- お役立ち記事
- High-precision drilling technology in milling that design department leaders in the precision machinery industry should know
High-precision drilling technology in milling that design department leaders in the precision machinery industry should know
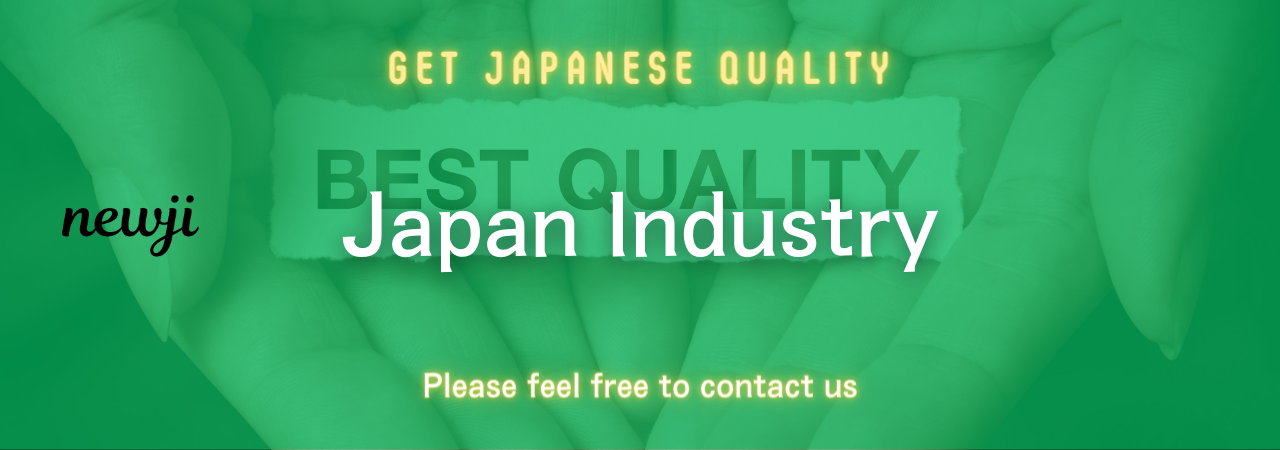
目次
Introduction to High-Precision Drilling Technology
High-precision drilling technology plays a pivotal role in the precision machinery industry, especially for design department leaders aiming to enhance their products’ accuracy and efficiency.
Modern milling processes have evolved significantly, thanks to advancements in technology and innovative engineering techniques.
This technological evolution allows for more precise drilling, enabling the creation of complex components used in various industries such as aerospace, automotive, and medical devices.
Design department leaders need to stay informed about these advancements to effectively integrate them into their projects.
This article explores high-precision drilling technology in milling and highlights essential knowledge that could be transformative for the precision machinery industry.
Understanding High-Precision Drilling
High-precision drilling involves the use of advanced equipment and methodologies to achieve exceptionally accurate and consistent results.
These processes require machines with superior specifications, like CNC (computer numerical control) mills, which are specifically designed to reduce tolerances and handle sophisticated drilling tasks.
Precision drilling is not solely about the machinery.
It involves a holistic approach that combines the right tools, techniques, and metrology equipment to ensure that every hole drilled meets the required specifications to the finest detail.
The integration of CAD/CAM software enhances the accuracy and efficiency of the milling process.
These software programs provide detailed blueprints and simulate drilling processes before actual machining takes place, identifying potential flaws and optimizing the workflow.
Key Technologies in Precision Milling
CNC Milling Machines
CNC milling machines are the backbone of high-precision drilling technology.
These machines offer unmatched precision levels, thanks to their ability to follow detailed programmed instructions and reduce human errors.
CNC technology allows for consistent quality and can replicate complex patterns with incredible accuracy, essential for industries relying on strict precision.
Advanced Tooling
High-precision drilling requires specialized tools capable of maintaining their edge and accuracy over prolonged use.
Carbide drills, coated with durable materials like titanium nitride, are commonly used due to their hardness and resistance to wear.
These advanced tools ensure precision by minimizing deflection and improving the reliability of the drilling process.
Micro Drilling
Micro drilling technologies are essential when dealing with extremely small components.
They require not only specialized drills but also unique techniques to prevent tool breakage and ensure that the tiny holes remain precise.
The advent of laser-assisted and ultrasonic micro-drilling has opened new avenues for drilling tiny, intricate holes in hard materials with high precision.
The Role of Metrology
Metrology, the science of measurement, is crucial in high-precision drilling.
To ensure each drilled component meets specific designs and tolerances, design department leaders must incorporate accurate metrology tools.
Coordinate Measuring Machines (CMM) and laser measurement technologies are frequently used to verify the precision of drilled holes.
These devices provide accurate data, allowing for timely adjustments and optimization of the milling process.
Benefits of High-Precision Drilling
The transition to high-precision drilling technologies provides numerous advantages.
These benefits include improved component quality, the capability to produce complex geometries, and enhanced product reliability.
Improved Quality
Precision drilling leads to finished products with better surface finishes and tighter tolerances, essential for high-performance applications.
The reduced variability in production enhances overall quality and consistency, leading to fewer defects and higher customer satisfaction.
Complex Geometries
Modern precision drilling technologies allow for the creation of complex geometries that were previously impossible with traditional drilling methods.
This capability opens new possibilities for product designs and applications across various industries.
Increased Efficiency
By reducing the need for manual intervention and enabling automation, precision drilling boosts production efficiency.
This increased efficiency translates into lower production costs and faster turnaround times, providing a competitive edge for manufacturers.
Challenges in Implementing Precision Drilling
Despite its advantages, high-precision drilling presents several challenges that design department leaders need to address.
Initial Setup Costs
Investing in advanced CNC machines, specialized tooling, and metrology equipment can be costly.
Companies must carefully evaluate the long-term benefits versus the initial expenses to ensure that upgrades align with their business goals.
Skilled Workforce
Operating and maintaining high-precision drilling equipment require skilled personnel.
Continuous training and development programs are necessary to keep the workforce updated with the latest technologies and operational best practices.
Future Trends in Precision Drilling
The future of high-precision drilling in milling is promising, with ongoing technological advancements paving the way for even greater accuracy and efficiency.
Emerging technologies like Artificial Intelligence (AI) and the Internet of Things (IoT) are being integrated into CNC systems, enhancing their capabilities with predictive maintenance and real-time monitoring.
Furthermore, the development of eco-friendly practices and sustainable manufacturing methods is becoming increasingly important in the precision machinery industry.
Design departments must stay ahead of these trends to remain competitive and meet the growing demand for more sustainable practices.
Conclusion
Incorporating high-precision drilling technology is essential for design leaders in the precision machinery industry.
Understanding and leveraging this technology can lead to superior product quality, expanded capabilities, and enhanced manufacturing efficiency.
Staying informed about technological advancements and overcoming implementation challenges will ensure companies remain at the forefront of innovation in their fields.
資料ダウンロード
QCD調達購買管理クラウド「newji」は、調達購買部門で必要なQCD管理全てを備えた、現場特化型兼クラウド型の今世紀最高の購買管理システムとなります。
ユーザー登録
調達購買業務の効率化だけでなく、システムを導入することで、コスト削減や製品・資材のステータス可視化のほか、属人化していた購買情報の共有化による内部不正防止や統制にも役立ちます。
NEWJI DX
製造業に特化したデジタルトランスフォーメーション(DX)の実現を目指す請負開発型のコンサルティングサービスです。AI、iPaaS、および先端の技術を駆使して、製造プロセスの効率化、業務効率化、チームワーク強化、コスト削減、品質向上を実現します。このサービスは、製造業の課題を深く理解し、それに対する最適なデジタルソリューションを提供することで、企業が持続的な成長とイノベーションを達成できるようサポートします。
オンライン講座
製造業、主に購買・調達部門にお勤めの方々に向けた情報を配信しております。
新任の方やベテランの方、管理職を対象とした幅広いコンテンツをご用意しております。
お問い合わせ
コストダウンが利益に直結する術だと理解していても、なかなか前に進めることができない状況。そんな時は、newjiのコストダウン自動化機能で大きく利益貢献しよう!
(Β版非公開)