- お役立ち記事
- A must-see for equipment engineers in the precision processing industry! A thorough guide to precision inspection of minute dimensions using ultrasonic measurement
A must-see for equipment engineers in the precision processing industry! A thorough guide to precision inspection of minute dimensions using ultrasonic measurement
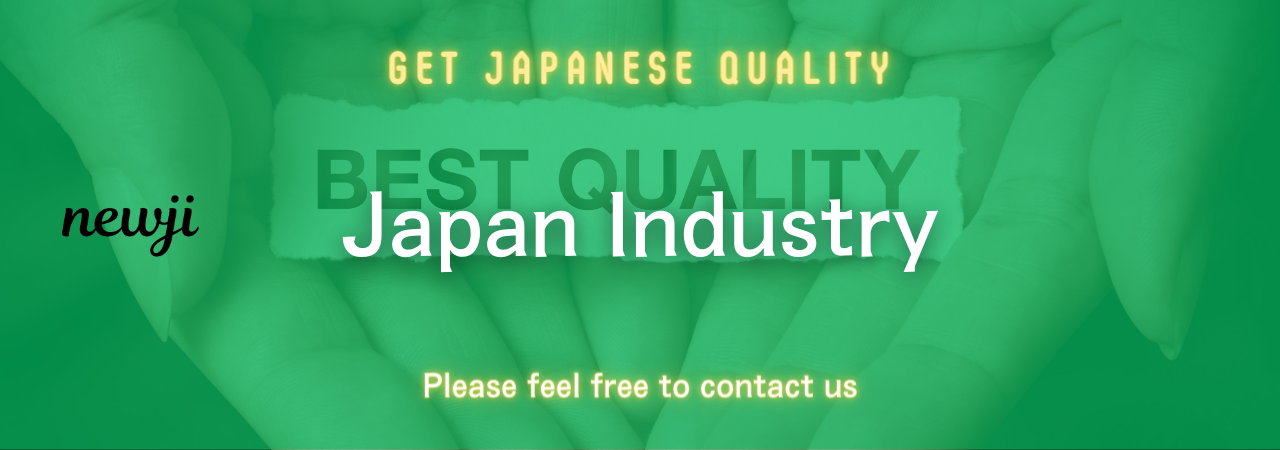
目次
Understanding Ultrasonic Measurement
Ultrasonic measurement is a cutting-edge technique widely used in various industries for precise inspection of minute dimensions.
This non-destructive testing method uses high-frequency sound waves to measure the thickness and dimensions of materials without causing any damage.
It is particularly beneficial for equipment engineers in the precision processing industry, where accuracy and reliability are paramount.
By understanding how ultrasonic measurement works, engineers can ensure precise inspections, ultimately leading to improved product quality and customer satisfaction.
The Basics of Ultrasonic Testing
Ultrasonic testing involves transmitting sound waves into a material and analyzing the reflected signals to determine the material’s properties.
These sound waves typically have frequencies ranging from 1 to 15 MHz, above the human hearing range, which is why they are referred to as ultrasonic waves.
When these waves encounter a boundary, such as a flaw or the back wall of the material, part of the energy is reflected back and can be detected by the equipment.
The time taken for the waves to return, along with the amplitude of the reflected signal, provides valuable information about the material’s thickness, structure, and any internal defects.
Key Advantages of Ultrasonic Measurement
There are several reasons why ultrasonic measurement is advantageous for precision inspection in the processing industry.
Firstly, it is a non-destructive method, which means it does not alter or damage the material being tested.
This is crucial for expensive or delicate components where maintaining integrity is vital.
Secondly, ultrasonic testing offers high precision and accuracy, capable of detecting changes in thickness as small as 0.1 mm.
Additionally, it can inspect complex geometries and assess both surface and internal features, providing a comprehensive view of the material’s condition.
Applications in the Precision Processing Industry
In the precision processing industry, maintaining minute dimensions with high accuracy is essential.
Ultrasonic measurement is employed in several applications where precision is critical.
For instance, it is used in the quality control of components such as turbine blades, pipelines, and automotive parts.
These components often undergo extreme conditions and require flawless manufacturing to ensure durability and performance.
Furthermore, ultrasonic measurement is utilized in the semiconductor industry for inspecting silicon wafers, where even the smallest defect can lead to product failure.
Implementing Ultrasonic Measurement in Inspections
To implement ultrasonic measurement effectively, engineers must select the appropriate equipment and techniques tailored to the specific requirements of their inspection.
The selection depends on various factors including the material type, thickness, and the desired resolution of the measurement.
Common equipment includes flaw detectors, thickness gauges, and phased array systems, each suited for different inspection needs.
Training and expertise in ultrasonic testing are also necessary to correctly interpret the signals and make informed decisions based on the results.
Challenges and Considerations
While ultrasonic measurement offers numerous advantages, engineers must be aware of certain challenges associated with its usage.
Material properties such as grain size, surface roughness, and anisotropy can affect sound wave propagation, potentially leading to inaccurate readings.
Therefore, careful calibration and compensation techniques must be applied to mitigate these effects and ensure reliable measurements.
Moreover, the presence of couplants, which are used to facilitate the transmission of sound waves between the transducer and the test surface, needs careful management to avoid contamination and errors.
The Role of Ultrasonic Measurement in Quality Assurance
Incorporating ultrasonic measurement into quality assurance processes can significantly enhance product reliability and safety.
By detecting defects early in the manufacturing cycle, companies can address issues proactively, reducing waste and rework.
Furthermore, comprehensive data from ultrasonic inspections aid in continuous process improvements, helping to optimize manufacturing methods and material selection.
As a result, engineers can confidently produce components that meet stringent industry standards and customer expectations.
Future Trends in Ultrasonic Measurement Technology
Continued advancements in ultrasonic measurement technology are set to further benefit the precision processing industry.
Developments such as portable devices, improved imaging techniques, and real-time data analysis are making inspections more efficient and accessible.
Moreover, integration with automated systems and the Industrial Internet of Things (IIoT) is anticipated to streamline inspections and provide valuable insights for predictive maintenance.
As technology continues to evolve, ultrasonic measurement will likely play an even more pivotal role in ensuring precision and quality in manufacturing.
By leveraging the power of ultrasonic measurement, equipment engineers in the precision processing industry can achieve unparalleled accuracy in their inspections.
This not only boosts the performance and safety of the products but also enhances the overall efficiency of manufacturing processes.
With a strong understanding and implementation strategy, ultrasonic measurement can be a key tool in any engineer’s arsenal for maintaining the highest standards of precision and quality.
資料ダウンロード
QCD調達購買管理クラウド「newji」は、調達購買部門で必要なQCD管理全てを備えた、現場特化型兼クラウド型の今世紀最高の購買管理システムとなります。
ユーザー登録
調達購買業務の効率化だけでなく、システムを導入することで、コスト削減や製品・資材のステータス可視化のほか、属人化していた購買情報の共有化による内部不正防止や統制にも役立ちます。
NEWJI DX
製造業に特化したデジタルトランスフォーメーション(DX)の実現を目指す請負開発型のコンサルティングサービスです。AI、iPaaS、および先端の技術を駆使して、製造プロセスの効率化、業務効率化、チームワーク強化、コスト削減、品質向上を実現します。このサービスは、製造業の課題を深く理解し、それに対する最適なデジタルソリューションを提供することで、企業が持続的な成長とイノベーションを達成できるようサポートします。
オンライン講座
製造業、主に購買・調達部門にお勤めの方々に向けた情報を配信しております。
新任の方やベテランの方、管理職を対象とした幅広いコンテンツをご用意しております。
お問い合わせ
コストダウンが利益に直結する術だと理解していても、なかなか前に進めることができない状況。そんな時は、newjiのコストダウン自動化機能で大きく利益貢献しよう!
(Β版非公開)