- お役立ち記事
- For new employees in the production technology department of the pharmaceutical manufacturing industry! Basics of aseptic filling and key points for equipment maintenance
For new employees in the production technology department of the pharmaceutical manufacturing industry! Basics of aseptic filling and key points for equipment maintenance
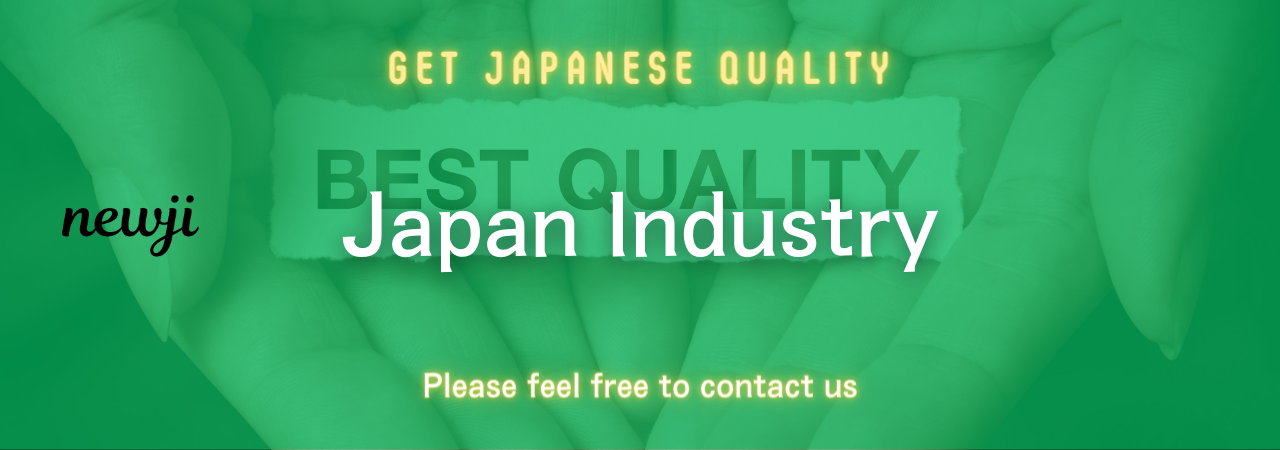
目次
Understanding Aseptic Filling in Pharmaceutical Manufacturing
In the pharmaceutical manufacturing industry, maintaining sterility during production is crucial.
Aseptic filling is the process used to prevent contamination, especially for injectable products.
To ensure the safety and efficacy of these products, it’s essential to understand the basics of aseptic filling.
Aseptic filling involves placing sterilized products into pre-sterilized containers such as vials, syringes, or ampoules.
The goal is to maintain sterility throughout the process to avoid contamination.
Contamination can compromise the integrity of the products, making them unsafe for patient use.
The aseptic filling process takes place in a controlled environment, often within cleanrooms or isolators.
These environments are designed to minimize the risk of contamination from particles such as bacteria, viruses, or fungi.
Operators working in these environments must follow stringent protocols, including wearing protective clothing and undergoing specific sanitation procedures.
The Importance of Aseptic Filling
Aseptic filling is particularly important in the production of sterile pharmaceutical products.
It ensures that drugs administered to patients are free from harmful microorganisms.
This is vital for safety and efficacy, as contaminated products can lead to serious health complications.
The pharmaceutical industry is heavily regulated to ensure that all products meet strict safety standards.
Aseptic filling is a critical part of these regulatory requirements.
Failure to maintain proper aseptic filling processes can result in product recalls, regulatory actions, and harm to patients.
Equipment Used in Aseptic Filling
To achieve aseptic conditions, specialized equipment is used in the process.
Understanding these tools is essential for anyone working in pharmaceutical production technology.
Filling Machines
Filling machines are the backbone of the aseptic filling process.
These machines must be capable of accurately filling each container with the correct dose of the product.
They should be designed to minimize the risk of contamination and be easy to clean and sterilize.
Filling machines often feature automated systems that control the filling process.
Automation reduces human intervention, which in turn lowers the risk of contamination.
This equipment must be calibrated and maintained regularly to ensure precise dosage and sterility.
Laminars and Hoods
Laminar airflow hoods are used to provide a sterile environment for aseptic filling.
These hoods create a continuous stream of high-efficiency particulate air (HEPA) filtered air that removes contaminants.
Operators work within these hoods to minimize the risk of exposing products to airborne particles.
Regular maintenance of laminar flow hoods is crucial to ensure their efficacy.
Filters must be replaced and the system checked for airflow uniformity to prevent contamination.
Cleanrooms
Aseptic filling typically occurs in cleanrooms, which are specially designed to maintain low levels of environmental pollutants.
Cleanrooms have specific airflow patterns, temperatures, and humidity controls to maintain a controlled environment.
Personnel entering cleanrooms must follow strict procedures, including wearing sterile garments and passing through air showers to remove contaminants.
Routine cleaning and testing are required to maintain the integrity of the cleanroom environment.
Key Points for Equipment Maintenance
For new employees in the production technology department, understanding equipment maintenance is vital for successful aseptic filling operations.
Regular Inspection and Calibration
Equipment used in aseptic filling must be regularly inspected to identify any signs of wear or malfunction.
Regular inspections help prevent equipment failures that could compromise product sterility.
Calibration ensures that machines are operating within the required specifications for accuracy and consistency.
Documenting maintenance activities is essential for compliance and provides a record of the equipment’s performance over time.
Preventive Maintenance
Implementing a preventive maintenance program can help reduce unplanned downtime and extend the lifespan of your equipment.
This involves performing maintenance tasks at scheduled intervals, even when equipment appears to be functioning correctly.
Preventive maintenance includes tasks such as replacing filters, lubricating moving parts, and checking electrical connections.
By addressing potential issues before they become problems, companies can reduce the risk of contamination and maintain smooth production operations.
Training and Competency
Employees responsible for equipment maintenance must be adequately trained and competent in their roles.
Training programs should be comprehensive and cover all aspects of aseptic filling and equipment maintenance.
Ongoing training ensures that staff remain up to date with the latest technologies and best practices.
Trained employees are also more likely to identify potential issues early and take corrective actions to prevent them from escalating.
Conclusion
Aseptic filling is a crucial process in the pharmaceutical manufacturing industry, ensuring the production of sterile and safe products.
Understanding the basics of aseptic filling and the key points for equipment maintenance is essential for new employees in the production technology department.
By adhering to stringent procedures and maintaining equipment effectively, companies can ensure product safety and regulatory compliance.
Overall, a thorough understanding of aseptic filling and maintenance practices contributes to the success of pharmaceutical manufacturing operations.
資料ダウンロード
QCD調達購買管理クラウド「newji」は、調達購買部門で必要なQCD管理全てを備えた、現場特化型兼クラウド型の今世紀最高の購買管理システムとなります。
ユーザー登録
調達購買業務の効率化だけでなく、システムを導入することで、コスト削減や製品・資材のステータス可視化のほか、属人化していた購買情報の共有化による内部不正防止や統制にも役立ちます。
NEWJI DX
製造業に特化したデジタルトランスフォーメーション(DX)の実現を目指す請負開発型のコンサルティングサービスです。AI、iPaaS、および先端の技術を駆使して、製造プロセスの効率化、業務効率化、チームワーク強化、コスト削減、品質向上を実現します。このサービスは、製造業の課題を深く理解し、それに対する最適なデジタルソリューションを提供することで、企業が持続的な成長とイノベーションを達成できるようサポートします。
オンライン講座
製造業、主に購買・調達部門にお勤めの方々に向けた情報を配信しております。
新任の方やベテランの方、管理職を対象とした幅広いコンテンツをご用意しております。
お問い合わせ
コストダウンが利益に直結する術だと理解していても、なかなか前に進めることができない状況。そんな時は、newjiのコストダウン自動化機能で大きく利益貢献しよう!
(Β版非公開)