- お役立ち記事
- For managers of production technology departments in the plastic molding industry! In-mold labeling (IML) technology implementation example
For managers of production technology departments in the plastic molding industry! In-mold labeling (IML) technology implementation example
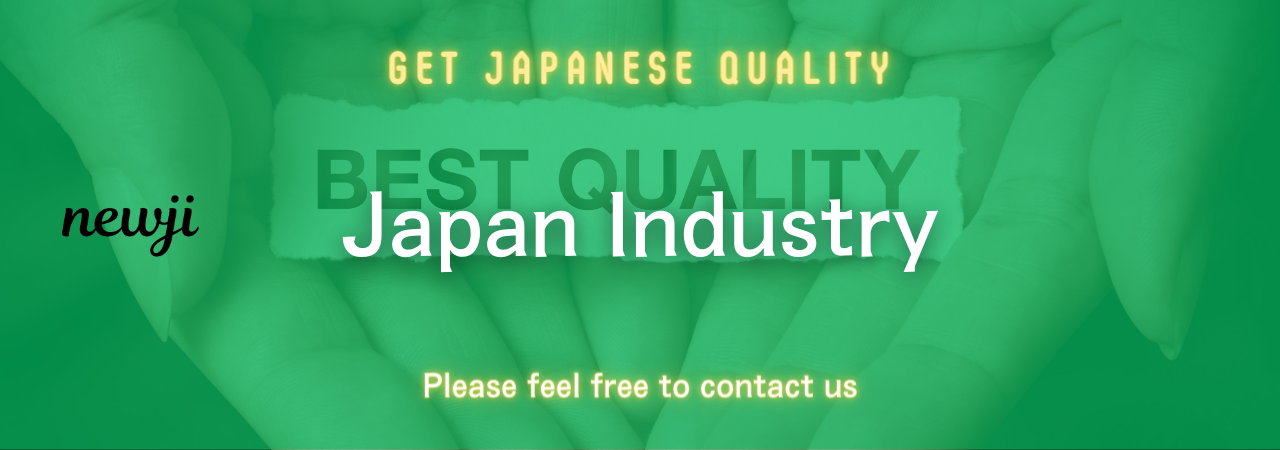
目次
Understanding In-Mold Labeling (IML) Technology
In the fast-paced world of plastic molding, staying ahead of the competition is crucial.
One significant innovation that has been a game-changer is In-Mold Labeling (IML) technology.
IML integrates the decoration or labeling of plastic products during the manufacturing process.
This technology not only enhances the appearance of the products but also offers a more efficient production process.
IML is performed by placing a pre-printed label inside the mold cavity.
When the molten plastic is injected into the mold, it fuses with the label, creating a seamless product.
This process eliminates the need for post-production decorating, reducing the time and cost associated with traditional labeling methods.
Benefits of In-Mold Labeling
For production technology departments, integrating IML technology offers several benefits.
Firstly, IML ensures high-quality, durable labels that are resistant to scratches, moisture, and extreme temperatures.
This longevity is crucial for products exposed to harsh environments or requiring a pristine appearance throughout their lifespan.
Moreover, IML provides unlimited design possibilities.
Labels can be produced with stunning graphics, vibrant colors, and detailed information, enhancing the overall appeal of the product.
It also offers the flexibility to change designs swiftly without disrupting the production process.
Another significant advantage is cost efficiency.
By consolidating molding and labeling into one step, manufacturers can reduce material usage and energy consumption, leading to lower production costs.
Additionally, IML reduces the waste associated with traditional adhesive labels, aligning with sustainable manufacturing practices.
Practical Implementation of IML Technology
Implementing IML technology in a production setting requires careful planning and consideration.
Here’s an example of practical steps to successfully integrate IML into your plastic molding process:
Step 1: Assess Compatibility
Before introducing IML, assess the compatibility of your existing machinery.
Ensure that your injection molding equipment can accommodate the IML process.
In some cases, minor modifications or new technology integration may be necessary to support the IML operation.
Step 2: Select the Right Materials
Choosing the appropriate materials is crucial for successful IML.
The labels used in IML must be compatible with the type of plastic being molded.
Labels are typically made from polypropylene (PP) or polyethylene (PE), as these materials provide the best adhesion and durability with most plastics.
Step 3: Partner with Experts
Partnering with experienced IML technology providers can greatly streamline the implementation process.
These experts can offer guidance on selecting the right equipment and materials, as well as provide training for your team.
Their expertise can help ensure a smooth transition to IML technology in your manufacturing processes.
Step 4: Pilot Test
Before full-scale implementation, conduct a pilot test.
This test will help identify any potential issues and provide insights into optimizing the process.
Collect data on production speed, label adhesion quality, and overall efficiency.
Use this information to make necessary adjustments before rolling out IML across all production lines.
Step 5: Quality Control
Implement rigorous quality control measures to ensure the integrity of the labeling on finished products.
Regularly inspect the bond between the label and the plastic to verify that it meets the desired strength and durability.
This commitment to quality will build trust with customers and reinforce your brand’s reputation.
Overcoming Challenges
Although IML technology offers numerous advantages, challenges may arise during implementation.
One common hurdle is the initial investment cost for new equipment and technology upgrades.
However, the long-term savings in materials, labor, and improved product quality often offset this cost.
Another challenge is ensuring that the labels used are environmentally friendly and comply with industry standards.
Collaborating with suppliers who share a commitment to sustainable practices can help address this concern.
Conclusion
In-Mold Labeling (IML) technology represents a revolutionary advancement in the plastic molding industry.
By seamlessly integrating the labeling process into manufacturing, IML offers a multitude of benefits, including enhanced product quality, design flexibility, and cost efficiency.
For managers of production technology departments, embracing IML technology can lead to more sustainable manufacturing practices and gain a competitive edge in the market.
By following practical implementation steps and overcoming potential challenges, the transition to IML can be a smooth and profitable venture.
With the right strategy and partnerships, introducing IML technology to your plastic molding operations can significantly enhance the efficiency and marketability of your products, paving the way for future success in the industry.
資料ダウンロード
QCD調達購買管理クラウド「newji」は、調達購買部門で必要なQCD管理全てを備えた、現場特化型兼クラウド型の今世紀最高の購買管理システムとなります。
ユーザー登録
調達購買業務の効率化だけでなく、システムを導入することで、コスト削減や製品・資材のステータス可視化のほか、属人化していた購買情報の共有化による内部不正防止や統制にも役立ちます。
NEWJI DX
製造業に特化したデジタルトランスフォーメーション(DX)の実現を目指す請負開発型のコンサルティングサービスです。AI、iPaaS、および先端の技術を駆使して、製造プロセスの効率化、業務効率化、チームワーク強化、コスト削減、品質向上を実現します。このサービスは、製造業の課題を深く理解し、それに対する最適なデジタルソリューションを提供することで、企業が持続的な成長とイノベーションを達成できるようサポートします。
オンライン講座
製造業、主に購買・調達部門にお勤めの方々に向けた情報を配信しております。
新任の方やベテランの方、管理職を対象とした幅広いコンテンツをご用意しております。
お問い合わせ
コストダウンが利益に直結する術だと理解していても、なかなか前に進めることができない状況。そんな時は、newjiのコストダウン自動化機能で大きく利益貢献しよう!
(Β版非公開)