- お役立ち記事
- For quality control leaders in the steel industry! A method to improve the accuracy of complex-shaped parts using 3D inspection
For quality control leaders in the steel industry! A method to improve the accuracy of complex-shaped parts using 3D inspection
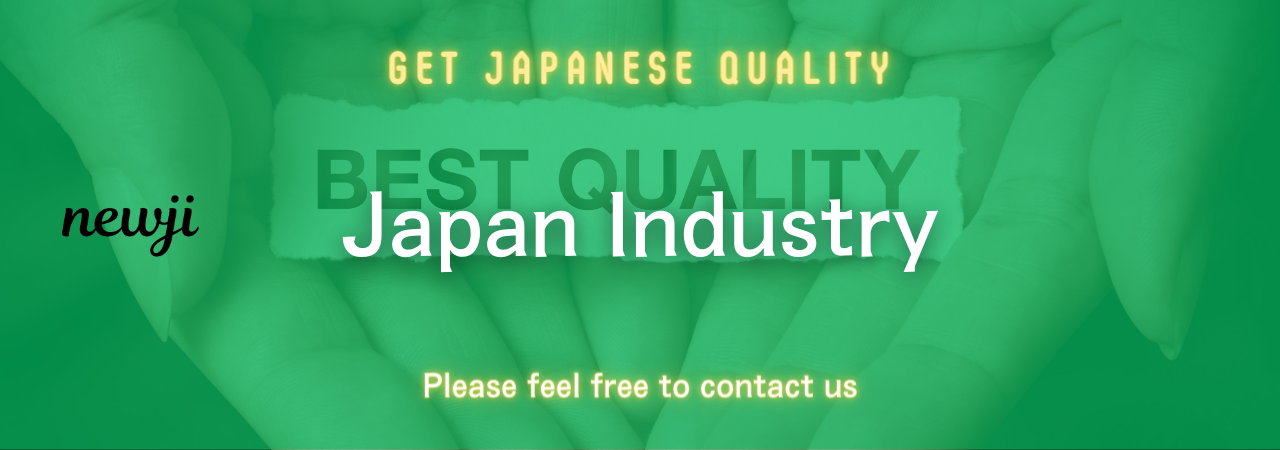
目次
Introduction to 3D Inspection in the Steel Industry
In the fast-paced world of the steel industry, maintaining quality control is crucial, especially when dealing with complex-shaped parts.
The accuracy of these parts can significantly impact performance, safety, and the lifetime of products.
With technological advancements, 3D inspection has emerged as a powerful tool to enhance quality control processes.
3D inspection provides a method to measure and analyze the characteristics of complex surfaces and geometries that traditional methods might miss.
By implementing advanced 3D inspection methods, your team can ensure each part meets stringent quality criteria, reducing waste and improving end-user satisfaction.
Understanding the Importance of Accuracy
In the steel industry, precision is paramount.
From automotive components to machinery parts, exactness ensures safety and functionality.
Errors in complex-shaped parts can lead to failure in critical applications, making inspection and quality control essential.
A small deviation from prescribed specifications can lead to vulnerabilities in the final product.
Quality control leaders recognize the impact that inaccurate parts can have, not only on product integrity but also on company reputation and financial performance.
The Limitations of Traditional Inspection Methods
Traditional inspection methods in the steel industry typically rely on coordinate measuring machines (CMMs) or manual inspections.
While useful, these methods often struggle with complex geometries and can be time-consuming.
Manual inspections are prone to human error, and CMMs, while more accurate, can be inefficient with intricate parts due to limitations in capturing detailed 3D data.
As a result, quality control can suffer, leading to potential defects slipping through the inspection process.
How 3D Inspection Works
3D inspection, often conducted with the help of scanners and software, captures the entire surface of a part in digital form.
This digital model offers a comprehensive view of the part’s geometry, allowing quality control professionals to identify deviations or defects.
These systems use laser or structured light technology, which scans the part in fine detail, providing a complete and precise measurement.
The resulting data can then be compared against the original CAD models to detect any discrepancies.
Advantages of 3D Inspection
1. **Precision**: The ability to capture even the most minute details improves the accuracy of the measurements.
2. **Efficiency**: Faster inspection times without compromising on quality.
3. **Comprehensive Data**: 3D inspection provides a full dataset that can be used for further analysis and process improvement.
4. **Repeatability**: Ensures the same part will consistently meet specifications each time it is produced.
Implementing 3D Inspection in Quality Control
Adopting 3D inspection techniques requires initial investment in technology and training but pays off through enhanced product quality.
Here’s a step-by-step guide to implementing 3D Inspection in your quality control processes:
Steps to Implement 3D Inspection
1. **Evaluate Needs**: Assess which parts and processes require more detailed inspection.
2. **Choose the Right Equipment**: Select 3D scanners and software that fit your specific industrial requirements.
3. **Train Your Team**: Ensure your team is fully trained in using the new technology, focusing on both hardware and software aspects.
4. **Integrate with Existing Systems**: Work towards seamless integration with existing quality control protocols.
5. **Continuous Monitoring and Adjustment**: Regularly evaluate the system’s performance and make necessary adjustments.
Benefits of Improved Quality Control
By using 3D inspection methods, the steel industry can experience several benefits:
1. **Reduced Scrap Rates**: Fewer rejected parts help lower material costs and reduce waste.
2. **Enhanced Product Reliability**: Parts produced with higher precision lead to improved product reliability and performance.
3. **Increased Customer Satisfaction**: Reliable products increase customer trust and brand reputation.
4. **Competitive Edge**: Companies leveraging advanced technologies stay ahead in a competitive market.
Overcoming Challenges
Transitioning to 3D inspection entails overcoming certain challenges.
Cost can be a significant barrier for smaller companies.
Moreover, there is a learning curve associated with the adoption of new technology.
However, these challenges are manageable with strategic planning and phased implementation.
Companies might start with critical parts and gradually extend the technology to other areas as benefits become evident.
Future of 3D Inspection
The future of 3D inspection in the steel industry appears promising.
Ongoing advancements in technology continue to enhance the capabilities and affordability of 3D measurement systems.
Moreover, with the rise of Industry 4.0 and smart manufacturing, integration with other automated systems can further optimize quality control processes.
This evolution will allow for faster, more accurate, and comprehensive inspection routines.
Conclusion
In conclusion, for quality control leaders in the steel industry, 3D inspection forms a critical component in enhancing the precision and efficiency of their operations.
By overcoming conventional inspection limitations, companies can ensure higher quality outcomes, contributing to overall business success.
As the industry moves towards more complex and meticulously designed components, adopting 3D inspection can boost process reliability and remain at the forefront of industrial innovation.
資料ダウンロード
QCD調達購買管理クラウド「newji」は、調達購買部門で必要なQCD管理全てを備えた、現場特化型兼クラウド型の今世紀最高の購買管理システムとなります。
ユーザー登録
調達購買業務の効率化だけでなく、システムを導入することで、コスト削減や製品・資材のステータス可視化のほか、属人化していた購買情報の共有化による内部不正防止や統制にも役立ちます。
NEWJI DX
製造業に特化したデジタルトランスフォーメーション(DX)の実現を目指す請負開発型のコンサルティングサービスです。AI、iPaaS、および先端の技術を駆使して、製造プロセスの効率化、業務効率化、チームワーク強化、コスト削減、品質向上を実現します。このサービスは、製造業の課題を深く理解し、それに対する最適なデジタルソリューションを提供することで、企業が持続的な成長とイノベーションを達成できるようサポートします。
オンライン講座
製造業、主に購買・調達部門にお勤めの方々に向けた情報を配信しております。
新任の方やベテランの方、管理職を対象とした幅広いコンテンツをご用意しております。
お問い合わせ
コストダウンが利益に直結する術だと理解していても、なかなか前に進めることができない状況。そんな時は、newjiのコストダウン自動化機能で大きく利益貢献しよう!
(Β版非公開)