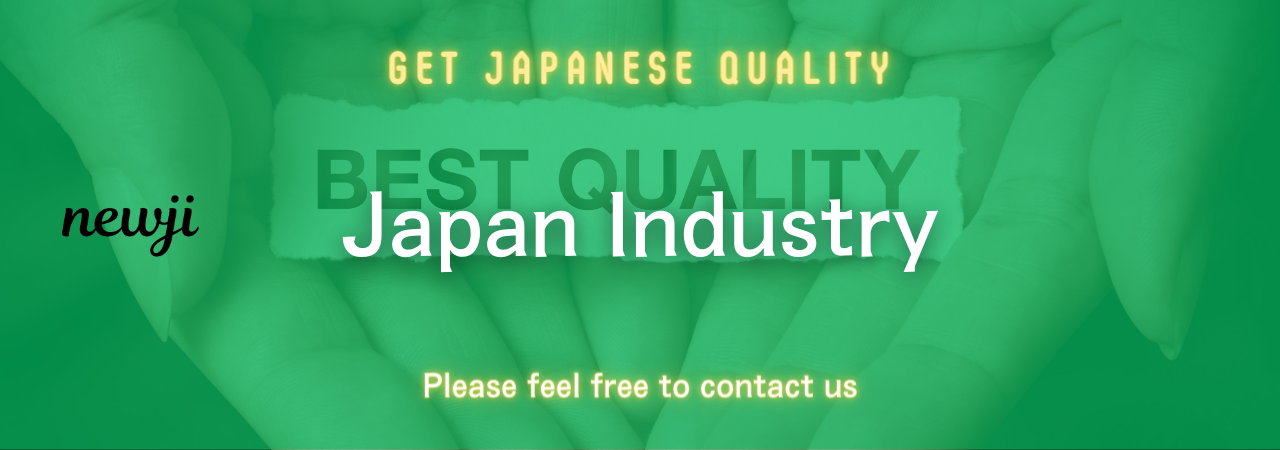
目次
Understanding LEAN Production
New employees entering the production technology department in the electrical equipment manufacturing industry often seek ways to enhance productivity effectively.
One of the most successful strategies to achieve this goal is by implementing LEAN production methods.
LEAN production, a concept developed primarily from the Japanese manufacturing industry, particularly Toyota, focuses on minimizing waste and maximizing efficiency.
It emphasizes value creation for the customer while using fewer resources.
By understanding and applying LEAN principles, you can significantly boost productivity in your workplace.
Key Principles of LEAN Production
Before diving into the application of LEAN production methods, it’s essential to grasp its core principles.
There are five key principles that form the foundation of LEAN production:
1. **Value**: Identifying what the customer considers valuable is the first step.
This ensures that all efforts are focused on creating products that meet the customer’s needs and expectations.
2. **Value Stream**: Mapping the value stream helps visualize the process involved in producing a product from start to finish.
It involves identifying every step in the production process and eliminating unnecessary activities that do not add value.
3. **Flow**: Establishing a smooth flow ensures that the production process runs continuously without interruptions.
It involves optimizing the work processes and layout to reduce wait times and bottlenecks.
4. **Pull**: Implementing a pull system matches production more closely with customer demand.
This minimizes overproduction and keeps inventory levels low, thus reducing work-in-process and finished goods inventory.
5. **Perfection**: Continuous improvement, or Kaizen, is central to LEAN production.
By constantly seeking ways to improve, the process becomes more efficient and productive over time.
Implementing LEAN Production in the Electrical Equipment Manufacturing Industry
With an understanding of LEAN’s principles, the next step is to implement these methods practically within the production technology department.
Start by gathering your team and educating them about LEAN principles.
This ensures everyone understands the objectives and is committed to the transformation process.
1. Value Identification
In the electrical equipment manufacturing sector, value is often associated with the product’s quality, reliability, and technological innovation.
Understanding customer expectations and feedback can help define what adds value from their perspective.
Engage directly with customers or use market research data to identify these values accurately.
2. Value Stream Mapping
Create a detailed map of the current production process.
Document every step from raw material procurement to the delivery of the final product.
Organize workshops with cross-functional teams to map out and analyze every process.
Identify processes that use time and resources but do not add value and plan strategies for improvement or elimination.
3. Ensuring Smooth Flow
After mapping the value stream, focus on optimizing the production flow.
Organize the workspace layout to support a seamless production process.
Implement methods like 5S, a workplace organization system that stands for Sort, Set in order, Shine, Standardize, and Sustain.
This approach helps smoothen the workflow and maintain discipline within the workspace.
4. Establish a Pull System
Adopt a pull production system by producing items only as they are needed by customers.
This approach prevents unnecessary stockpiling and reduces waste.
Implement tools like Kanban, which are visual signals, to maintain production levels that match demand.
5. Commit to Continuous Improvement
Promote a culture of continuous improvement within the organization.
Encourage employees at all levels to provide suggestions for bettering processes and solving problems.
Regular training and open communication can foster an environment where innovation and tangible improvements happen frequently.
Benefits of LEAN Production
Implementing LEAN production methods in the production technology department offers several benefits:
– **Increased Efficiency**: By eliminating waste and optimizing processes, the production becomes more efficient.
– **Reduced Costs**: Efficient resource use leads to cost savings in material, labor, and overheads.
– **Improved Quality**: Focusing on value creation results in products that better meet customer expectations.
– **Employee Satisfaction and Engagement**: Involving employees in improvement efforts fosters a sense of ownership and satisfaction.
– **Better Customer Satisfaction**: By consistently delivering high-quality products on time, the company enhances its reputation and customer loyalty.
Challenges and Considerations
While the benefits of LEAN production are significant, there may be challenges during implementation:
– **Initial Resistance**: Change can be met with resistance.
Effective communication and emphasizing benefits aid in overcoming resistance.
– **Continuous Commitment**: LEAN requires ongoing commitment and adaptation.
Without sustained effort, implementation might not achieve desired results.
– **Training Needs**: Continuous training and skill enhancement are crucial for all personnel, ensuring everyone understands and applies LEAN principles effectively.
Conclusion
Adopting LEAN production methods in the electrical equipment manufacturing industry can dramatically improve productivity, quality, and customer satisfaction.
By following the core principles and successfully implementing these strategies, new employees in the production technology department can significantly contribute to the company’s success.
With time, experience, and commitment, LEAN production can transform not only the production processes but also the corporate culture toward a more efficient and innovative future.
資料ダウンロード
QCD調達購買管理クラウド「newji」は、調達購買部門で必要なQCD管理全てを備えた、現場特化型兼クラウド型の今世紀最高の購買管理システムとなります。
ユーザー登録
調達購買業務の効率化だけでなく、システムを導入することで、コスト削減や製品・資材のステータス可視化のほか、属人化していた購買情報の共有化による内部不正防止や統制にも役立ちます。
NEWJI DX
製造業に特化したデジタルトランスフォーメーション(DX)の実現を目指す請負開発型のコンサルティングサービスです。AI、iPaaS、および先端の技術を駆使して、製造プロセスの効率化、業務効率化、チームワーク強化、コスト削減、品質向上を実現します。このサービスは、製造業の課題を深く理解し、それに対する最適なデジタルソリューションを提供することで、企業が持続的な成長とイノベーションを達成できるようサポートします。
オンライン講座
製造業、主に購買・調達部門にお勤めの方々に向けた情報を配信しております。
新任の方やベテランの方、管理職を対象とした幅広いコンテンツをご用意しております。
お問い合わせ
コストダウンが利益に直結する術だと理解していても、なかなか前に進めることができない状況。そんな時は、newjiのコストダウン自動化機能で大きく利益貢献しよう!
(Β版非公開)