- お役立ち記事
- How to aim for zero mistakes with pokayoke techniques that new employees in the equipment maintenance department should know
How to aim for zero mistakes with pokayoke techniques that new employees in the equipment maintenance department should know
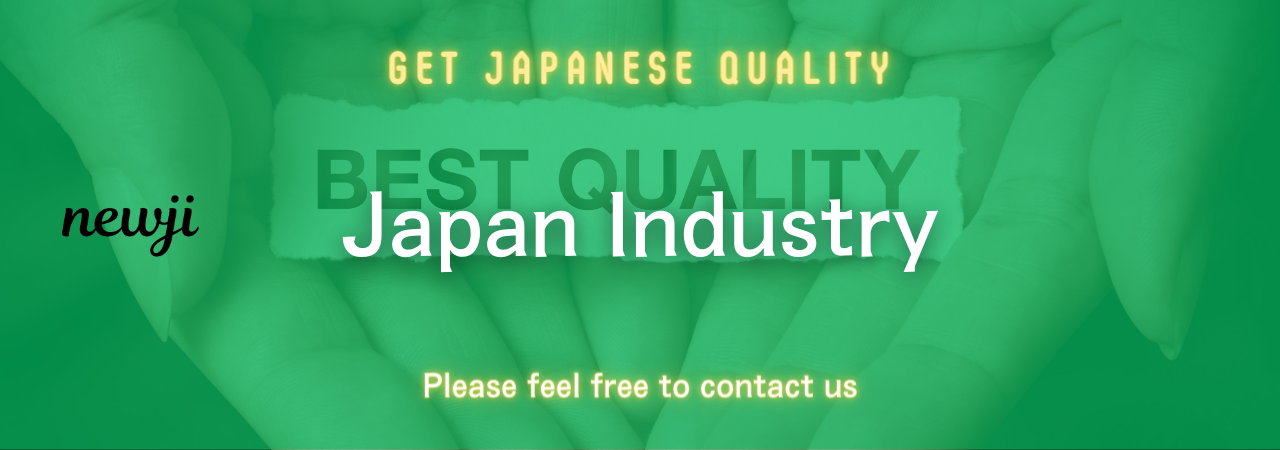
Understanding Pokayoke Techniques
Pokayoke is a Japanese term that translates to “mistake-proofing” or “inadvertent error prevention.”
In equipment maintenance, applying pokayoke techniques helps eliminate errors by designing processes that make mistakes nearly impossible or easily detectable.
For new employees in the equipment maintenance department, understanding and implementing pokayoke techniques can significantly reduce the likelihood of errors, leading to improved efficiency and safety.
The Importance of Pokayoke in Equipment Maintenance
Equipment maintenance involves complex processes that require accuracy and precision.
Mistakes during maintenance can lead to equipment failure, safety hazards, and increased operational costs.
Pokayoke techniques aim to prevent these mistakes by integrating error-proofing features into the maintenance process.
For new employees, learning these techniques can help minimize human errors and ensure that the equipment operates smoothly.
Common Types of Pokayokes
There are several types of pokayokes that can be implemented in equipment maintenance.
The most common ones include:
1. **Prevention Pokayokes**: These are designed to prevent errors before they occur.
For instance, color-coded tags that help new employees identify the correct parts or tools needed for a job.
2. **Detection Pokayokes**: These identify errors that have already occurred so they can be corrected immediately.
An example is sensors that alert when a part is misaligned.
3. **Facilitative Pokayokes**: These make it easy to perform tasks correctly by simplifying the process.
This can include guides or jigs that ensure components fit together only one way.
Understanding these types can help new employees select the right pokayoke techniques for different tasks.
Implementing Pokayoke in Equipment Maintenance
When new employees in the equipment maintenance department start implementing pokayoke, they should follow several steps to ensure effective error-proofing:
1. **Identify Common Errors**: Start by conducting an analysis of the maintenance process to identify where mistakes frequently occur.
This analysis will guide the selection of appropriate pokayoke techniques.
2. **Design and Apply Pokayokes**: Once errors have been identified, the next step is designing pokayoke elements that target these issues.
This could involve simple solutions, such as checklists, or more complex interventions, like automated alerts.
3. **Test Effectiveness**: After implementation, it’s essential to test the effectiveness of the pokayoke measures.
Regular reviews can help determine if adjustments are needed or if additional measures should be implemented.
4. **Educate and Train Staff**: Ensuring that all staff, especially new employees, understand the purpose and functionality of pokayoke systems is vital.
Training sessions that demonstrate how these techniques prevent errors can maximize their impact.
Benefits of Using Pokayoke Techniques
Integrating pokayoke techniques into the maintenance process offers numerous advantages.
Firstly, it enhances reliability because reducing errors significantly decreases equipment downtime.
This leads to more consistent performance and productivity.
Safety is another critical benefit.
Error prevention means fewer risks related to equipment mishandling or malfunctions.
This is particularly important for new employees who might be less familiar with the equipment.
Moreover, using pokayoke techniques can improve job satisfaction among maintenance staff.
By reducing the stress of potential errors, employees can focus on efficient performance.
Lastly, implementing pokayoke techniques can contribute to cost savings by minimizing waste and avoiding costly repairs from continued equipment errors.
Challenges in Pokayoke Implementation
Despite its benefits, implementing pokayoke techniques comes with challenges.
New employees may find it hard to fully grasp the concept without practical experience.
Moreover, some pokayoke solutions may require additional resources, including time and budget for design, development, and installation.
Resistance to change can also be a barrier, as employees accustomed to older methods may initially be reluctant to adopt new systems.
Overcoming these challenges involves a commitment to ongoing training, fostering a culture that values continuous improvement, and leveraging leadership support to champion pokayoke practices.
Conclusion
For new employees in the equipment maintenance department, embracing pokayoke techniques can be a game-changer in achieving zero mistakes.
By designing systems that inherently prevent or quickly detect errors, maintenance processes become more efficient, safe, and cost-effective.
Through education, practice, and regular evaluations, pokayoke becomes a foundational component of equipment maintenance, ultimately leading to a more robust and error-free operation.
資料ダウンロード
QCD調達購買管理クラウド「newji」は、調達購買部門で必要なQCD管理全てを備えた、現場特化型兼クラウド型の今世紀最高の購買管理システムとなります。
ユーザー登録
調達購買業務の効率化だけでなく、システムを導入することで、コスト削減や製品・資材のステータス可視化のほか、属人化していた購買情報の共有化による内部不正防止や統制にも役立ちます。
NEWJI DX
製造業に特化したデジタルトランスフォーメーション(DX)の実現を目指す請負開発型のコンサルティングサービスです。AI、iPaaS、および先端の技術を駆使して、製造プロセスの効率化、業務効率化、チームワーク強化、コスト削減、品質向上を実現します。このサービスは、製造業の課題を深く理解し、それに対する最適なデジタルソリューションを提供することで、企業が持続的な成長とイノベーションを達成できるようサポートします。
オンライン講座
製造業、主に購買・調達部門にお勤めの方々に向けた情報を配信しております。
新任の方やベテランの方、管理職を対象とした幅広いコンテンツをご用意しております。
お問い合わせ
コストダウンが利益に直結する術だと理解していても、なかなか前に進めることができない状況。そんな時は、newjiのコストダウン自動化機能で大きく利益貢献しよう!
(Β版非公開)