- お役立ち記事
- For leaders of quality control departments in the auto parts manufacturing industry! Thorough traceability and early detection of quality problems
For leaders of quality control departments in the auto parts manufacturing industry! Thorough traceability and early detection of quality problems
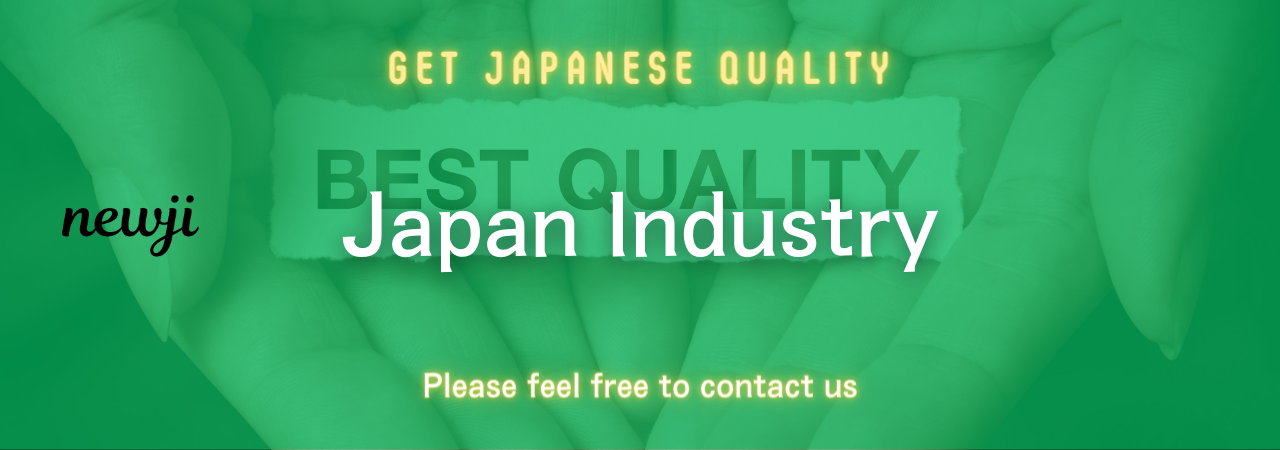
目次
Understanding Traceability in Auto Parts Manufacturing
In the auto parts manufacturing industry, ensuring the quality of components is paramount.
Quality control leaders are at the forefront of this mission, tasked with maintaining the highest standards and swiftly identifying any issues that may arise.
One of the key strategies employed in achieving this is traceability.
Traceability refers to the ability to track every part and process involved in the production chain, from the raw materials to the finished product.
This comprehensive tracking allows manufacturers to pinpoint the source of any defects and address them with minimal disruption.
For those leading quality control departments, mastering traceability is essential.
It not only ensures product reliability but also builds trust with customers and meets industry regulations.
The Importance of Effective Traceability
Effective traceability in auto parts manufacturing serves several critical functions.
Firstly, it enhances accountability throughout the supply chain.
When every component is tracked, it becomes easier to identify who is responsible if a defect is detected.
This accountability discourages mistakes and promotes a culture of quality.
Secondly, traceability allows for efficient recalls.
In the event that a malfunctioning part is discovered, manufacturers can quickly identify affected products and streamline the recall process.
This capability minimizes damage to brand reputation and protects consumers.
Additionally, traceability supports regulatory compliance.
Automotive manufacturers operate under strict standards and regulations.
Maintaining thorough records of the production process helps demonstrate compliance with these requirements, avoiding potential penalties or legal issues.
Implementing a Traceability System
Developing a robust traceability system requires a strategic approach.
The first step is selecting the right technology.
Barcode scanning, Radio Frequency Identification (RFID), and blockchain are commonly used technologies that facilitate the tracking of parts and materials.
Each offers different advantages; for example, RFID tags enable real-time data collection, while blockchain ensures data integrity.
Next, integrate traceability into the existing workflow.
This involves updating standard operating procedures and training staff to use new tools effectively.
It is crucial that all employees, from the production floor to the executive level, understand the importance of traceability.
Communication is key.
Data collected should be shared across departments to foster collaboration and proactive problem-solving.
Furthermore, it is essential to maintain accurate records.
Detailed documentation of every step in the production chain will support swift identification of quality issues.
Regular audits and inspections can help ensure that data remains reliable and up-to-date.
Early Detection of Quality Problems
One of the primary objectives for leaders in quality control is the early detection of quality problems.
Catching issues before they escalate can save time, reduce costs, and maintain the company’s reputation.
Utilizing advanced data analysis tools allows manufacturers to identify patterns that suggest potential defects.
Predictive analytics, for example, can provide insights by assessing the performance of parts over time.
This proactive approach enables teams to address minor issues before they develop into significant problems.
In addition, incorporating sensors within manufacturing equipment can offer real-time monitoring.
These sensors can detect anomalies during the production process, alerting operators to possible defects.
This capability allows for immediate intervention and correction.
Another effective strategy is fostering a strong feedback loop.
Encouraging customer feedback provides valuable insights into product performance and quality.
Analyzing warranty claims, service requests, and customer reviews can highlight areas needing improvement.
Building a Quality-First Culture
To effectively manage quality, it is crucial to build a culture centered around excellence.
This starts with leadership.
When leaders prioritize quality, it sets the tone for the entire organization.
They should consistently communicate the importance of quality control and recognize employees who uphold these standards.
Training and development programs are also vital.
Offering continuous learning opportunities ensures that staff remain informed of the latest quality assurance techniques and trends.
Creating an environment where employees feel empowered to suggest improvements and report concerns can significantly enhance the quality control process.
A transparent and collaborative atmosphere enables faster detection of issues and fosters innovation in problem-solving.
Harnessing Technology for Quality Assurance
Technology plays a pivotal role in modern quality control.
Advanced software systems provide comprehensive solutions for monitoring and managing quality across manufacturing processes.
For instance, Quality Management Systems (QMS) offer centralized platforms for tracking metrics, managing documentation, and coordinating audits.
These systems streamline the workflow, enhance communication, and ensure compliance with industry standards.
Moreover, automation is transforming quality control.
Automated inspections using machine learning algorithms can quickly and accurately detect defects, reducing the reliance on manual checks.
This not only increases efficiency but also improves precision.
Embracing digital transformation helps manufacturers stay competitive in a rapidly evolving market.
By adopting cutting-edge technologies, auto parts producers can maintain their commitment to quality while optimizing production.
Conclusion
For leaders in quality control departments, mastering traceability and early detection of quality problems is fundamental to success in the auto parts manufacturing industry.
By implementing a robust traceability system, fostering a quality-first culture, and leveraging advanced technologies, manufacturers can ensure the highest standards are met.
These practices not only safeguard product integrity but also strengthen customer trust and enhance the company’s reputation.
In an industry as critical as automotive manufacturing, a proactive and vigilant approach to quality control is an invaluable asset.
資料ダウンロード
QCD調達購買管理クラウド「newji」は、調達購買部門で必要なQCD管理全てを備えた、現場特化型兼クラウド型の今世紀最高の購買管理システムとなります。
ユーザー登録
調達購買業務の効率化だけでなく、システムを導入することで、コスト削減や製品・資材のステータス可視化のほか、属人化していた購買情報の共有化による内部不正防止や統制にも役立ちます。
NEWJI DX
製造業に特化したデジタルトランスフォーメーション(DX)の実現を目指す請負開発型のコンサルティングサービスです。AI、iPaaS、および先端の技術を駆使して、製造プロセスの効率化、業務効率化、チームワーク強化、コスト削減、品質向上を実現します。このサービスは、製造業の課題を深く理解し、それに対する最適なデジタルソリューションを提供することで、企業が持続的な成長とイノベーションを達成できるようサポートします。
オンライン講座
製造業、主に購買・調達部門にお勤めの方々に向けた情報を配信しております。
新任の方やベテランの方、管理職を対象とした幅広いコンテンツをご用意しております。
お問い合わせ
コストダウンが利益に直結する術だと理解していても、なかなか前に進めることができない状況。そんな時は、newjiのコストダウン自動化機能で大きく利益貢献しよう!
(Β版非公開)