- お役立ち記事
- For project leaders in the plasma cutter nozzle manufacturing industry! Materials for increased precision and wear resistance
For project leaders in the plasma cutter nozzle manufacturing industry! Materials for increased precision and wear resistance
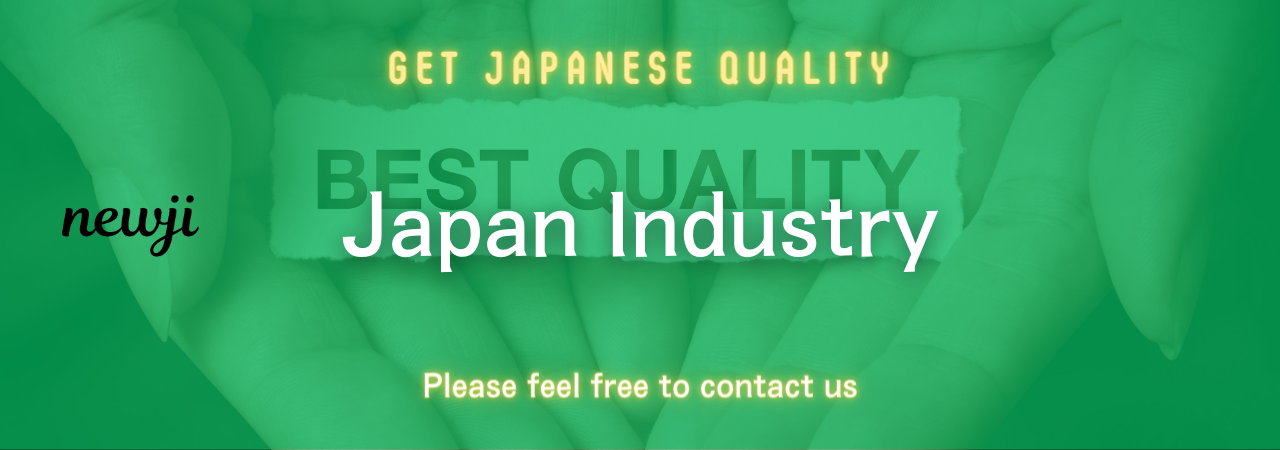
目次
Understanding the Importance of Precision and Wear Resistance
In the plasma cutter nozzle manufacturing industry, precision and wear resistance are crucial factors that can significantly affect the performance and longevity of the equipment.
The nozzle is a key component, responsible for directing the plasma arc and facilitating clean cuts.
Without a high degree of precision, the resulting cuts can be uneven, leading to material waste and additional expenses.
Wear resistance, on the other hand, ensures that nozzles maintain their shape and function even after prolonged usage, reducing the need for frequent replacements and maintenance.
The Role of Materials in Enhancing Performance
The choice of materials in manufacturing plasma cutter nozzles has a substantial impact on both precision and wear resistance.
Selecting the right material can enhance the nozzle’s durability, leading to improved cutting performance and operational efficiency.
Manufacturers are constantly seeking materials that offer optimal hardness, thermal conductivity, and resistance to high temperatures.
Materials for Increased Precision
Among the various materials available for manufacturing plasma cutter nozzles, a few stand out for their ability to provide high precision.
Copper and its alloys, particularly chromium copper and zirconium copper, are widely used due to their excellent thermal conductivity and machinability.
These materials allow the nozzle to maintain a stable temperature, reducing thermal deformation and ensuring consistent accuracy in cuts.
Tungsten is another material gaining popularity, known for its high melting point and superior wear resistance.
It offers the ability to create smaller orifices without losing precision, thanks to its rigidity.
Benefits of Using Copper Alloys
Copper alloys, especially those incorporating chromium or zirconium, offer several benefits for manufacturing plasma cutter nozzles.
They provide a good balance between conductivity and strength, which helps maintain the structural integrity of the nozzle during high-temperature operations.
Additionally, these alloys’ machinability makes it easier to achieve precision in the manufacturing process, resulting in better performance and reliability.
The balance of properties found in these materials makes them a versatile choice for many manufacturers.
Enhancing Wear Resistance with Advanced Materials
Wear resistance in plasma cutter nozzles is essential to ensure a long service life and maintain cutting performance over time.
Several advanced materials have been studied and developed to enhance this property, allowing nozzles to withstand the stresses of high-speed cutting.
One such material is ceramic, which is used in conjunction with metal alloys to improve durability without compromising on precision.
Ceramics’ natural heat resistance and hardness make them a suitable choice for applications requiring prolonged exposure to high temperatures and abrasive environments.
The Advantages of Using Tungsten
Tungsten, often used in combination with copper, provides excellent wear resistance due to its hardness and high melting point.
This makes it an ideal candidate for plasma cutter nozzles, particularly in industries where the equipment is subject to intense usage.
The durability offered by tungsten-alloyed nozzles translates to lower maintenance costs and fewer replacements, thereby delivering considerable long-term savings.
Its resistance to erosion from high-speed plasma flows makes tungsten a vital component in cutting-edge nozzle designs.
Innovations in Material Science
Innovation in material science continues to drive advancements in the plasma cutter nozzle industry.
With the development of new alloys and composites, manufacturers can now design nozzles with tailored properties that meet specific operational needs.
Emerging techniques such as additive manufacturing are also being explored, allowing for the creation of complex nozzle shapes that were previously difficult or impossible to achieve.
These techniques enable the optimization of material usage, potentially leading to lighter, more efficient nozzle designs that do not compromise on either precision or wear resistance.
Future Trends and Research
Looking forward, the plasma cutter nozzle manufacturing industry is likely to see further developments in the materials used.
Research into nanostructured alloys and coating technologies is expected to produce nozzles with enhanced surface properties, reducing wear and improving performance.
Another area of interest is the development of self-lubricating materials, which could minimize the friction between the nozzle and the plasma arc.
This innovation would not only increase wear resistance but also improve precision by reducing vibration and movement within the nozzle.
Conclusion: Choosing the Right Materials for Success
For project leaders in the plasma cutter nozzle manufacturing industry, selecting the right materials is crucial to achieving increased precision and wear resistance.
Understanding the properties and advantages of materials such as copper alloys, tungsten, and ceramics can guide better decision-making in production processes.
By investing in advanced materials and staying informed about the latest scientific developments, manufacturers can produce nozzles that offer superior performance, efficiency, and durability.
This strategic approach not only maximizes the effectiveness of plasma cutting but also provides a competitive edge in a rapidly evolving market.
資料ダウンロード
QCD調達購買管理クラウド「newji」は、調達購買部門で必要なQCD管理全てを備えた、現場特化型兼クラウド型の今世紀最高の購買管理システムとなります。
ユーザー登録
調達購買業務の効率化だけでなく、システムを導入することで、コスト削減や製品・資材のステータス可視化のほか、属人化していた購買情報の共有化による内部不正防止や統制にも役立ちます。
NEWJI DX
製造業に特化したデジタルトランスフォーメーション(DX)の実現を目指す請負開発型のコンサルティングサービスです。AI、iPaaS、および先端の技術を駆使して、製造プロセスの効率化、業務効率化、チームワーク強化、コスト削減、品質向上を実現します。このサービスは、製造業の課題を深く理解し、それに対する最適なデジタルソリューションを提供することで、企業が持続的な成長とイノベーションを達成できるようサポートします。
オンライン講座
製造業、主に購買・調達部門にお勤めの方々に向けた情報を配信しております。
新任の方やベテランの方、管理職を対象とした幅広いコンテンツをご用意しております。
お問い合わせ
コストダウンが利益に直結する術だと理解していても、なかなか前に進めることができない状況。そんな時は、newjiのコストダウン自動化機能で大きく利益貢献しよう!
(Β版非公開)