- お役立ち記事
- Basics and introduction guide for TPM activities that new employees in the equipment technology department should know
Basics and introduction guide for TPM activities that new employees in the equipment technology department should know
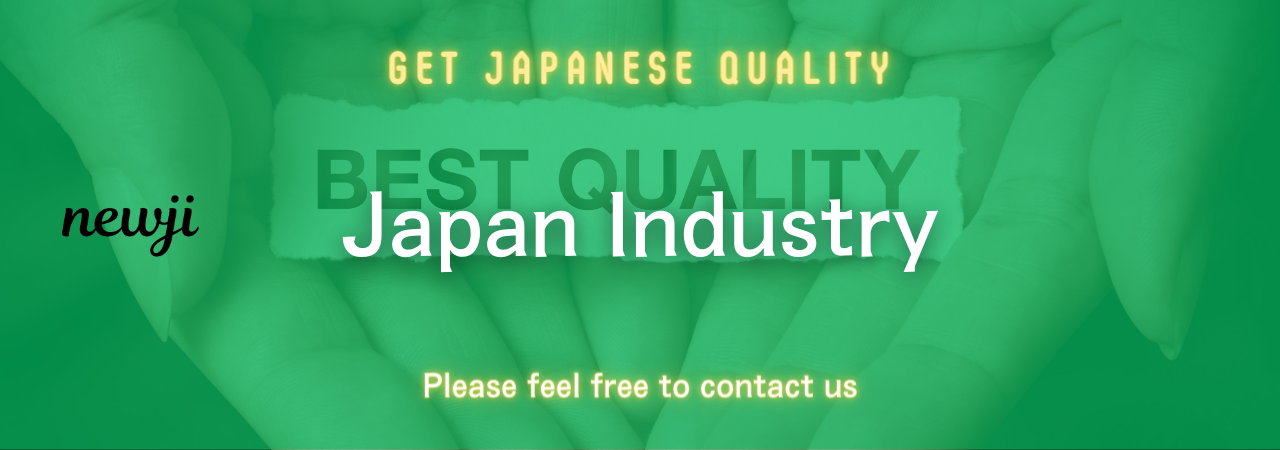
目次
What is TPM?
Total Productive Maintenance, often abbreviated as TPM, is a systematic approach to maintenance that focuses on improving the efficiency and productivity of equipment.
It originated in Japan, where it was developed to enhance manufacturing processes by minimizing downtime and fostering a proactive maintenance culture.
TPM is a holistic system that involves everyone in the organization, from operators to management, in maintaining and optimizing equipment.
The concept is to ensure that machines are in peak operating condition, which in turn reduces breakdowns and increases production capabilities.
The Pillars of TPM
TPM is built on eight fundamental pillars, each of which plays a crucial role in achieving total efficiency in equipment management.
Understanding these pillars is essential for new employees in the equipment technology department.
Autonomous Maintenance
Autonomous maintenance involves operators taking responsibility for the basic upkeep of their equipment.
This includes cleaning, lubricating, and inspecting machines regularly.
By empowering operators to care for their equipment, minor issues can be identified and addressed before they become significant problems.
Planned Maintenance
Planned maintenance focuses on scheduling regular maintenance activities to prevent equipment failures.
This proactive approach ensures that machines remain in optimal condition and helps in forecasting maintenance needs, thus avoiding unexpected breakdowns.
Quality Maintenance
This pillar emphasizes maintaining equipment to produce high-quality products.
Machines are regularly checked and maintained to ensure they meet quality standards, reducing defects and rework.
Focused Improvement
Also known as continuous improvement, this pillar encourages small, incremental changes aimed at enhancing processes and equipment efficiency.
It involves collaborative efforts to identify inefficiencies and implement solutions systematically.
Early Equipment Management
Early equipment management integrates maintenance considerations into the design and installation of new equipment.
This ensures that machines are designed for ease of maintenance, reducing future maintenance time and costs.
Training and Education
Continuous training and education are vital for empowering the workforce with the skills needed for effective maintenance.
This pillar ensures that employees at all levels are knowledgeable about TPM principles and practices.
Safety, Health, and Environment
This pillar focuses on maintaining a safe working environment and ensuring that equipment does not pose any health or environmental risks.
Safety protocols and preventive measures are implemented to minimize accidents and promote a healthy workplace.
TPM in Administration
Extending TPM beyond the shop floor, this pillar involves applying TPM principles to administrative processes.
The aim is to eliminate waste and inefficiencies in office areas, improving overall organizational performance.
The Role of New Employees in TPM
As new employees in the equipment technology department, understanding and participating in TPM activities is crucial.
You will be part of a team responsible for ensuring that machinery operates smoothly and efficiently.
Here’s how you can contribute:
Engaging in Training
Take advantage of training opportunities to learn about TPM principles and how they apply to your role.
Familiarize yourself with the equipment you’ll be working with and understand its maintenance needs.
Participating in Autonomous Maintenance
Get involved in routine maintenance activities, such as cleaning and inspecting equipment.
By taking care of machines, you will develop a deeper understanding of their operation and potential issues.
Contributing to Continuous Improvement
Collaborate with your team to identify areas where processes can be improved.
Your fresh perspective as a new employee can provide valuable insights into potential improvements.
Ensuring Safety and Compliance
Understand and adhere to safety protocols to maintain a safe working environment.
This is crucial not only for your safety but also for the preservation of equipment and the health of your colleagues.
Benefits of Implementing TPM
Incorporating TPM into a company’s operational framework offers numerous benefits.
Reduced Downtime
With regular maintenance and the preventative measures advocated by TPM, equipment failure is minimized, resulting in less downtime and increased production capacity.
Cost Efficiency
By maintaining equipment in optimum condition, companies can reduce repair costs and the need for replacement parts.
This leads to significant savings over time.
Enhanced Equipment Lifespan
Regular maintenance ensures that machines operate efficiently for longer periods, delaying the need for costly replacements.
Improved Product Quality
By focusing on quality maintenance, TPM helps in delivering high-quality products consistently, which in turn enhances customer satisfaction and trust.
Increased Employee Morale
Empowering employees to take ownership of their equipment fosters a sense of responsibility and pride in their work, improving overall job satisfaction.
Conclusion
Total Productive Maintenance is an integral part of modern manufacturing and equipment management.
For new employees in the equipment technology department, understanding TPM is essential to performing their roles effectively.
By engaging with TPM principles, you will help improve equipment reliability, reduce costs, and maintain high standards of product quality.
Embracing TPM not only benefits the organization but also contributes to personal growth and development within the field of equipment technology.
資料ダウンロード
QCD調達購買管理クラウド「newji」は、調達購買部門で必要なQCD管理全てを備えた、現場特化型兼クラウド型の今世紀最高の購買管理システムとなります。
ユーザー登録
調達購買業務の効率化だけでなく、システムを導入することで、コスト削減や製品・資材のステータス可視化のほか、属人化していた購買情報の共有化による内部不正防止や統制にも役立ちます。
NEWJI DX
製造業に特化したデジタルトランスフォーメーション(DX)の実現を目指す請負開発型のコンサルティングサービスです。AI、iPaaS、および先端の技術を駆使して、製造プロセスの効率化、業務効率化、チームワーク強化、コスト削減、品質向上を実現します。このサービスは、製造業の課題を深く理解し、それに対する最適なデジタルソリューションを提供することで、企業が持続的な成長とイノベーションを達成できるようサポートします。
オンライン講座
製造業、主に購買・調達部門にお勤めの方々に向けた情報を配信しております。
新任の方やベテランの方、管理職を対象とした幅広いコンテンツをご用意しております。
お問い合わせ
コストダウンが利益に直結する術だと理解していても、なかなか前に進めることができない状況。そんな時は、newjiのコストダウン自動化機能で大きく利益貢献しよう!
(Β版非公開)