- お役立ち記事
- A must-see for managers of quality assurance departments in the apparel manufacturing industry! Shrinkage ratio test and countermeasures to ensure dimensional stability
A must-see for managers of quality assurance departments in the apparel manufacturing industry! Shrinkage ratio test and countermeasures to ensure dimensional stability
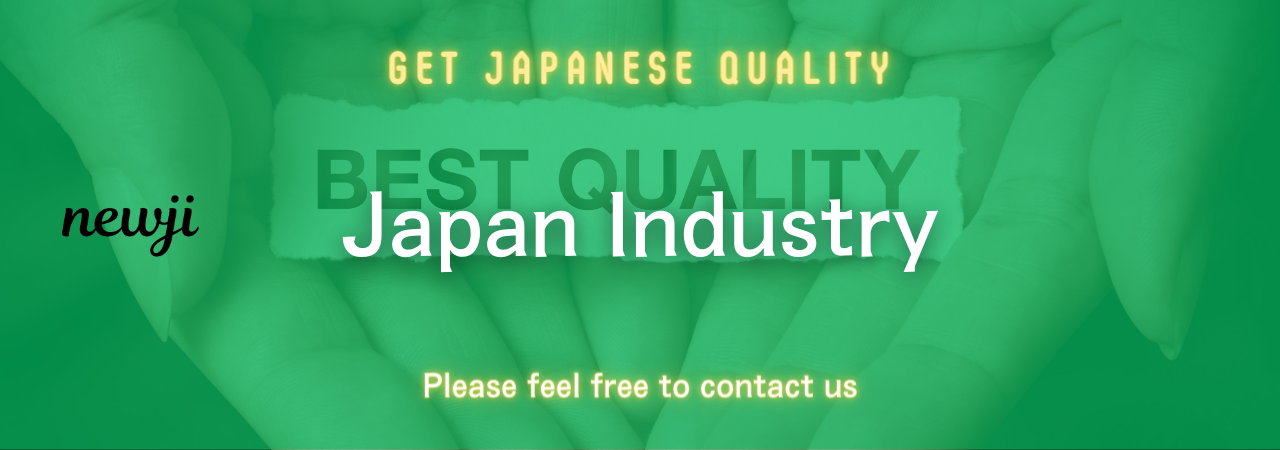
目次
Understanding Dimensional Stability in Apparel Manufacturing
In the apparel manufacturing industry, maintaining the dimensional stability of fabrics is crucial for ensuring high-quality products.
Dimensional stability refers to the fabric’s ability to maintain its original dimensions after being subjected to processes like washing, dyeing, and drying.
One of the key concerns in achieving dimensional stability is addressing fabric shrinkage.
Shrinkage can lead to size inconsistencies, which undermine the product’s quality and customer satisfaction.
Therefore, it is essential for quality assurance managers to understand and implement effective strategies to control shrinkage.
What is Shrinkage Ratio?
The shrinkage ratio is a metric used to quantify the extent of shrinkage a fabric undergoes during processing.
It is calculated by comparing the change in dimensions after washing or other treatments to the original dimensions.
The shrinkage ratio is expressed as a percentage and provides a clear indication of how much a fabric will shrink.
For instance, if a fabric measures 100cm in length initially and reduces to 95cm after washing, the shrinkage ratio would be 5%.
Understanding and managing this ratio is crucial for creating garments that fit well and maintain their shape over time.
Importance of Shrinkage Testing
Shrinkage testing is a vital step in the production process for quality assurance teams.
By conducting shrinkage tests, manufacturers can predict how a fabric will behave during customer use.
This information helps in designing garments that account for potential shrinkage, thus ensuring the final product meets size specifications.
Regular shrinkage testing can also help identify inconsistencies in fabric batches, enabling manufacturers to address issues before production.
In turn, this minimizes waste and maintains high standards of quality.
Conducting a Shrinkage Ratio Test
To perform a shrinkage ratio test, follow these steps:
1. **Sample Selection**: Choose fabric samples from different batches to ensure consistency.
Cut samples with precise dimensions to serve as a baseline for measurement.
2. **Mark and Measure**: Use fabric markers to clearly label the edges of the sample.
Record initial measurements with a ruler or measuring tape.
3. **Treatment Process**: Subject the samples to washing, drying, or any other fabric processing method applicable to the product line.
Use the same conditions that the final product will experience.
4. **Re-Measure**: After the treatment, use the same ruler or measuring tape to measure the samples again.
Note any changes in the fabric dimensions.
5. **Calculate the Shrinkage Ratio**: Use the formula: (Original Dimension – Post-Treatment Dimension) / Original Dimension * 100 to determine the shrinkage percentage.
By systematically conducting these tests, production teams can establish authentic shrinkage metrics, enabling appropriate product adjustments.
Key Factors Affecting Shrinkage
Several factors influence the shrinkage of fabrics:
– **Fabric Type**: Natural fibers like cotton tend to shrink more than synthetic fibers, although treatment processes can alter these characteristics.
– **Weave Construction**: Loose weave constructions allow for more movement between the yarns, potentially increasing shrinkage risks.
– **Finishing Treatments**: Certain chemical finishes and heat treatments can stabilize fabric dimensions or conversely, lead to additional shrinkage.
Countermeasures for Controlling Shrinkage
Managing shrinkage effectively ensures the production of consistent and reliable garments.
Here are a few countermeasures that quality assurance teams in the apparel industry can implement:
Pre-Shrinking Treatments
Pre-shrinking processes can be employed to preemptively reduce shrinkage during the manufacturing stage.
Techniques such as compacting or sanforizing apply mechanical means to compress fabric before transforming it into garments.
These methods stabilize the dimensions and can significantly diminish the extent of shrinkage.
Use of Blended Fabrics
Designing apparel using fabric blends, particularly with synthetic fibers, creates materials that are more resistant to shrinkage.
Blended fabrics offer added resilience and expand the versatility of garment design.
Quality Control at Every Stage
Implementing stringent quality control measures throughout production is critical.
This includes inspecting raw materials, monitoring fabric treatment processes, and conducting regular shrinkage tests.
By maintaining consistent scrutiny, issues leading to significant shrinkage can be identified and corrected promptly.
Conclusion: Ensuring Dimensional Stability
For managers in quality assurance departments of apparel manufacturing, understanding the intricacies of the shrinkage ratio is vital.
Effective management of shrinkage through comprehensive testing and pre-emptive measures ensures that garments remain true to size and retain their shape.
By investing in robust techniques and protocols to control shrinkage, manufacturers can enhance product quality, improve customer satisfaction, and bolster their brand’s reputation.
Addressing shrinkage actively also contributes to sustainable practices by reducing waste and increasing the lifespan of apparel products.
資料ダウンロード
QCD調達購買管理クラウド「newji」は、調達購買部門で必要なQCD管理全てを備えた、現場特化型兼クラウド型の今世紀最高の購買管理システムとなります。
ユーザー登録
調達購買業務の効率化だけでなく、システムを導入することで、コスト削減や製品・資材のステータス可視化のほか、属人化していた購買情報の共有化による内部不正防止や統制にも役立ちます。
NEWJI DX
製造業に特化したデジタルトランスフォーメーション(DX)の実現を目指す請負開発型のコンサルティングサービスです。AI、iPaaS、および先端の技術を駆使して、製造プロセスの効率化、業務効率化、チームワーク強化、コスト削減、品質向上を実現します。このサービスは、製造業の課題を深く理解し、それに対する最適なデジタルソリューションを提供することで、企業が持続的な成長とイノベーションを達成できるようサポートします。
オンライン講座
製造業、主に購買・調達部門にお勤めの方々に向けた情報を配信しております。
新任の方やベテランの方、管理職を対象とした幅広いコンテンツをご用意しております。
お問い合わせ
コストダウンが利益に直結する術だと理解していても、なかなか前に進めることができない状況。そんな時は、newjiのコストダウン自動化機能で大きく利益貢献しよう!
(Β版非公開)