- お役立ち記事
- Quality Function Deployment (QFD) practices that mid-level employees in the quality assurance department of the auto parts manufacturing industry should know
Quality Function Deployment (QFD) practices that mid-level employees in the quality assurance department of the auto parts manufacturing industry should know
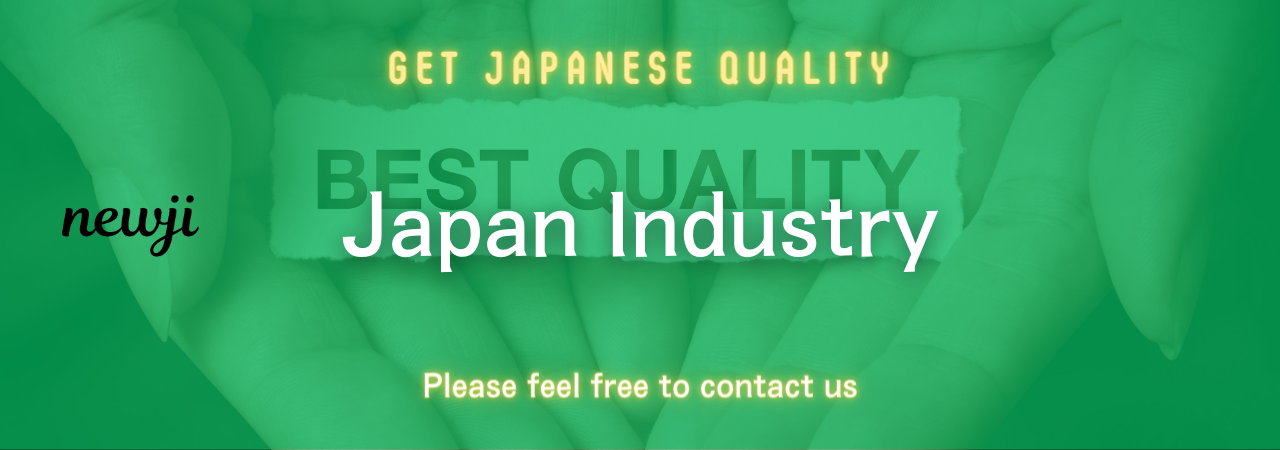
目次
Introduction to Quality Function Deployment (QFD)
Quality Function Deployment (QFD) is a systematic process used to ensure that the wants and needs of customers are accurately understood and met throughout the product development process.
Originating in Japan in the late 1960s, QFD is an essential practice in industries where customer satisfaction and product quality are paramount.
For mid-level employees in the quality assurance (QA) department of the auto parts manufacturing industry, understanding QFD can significantly enhance their contributions to producing superior products that meet customer expectations.
The Importance of QFD in Auto Parts Manufacturing
In the auto parts manufacturing industry, the quality of parts can directly impact the safety and performance of a vehicle.
Thus, it’s crucial to maintain high standards of quality throughout the manufacturing process.
QFD helps in translating customer requirements into specific, measurable project goals, ensuring that each part meets the necessary standards for safety and performance.
By using QFD, QA professionals can systematically approach problems and develop processes that enhance quality and efficiency.
Key Steps in the QFD Process
1. Identify Customer Requirements
The first step in QFD is identifying customer demands, also known as the “Voice of the Customer” (VoC).
This involves gathering detailed information about what customers expect from the product.
Techniques such as surveys, interviews, and focus groups are commonly used to collect this data.
For mid-level QA employees, understanding this step is crucial, as it sets the foundation for developing quality products that resonate with customers.
2. Translate Requirements into Design Qualities
Once customer needs are identified, the next step is to translate these needs into specific design qualities or characteristics of the product.
In the context of auto parts manufacturing, this might involve specifications such as durability, performance, size, or weight.
This translation process is essential because it bridges the gap between customer expectations and engineering capabilities, ensuring that the final product meets or exceeds customer requirements.
3. Develop a Relationship Matrix
The relationship matrix, often referred to as the House of Quality, is a central tool used in QFD.
It helps QA teams understand the relationships between customer requirements and the design qualities of the product.
Constructing this matrix involves evaluating how well each design characteristic satisfies customer needs.
Mid-level QA employees can use this matrix to prioritize features based on their importance and impact, allowing for more focused improvement efforts.
4. Evaluate Competitiveness
A competitive evaluation is crucial in the QFD process to assess how your products stack up against those of competitors.
This can involve benchmarking practices to identify strengths and weaknesses relative to other market players.
By understanding the competitive landscape, QA professionals can identify opportunities for differentiation and develop strategies to improve product features or performance.
5. Develop and Implement Design Improvements
Based on insights gained from the relationship matrix and competitive evaluation, targeted design improvements can be developed and implemented.
For mid-level QA employees, this step involves collaborating closely with design and engineering teams to ensure that proposed changes are feasible and align with customer requirements.
Regular testing and validation are necessary to confirm that modifications enhance product quality without introducing new issues.
Benefits of Implementing QFD in QA Departments
Enhanced Customer Satisfaction
By aligning product development with customer needs, QFD helps ensure that the final product not only meets quality standards but also satisfies customer expectations.
This leads to higher levels of customer satisfaction and can contribute to increased brand loyalty and market success for auto parts manufacturers.
Improved Team Collaboration
QFD requires input and collaboration from multiple departments, including design, engineering, marketing, and quality assurance.
For mid-level QA employees, this collaborative approach can lead to improved communication and teamwork, resulting in more efficient problem-solving and decision-making processes.
Risk Mitigation
By identifying potential issues early in the product development cycle, QFD can help minimize risks associated with product defects or failures.
QA departments can take proactive measures to address these risks, saving time and resources by avoiding costly product recalls or revisions.
Increased Competitive Advantage
In a highly competitive industry like auto parts manufacturing, implementing QFD can provide a significant competitive advantage.
By developing products that consistently meet or exceed customer expectations, manufacturers can differentiate themselves from competitors and capture a larger market share.
Conclusion
For mid-level employees in the quality assurance department of the auto parts manufacturing industry, mastering the principles and practices of Quality Function Deployment is an invaluable skill.
By applying QFD methodologies, these professionals can contribute to the development of high-quality products that meet customer expectations and enhance the organization’s reputation in the market.
As global competition intensifies, the ability to effectively implement QFD will be essential for maintaining a competitive edge and achieving long-term success in the industry.
資料ダウンロード
QCD調達購買管理クラウド「newji」は、調達購買部門で必要なQCD管理全てを備えた、現場特化型兼クラウド型の今世紀最高の購買管理システムとなります。
ユーザー登録
調達購買業務の効率化だけでなく、システムを導入することで、コスト削減や製品・資材のステータス可視化のほか、属人化していた購買情報の共有化による内部不正防止や統制にも役立ちます。
NEWJI DX
製造業に特化したデジタルトランスフォーメーション(DX)の実現を目指す請負開発型のコンサルティングサービスです。AI、iPaaS、および先端の技術を駆使して、製造プロセスの効率化、業務効率化、チームワーク強化、コスト削減、品質向上を実現します。このサービスは、製造業の課題を深く理解し、それに対する最適なデジタルソリューションを提供することで、企業が持続的な成長とイノベーションを達成できるようサポートします。
オンライン講座
製造業、主に購買・調達部門にお勤めの方々に向けた情報を配信しております。
新任の方やベテランの方、管理職を対象とした幅広いコンテンツをご用意しております。
お問い合わせ
コストダウンが利益に直結する術だと理解していても、なかなか前に進めることができない状況。そんな時は、newjiのコストダウン自動化機能で大きく利益貢献しよう!
(Β版非公開)