- お役立ち記事
- A must-see for new employees in the equipment management department! Fundamentals and effective practices of TPM (total production maintenance)
A must-see for new employees in the equipment management department! Fundamentals and effective practices of TPM (total production maintenance)
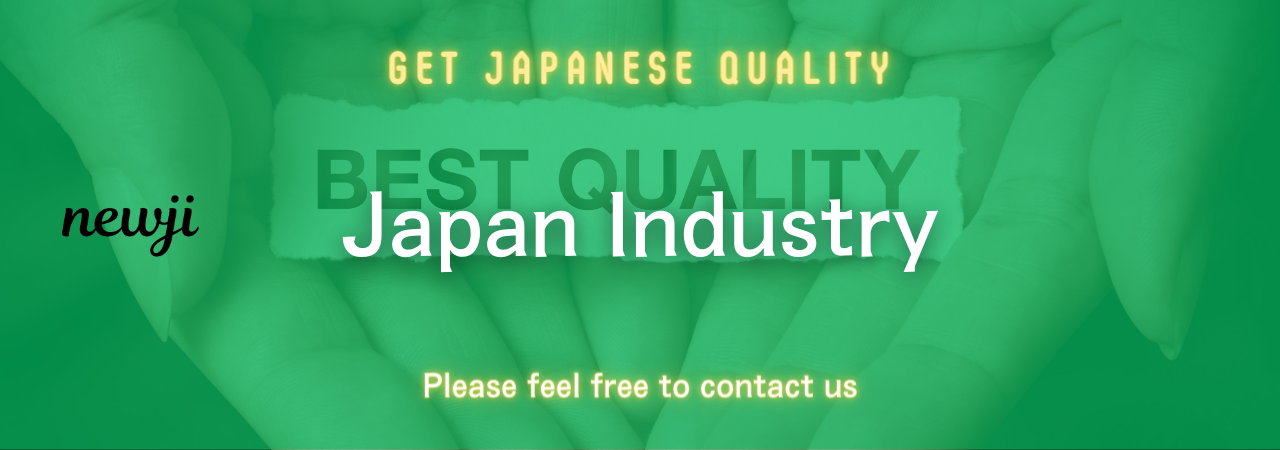
目次
Understanding TPM: The Basics
TPM, or Total Productive Maintenance, is a comprehensive approach designed to maximize the overall effectiveness of equipment within a manufacturing setting.
It is essential for new employees in equipment management to grasp the fundamentals of TPM, as these principles focus on maintaining and enhancing the productivity of machinery to reduce downtime and bolster efficiency.
TPM emerged in Japan in the 1970s, rooted in the concept of preventive maintenance, but it evolved to incorporate the involvement of all employees from top management to the plant floor.
The goal is to create a culture where maintenance, often considered a backend function, is integrated into the fabric of the production process itself.
There are seven key pillars of TPM, each addressing different aspects of equipment management.
These pillars include Autonomous Maintenance, Focused Improvement, Planned Maintenance, Quality Management, Early Equipment Management, Education and Training, and Safety, Health, and Environment.
Pillar 1: Autonomous Maintenance
Autonomous Maintenance empowers operators to take responsibility for the routine maintenance of their equipment.
This includes basic tasks such as cleaning, lubricating, and inspection.
The idea is that operators who work with the machinery daily have a unique understanding of its normal operations.
Training in this area is crucial so operators can quickly identify abnormalities before they develop into major issues.
This proactive approach reduces the risk of unexpected breakdowns and extends the lifespan of the equipment.
Pillar 2: Focused Improvement
Focused Improvement is about constantly seeking ways to enhance the overall efficiency and effectiveness of the production process.
This requires a team effort to identify areas for improvement, often using small group activities.
By encouraging teams to collaborate on solutions, the organization fosters a culture of continuous improvement.
This pillar encourages setting specific, measurable targets, and developing action plans to achieve them.
Pillar 3: Planned Maintenance
Planned Maintenance involves scheduling maintenance activities based on historical data and predicted needs, rather than reacting to equipment failure.
This planned approach minimizes downtime by ensuring that all equipment is maintained before it reaches a critical point of failure.
It also involves the use of predictive maintenance techniques, such as analyzing vibration, acoustics, or thermal data, to anticipate problems.
Pillar 4: Quality Management
TPM also emphasizes Quality Management, ensuring that manufacturing processes are aligned to prevent defects and failures.
By embedding quality into maintenance activities, issues such as product defects, rework, and wastage are reduced.
Quality management within TPM relies on root cause analysis to eliminate recurring problems, ensuring machinery produces conforming products consistently.
Pillar 5: Early Equipment Management
Early Equipment Management involves the integration of equipment maintenance considerations during the design and acquisition phase.
The aim is to install new equipment with future maintenance needs in mind, reducing long-term costs and improving reliability.
Engaging operators and maintenance personnel early in the design or acquisition phases ensures the machinery is user-friendly and maintainable.
Pillar 6: Education and Training
Education and Training are critical components of TPM.
Employees at all levels must understand TPM principles, and possess the skills needed to execute their roles effectively.
By continuously developing skills through regular training sessions, the organization builds a knowledgeable workforce capable of meeting the demanding environment of modern manufacturing.
Pillar 7: Safety, Health, and Environment
Safety, Health, and Environment are essential pillars that ensure all maintenance and production activities are conducted safely without negative impact on the environment.
TPM incorporates rigorous safety standards and promotes a health-centric work culture.
By prioritizing safety and environmental considerations, TPM not only protects employees but also prevents costly compliance violations and environmental damage.
Effective Practices for Implementing TPM
For new employees in equipment management, understanding the effective practices for implementing TPM is vital.
Initially, management must demonstrate firm commitment and lead by example.
Without leadership support, efforts to implement TPM may struggle to gain traction.
Communication is another critical factor.
Ensuring that all employees understand the objectives of TPM and are informed about progress helps to cultivate a motivated team ready to embrace change.
Moreover, setting clear objectives for TPM initiatives helps align all efforts towards achieving measurable outcomes.
Regular performance metrics should be shared with teams to track progress and celebrate successes.
Employee involvement is also key.
Fostering a sense of ownership in the equipment encourages operators and maintenance staff to take initiative in caring for their machinery.
This can be achieved by establishing cross-functional teams tasked with applying TPM concepts and strategies.
Regular training sessions should be conducted to ensure everyone is up-to-date with the latest tools and techniques.
Investing in training enhances the skill set of the workforce, allowing them to perform their roles more effectively.
Finally, creating a feedback loop is essential.
Feedback provides valuable insights that can be used to refine existing TPM strategies and drive continuous improvement.
Conclusion
Understanding and implementing TPM can empower new employees in equipment management to significantly contribute to enhancing operational efficiency.
By internalizing the TPM pillars and adopting effective practices, organizations can navigate the complexities of today’s manufacturing environment with greater ease.
TPM is more than just a maintenance strategy; it is a holistic approach aimed at fostering a more productive, efficient, and sustainable manufacturing operation.
資料ダウンロード
QCD調達購買管理クラウド「newji」は、調達購買部門で必要なQCD管理全てを備えた、現場特化型兼クラウド型の今世紀最高の購買管理システムとなります。
ユーザー登録
調達購買業務の効率化だけでなく、システムを導入することで、コスト削減や製品・資材のステータス可視化のほか、属人化していた購買情報の共有化による内部不正防止や統制にも役立ちます。
NEWJI DX
製造業に特化したデジタルトランスフォーメーション(DX)の実現を目指す請負開発型のコンサルティングサービスです。AI、iPaaS、および先端の技術を駆使して、製造プロセスの効率化、業務効率化、チームワーク強化、コスト削減、品質向上を実現します。このサービスは、製造業の課題を深く理解し、それに対する最適なデジタルソリューションを提供することで、企業が持続的な成長とイノベーションを達成できるようサポートします。
オンライン講座
製造業、主に購買・調達部門にお勤めの方々に向けた情報を配信しております。
新任の方やベテランの方、管理職を対象とした幅広いコンテンツをご用意しております。
お問い合わせ
コストダウンが利益に直結する術だと理解していても、なかなか前に進めることができない状況。そんな時は、newjiのコストダウン自動化機能で大きく利益貢献しよう!
(Β版非公開)