- お役立ち記事
- For process engineers in the semiconductor industry! High precision and process control of ion beam etching
For process engineers in the semiconductor industry! High precision and process control of ion beam etching
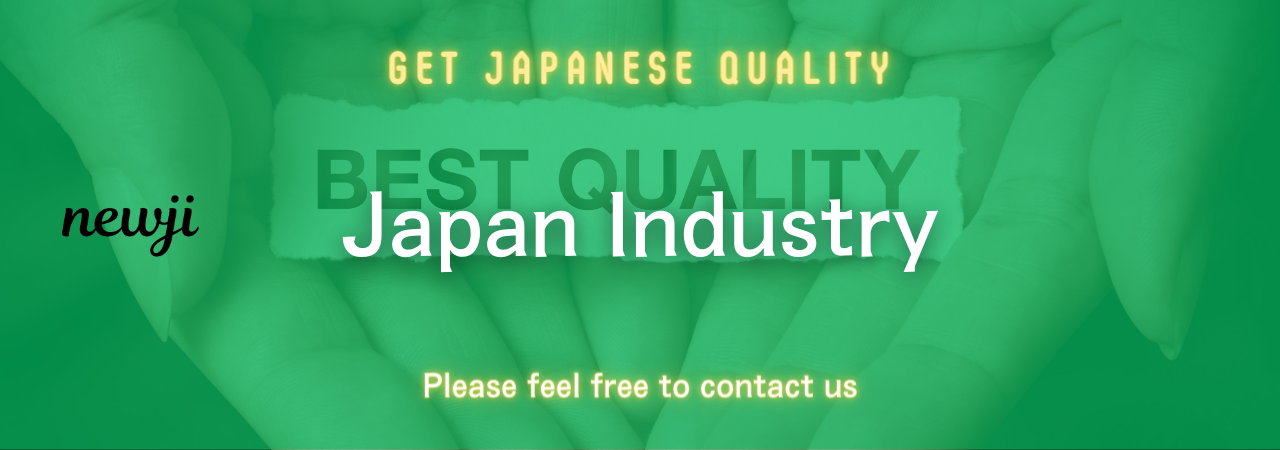
目次
Introduction to Ion Beam Etching in the Semiconductor Industry
Ion beam etching is a critical process in semiconductor manufacturing, known for its high precision and exceptional control.
With the continuous advancement in semiconductor technology, process engineers are always looking for ways to enhance efficiency and accuracy.
Ion beam etching stands out as a preferred technique, offering unique advantages over other etching methods.
This process involves the removal of material from substrates using a directed stream of ions, allowing for intricate and precise designs to be manufactured at micro and nano scales.
The Importance of Precision in Semiconductor Manufacturing
In the semiconductor industry, precision is paramount.
As integrated circuits and microchips become ever smaller and more complex, maintaining tight control over manufacturing processes is essential.
Ion beam etching provides the precision needed to accurately define minute features without compromising on the quality of the semiconductors.
This precision is crucial in applications ranging from consumer electronics to aerospace and automotive technologies, where performance is heavily dependent on the precise architecture of semiconductor components.
How Ion Beam Etching Works
Ion beam etching operates by directing ions towards a substrate to physically remove material.
This removal process can be finely tuned to achieve the desired pattern or shape.
The ions are generated in an ion source, typically a plasma, and accelerated in a high-voltage electric field.
The resulting ion beam strikes the surface of the material in a controlled fashion, allowing for the precise definition of patterns.
The process can be adjusted by changing parameters such as ion energy, angle of incidence, and beam composition, contributing to the high level of process control offered by ion beam etching.
Advantages of Ion Beam Etching in Process Control
Ion beam etching offers several advantages that make it ideal for applications requiring high precision and control.
Pattern Versatility and Fidelity
One of the standout benefits of ion beam etching is its ability to produce patterns with high fidelity.
This means that the etched features closely match the intended design.
Unlike other etching methods, which rely on chemical reactions that can undercut or err from the specified pattern, ion beam etching removes material through direct physical processes.
This significantly reduces deviations and enhances the accuracy of intricate designs.
Material Versatility
Ion beam etching is versatile and can be used with a wide range of materials.
This includes both conductive and non-conductive materials like metals, dielectrics, and semiconductors.
The technique’s broad applicability makes it suitable for a diverse array of applications in the semiconductor sector, from microelectromechanical systems (MEMS) to advanced optics and more.
Controlled Anisotropic Etching
Anisotropic etching is often desired in semiconductor manufacturing because it allows for the creation of geometric features with specific orientations and depths.
Ion beam etching can achieve anisotropic profiles by precisely controlling the direction of the ion beam.
This characteristic is particularly beneficial in applications where the cross-sectional shape of etched features directly impacts the performance of the semiconductor device.
Challenges and Innovations in Ion Beam Etching
Despite its numerous benefits, ion beam etching is not without its challenges.
Process Complexity and Equipment Costs
One of the primary challenges associated with ion beam etching is the complexity of the process.
Achieving high precision requires sophisticated equipment and meticulous process control, which can entail significant costs.
However, continuous innovations in equipment design and process automation have been making ion beam etching more accessible and efficient.
Reducing Damage to Substrates
The high-energy ions used in ion beam etching have the potential to cause damage to the substrate, which can affect the performance of the final semiconductor product.
To mitigate this, recent advancements focus on optimizing ion energy and minimizing the impact energy on the substrate.
Developments in mask technology and the use of sacrificial layers are also being employed to protect sensitive layers from unintentional damage.
The Future of Ion Beam Etching in Semiconductors
As the semiconductor industry demands increasingly smaller and more powerful chips, the role of ion beam etching is expected to grow.
Future advancements are likely to focus on enhancing etch precision and expanding the range of applicable materials.
Integration with Other Technologies
Ion beam etching is being integrated with other advanced technologies, such as machine learning and artificial intelligence, to boost process control and defect detection capabilities.
By analyzing large datasets, these technologies can predict and compensate for deviations in real-time, resulting in improved yield and reduced waste.
Eco-Friendly Practices
With an increased emphasis on sustainability, the semiconductor industry is exploring eco-friendly practices, including ion beam etching.
This entails reducing the environmental footprint by optimizing energy consumption and minimizing waste generation.
Future ion beam etching processes are expected to incorporate green technologies to align with global sustainability initiatives.
Conclusion
Ion beam etching remains a cornerstone technology in semiconductor manufacturing.
Its high precision and exceptional process control make it invaluable in the development of next-generation devices.
As challenges are addressed and technological innovations continue, ion beam etching is set to play an even more significant role in pushing the boundaries of what is possible in the semiconductor industry.
For process engineers, staying abreast of developments in this area will be essential to ensure continued success and competitiveness in the fast-evolving tech landscape.
資料ダウンロード
QCD調達購買管理クラウド「newji」は、調達購買部門で必要なQCD管理全てを備えた、現場特化型兼クラウド型の今世紀最高の購買管理システムとなります。
ユーザー登録
調達購買業務の効率化だけでなく、システムを導入することで、コスト削減や製品・資材のステータス可視化のほか、属人化していた購買情報の共有化による内部不正防止や統制にも役立ちます。
NEWJI DX
製造業に特化したデジタルトランスフォーメーション(DX)の実現を目指す請負開発型のコンサルティングサービスです。AI、iPaaS、および先端の技術を駆使して、製造プロセスの効率化、業務効率化、チームワーク強化、コスト削減、品質向上を実現します。このサービスは、製造業の課題を深く理解し、それに対する最適なデジタルソリューションを提供することで、企業が持続的な成長とイノベーションを達成できるようサポートします。
オンライン講座
製造業、主に購買・調達部門にお勤めの方々に向けた情報を配信しております。
新任の方やベテランの方、管理職を対象とした幅広いコンテンツをご用意しております。
お問い合わせ
コストダウンが利益に直結する術だと理解していても、なかなか前に進めることができない状況。そんな時は、newjiのコストダウン自動化機能で大きく利益貢献しよう!
(Β版非公開)