- お役立ち記事
- Techniques to improve heat resistance and combustion efficiency that new employees in the gas burner manufacturing industry for high-temperature gas heaters should know
Techniques to improve heat resistance and combustion efficiency that new employees in the gas burner manufacturing industry for high-temperature gas heaters should know
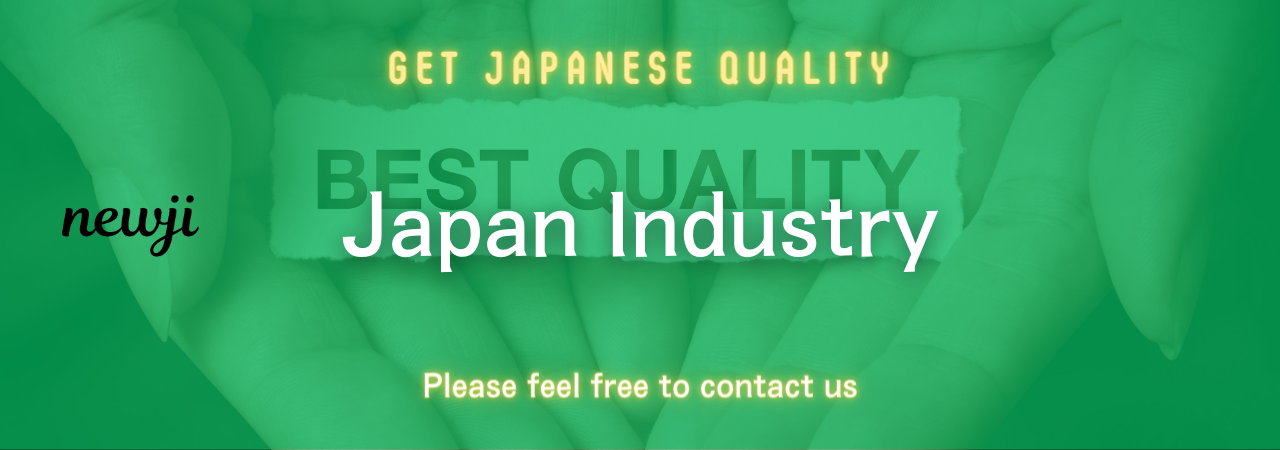
目次
Understanding Heat Resistance in Gas Burners
New employees in the gas burner manufacturing industry often find themselves dealing with the mechanics of high-temperature gas heaters.
A key aspect that needs your attention is improving heat resistance.
Heat resistance refers to the ability of materials used in burners to withstand extreme temperatures without degrading.
Selecting the right materials is crucial as it ensures longevity and safety.
The use of ceramics, special alloys, and composite materials can enhance heat resistance.
These materials are designed to remain stable under high temperatures, preventing any premature wear and tear.
For instance, stainless steel alloys are often preferred for their ability to maintain strength and integrity at elevated temperatures.
On the other hand, ceramics are chosen because of their low thermal conductivity and high temperature endurance.
Another technique to improve heat resistance involves surface treatment processes like coating and glazing.
Special coatings can be applied to surfaces that are exposed to intense heat, creating a barrier that minimizes thermal exposure to the core material.
With advancements in material science, coatings such as silicon carbide and aluminum oxide have been developed specifically to enhance resistance.
Enhancing Combustion Efficiency
Combustion efficiency is a measure of how well a gas burner converts fuel into energy or heat.
Improving this efficiency ensures that the burner operates economically and with minimal emissions, which is crucial in today’s environmentally conscious market.
One way to enhance combustion efficiency is through precise air-to-fuel ratio control.
When a burner operates at the correct air and fuel mixture, it burns fuel completely, reducing waste gases.
Sophisticated control systems and sensors can help achieve this optimal balance.
Tuning the burner’s design is another impactful method.
Ensuring the burner outlets and flame passages are engineered for ideal air circulation leads to more complete combustion.
Design improvements help reduce hotspots that cause uneven heating and unnecessary fuel consumption.
Additionally, regular maintenance and cleaning of burners are essential.
Burners clogged with soot or debris won’t burn fuel efficiently, leading to higher fuel consumption and reduced output.
Implementing a maintenance schedule can keep burners clean, ensuring they operate at peak efficiency.
Practical Tips for New Employees
For new employees stepping into the world of gas burner manufacturing, understanding these concepts is pivotal.
Begin by familiarizing yourself with the materials and their properties used in burner manufacturing.
Participate actively in training programs offered on material science applications in high-temperature environments.
Another tip is to study the combustion process and thermal dynamics.
Knowledge in this area will allow you to better understand how burner designs impact efficiency and resistance.
Engaging with experienced coworkers or mentors can provide insights that are not readily available in textbooks.
Keeping up-to-date with technological advancements in burner design and materials is also beneficial.
As technology evolves, new innovations emerge that enhance both heat resistance and efficiency.
Finally, consider environmental and safety regulations that apply to your industry.
Adhering to these guidelines not only ensures compliance but can also highlight areas where efficiency improvements are needed.
Future Directions in Gas Burner Technology
As industries push for greener solutions, gas burner technology must evolve.
Future trends indicate a move towards improved digital controls and smart sensors that automate adjustments for optimal performance.
These technologies help maintain efficiency and safety without constant manual intervention.
Additionally, research into nanomaterials and innovative alloys continues to provide new options in enhancing heat resistance.
These materials offer heightened durability and can withstand more extreme conditions than traditional options.
In the shift towards renewable energy sources, hybrid systems that integrate gas burners with solar or biomass energy are emerging.
Such systems aim to reduce dependency on fossil fuels while maintaining high output efficiency.
Integrating computational modeling in designing burners can also lead to greater advancements.
Modeling helps predict potential improvements and reduce trial-and-error designs, enhancing both efficiency and heat resistance.
By staying informed and adaptable, new employees in the gas burner manufacturing industry can contribute significantly to these developments and help create more sustainable and efficient high-temperature gas heater solutions.
資料ダウンロード
QCD調達購買管理クラウド「newji」は、調達購買部門で必要なQCD管理全てを備えた、現場特化型兼クラウド型の今世紀最高の購買管理システムとなります。
ユーザー登録
調達購買業務の効率化だけでなく、システムを導入することで、コスト削減や製品・資材のステータス可視化のほか、属人化していた購買情報の共有化による内部不正防止や統制にも役立ちます。
NEWJI DX
製造業に特化したデジタルトランスフォーメーション(DX)の実現を目指す請負開発型のコンサルティングサービスです。AI、iPaaS、および先端の技術を駆使して、製造プロセスの効率化、業務効率化、チームワーク強化、コスト削減、品質向上を実現します。このサービスは、製造業の課題を深く理解し、それに対する最適なデジタルソリューションを提供することで、企業が持続的な成長とイノベーションを達成できるようサポートします。
オンライン講座
製造業、主に購買・調達部門にお勤めの方々に向けた情報を配信しております。
新任の方やベテランの方、管理職を対象とした幅広いコンテンツをご用意しております。
お問い合わせ
コストダウンが利益に直結する術だと理解していても、なかなか前に進めることができない状況。そんな時は、newjiのコストダウン自動化機能で大きく利益貢献しよう!
(Β版非公開)