- お役立ち記事
- A must-see for managers of production technology departments in the electronic equipment manufacturing industry! Latest trends in BGA (Ball Grid Array) rework technology
A must-see for managers of production technology departments in the electronic equipment manufacturing industry! Latest trends in BGA (Ball Grid Array) rework technology
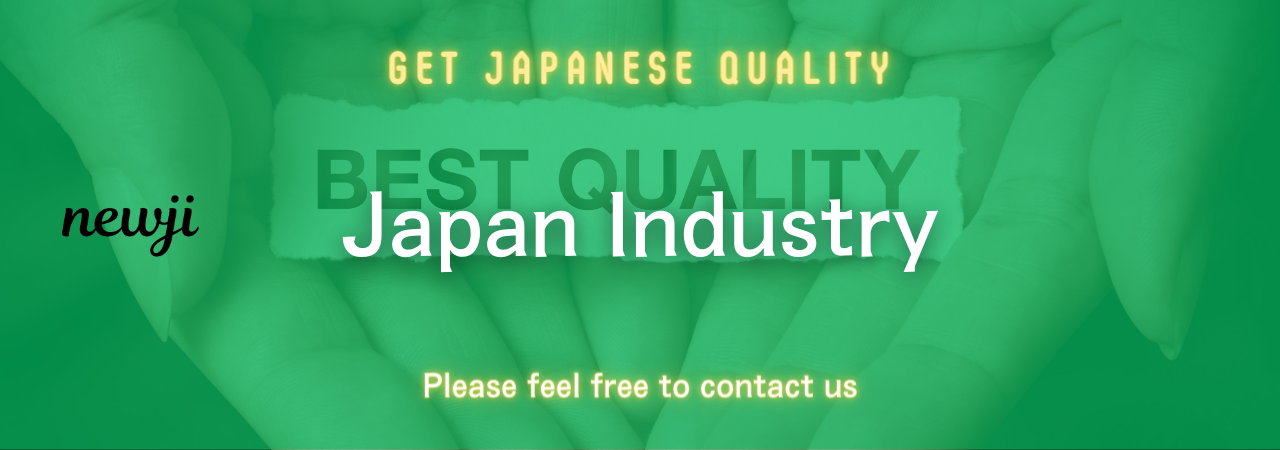
目次
Introduction to BGA Rework Technology
Ball Grid Array (BGA) technology is a pivotal component of modern electronic manufacturing.
It provides a connection between a device and its circuit board with high efficiency and compact design.
For managers in production technology departments, staying updated with the latest advancements in BGA rework technology is essential.
The ability to effectively manage and repair BGAs can significantly influence production costs, time, and ultimately, product quality.
Understanding BGA Rework
To fully utilize BGA technology, it’s essential to have a firm understanding of BGA rework.
BGA rework involves the process of removing, replacing, or repairing a BGA component on a printed circuit board (PCB).
This can be necessary due to defects in the initial manufacturing process, design changes, or functionality issues that arise after the product is in use.
Given the small size and critical nature of these components, precise rework techniques are essential.
The Importance of Precision in BGA Rework
Precision is the cornerstone of effective BGA rework.
The complexity of removing and replacing a BGA lies in the array of solder balls, which serve as the contact points to the board.
Each of these solder joints must be individually reflowed and aligned to ensure a reliable connection.
Mistakes in this process can lead to circuit failures, impacting the performance of the entire device.
Advanced Techniques for BGA Rework
Recent advancements in BGA rework technology focus on enhancing the precision and efficiency of the rework process.
Among these innovations, laser rework systems stand out.
These systems use concentrated beams of light to accurately heat specific areas of the PCB, allowing for precise removal and replacement of BGA components.
Laser rework systems reduce the thermal stress on the board and nearby components, minimizing the risk of damage.
Benefits of Using Laser Rework Systems
Laser rework systems represent a significant improvement over traditional hot-air rework methods.
They offer higher precision, less thermal influence on other board areas, and the ability to automate processes.
This leads to lower error rates and higher throughput in production, which are critical factors for maintaining competitiveness in the electronic equipment manufacturing industry.
Incorporating Automation in BGA Rework
Automation is rapidly transforming every aspect of manufacturing, and BGA rework is no exception.
Automated rework stations have become increasingly prevalent, leveraging robotic arms and machine learning algorithms to enhance precision and efficiency.
These systems can automatically recognize and align components, apply the necessary heat for reflow, and inspect the quality of connections post-removal or replacement.
The Role of AI in Automated BGA Rework
Artificial Intelligence (AI) plays a crucial role in optimizing automated rework systems.
Through machine learning, AI can improve the accuracy of component placement and adhere inspection procedures to maintain high standards.
By analyzing vast amounts of data from previous rework operations, AI can predict potential failure points and adjust parameters accordingly, ensuring higher success rates.
Challenges in BGA Rework and Solutions
Despite technological advancements, BGA rework remains a challenging process.
Common issues include improper alignment of BGAs during replacement, overheating or underheating during soldering, and incomplete solder joint formation.
Employing state-of-the-art inspection technologies, such as X-ray inspection and optical recognition systems, can help overcome these challenges by offering real-time feedback and quality control.
X-Ray Inspection and Its Advantages
X-ray inspection systems provide unparalleled visibility into the connections under a BGA package.
They allow manufacturers to view the internal solder joints without physical interference, ensuring correct ball placement and solid connections.
This non-destructive testing method is vital for preventing product failures and ensuring the reliability of electronic devices.
Future Outlook for BGA Rework Technology
The future of BGA rework technology is promising, driven by continuous innovation and the growing demand for more compact, powerful electronic devices.
Nanotechnology might soon play a role in further miniaturizing components and improving rework precision.
Moreover, advancements in materials science promise to yield new solder materials that can withstand higher temperatures and more cycles of heating and cooling.
Conclusion
Keeping abreast of the latest trends in BGA rework technology is critical for managers in the electronic equipment manufacturing industry.
As technology progresses, those who adapt and invest in advanced rework processes will enjoy increased production efficiency and product quality.
By understanding and implementing these cutting-edge practices, technology managers can ensure their factories remain competitive and continue to meet the ever-evolving demands of the electronics market.
資料ダウンロード
QCD調達購買管理クラウド「newji」は、調達購買部門で必要なQCD管理全てを備えた、現場特化型兼クラウド型の今世紀最高の購買管理システムとなります。
ユーザー登録
調達購買業務の効率化だけでなく、システムを導入することで、コスト削減や製品・資材のステータス可視化のほか、属人化していた購買情報の共有化による内部不正防止や統制にも役立ちます。
NEWJI DX
製造業に特化したデジタルトランスフォーメーション(DX)の実現を目指す請負開発型のコンサルティングサービスです。AI、iPaaS、および先端の技術を駆使して、製造プロセスの効率化、業務効率化、チームワーク強化、コスト削減、品質向上を実現します。このサービスは、製造業の課題を深く理解し、それに対する最適なデジタルソリューションを提供することで、企業が持続的な成長とイノベーションを達成できるようサポートします。
オンライン講座
製造業、主に購買・調達部門にお勤めの方々に向けた情報を配信しております。
新任の方やベテランの方、管理職を対象とした幅広いコンテンツをご用意しております。
お問い合わせ
コストダウンが利益に直結する術だと理解していても、なかなか前に進めることができない状況。そんな時は、newjiのコストダウン自動化機能で大きく利益貢献しよう!
(Β版非公開)