- お役立ち記事
- For processing engineers in the machining industry! Optimization of tool selection and cutting conditions in milling
For processing engineers in the machining industry! Optimization of tool selection and cutting conditions in milling
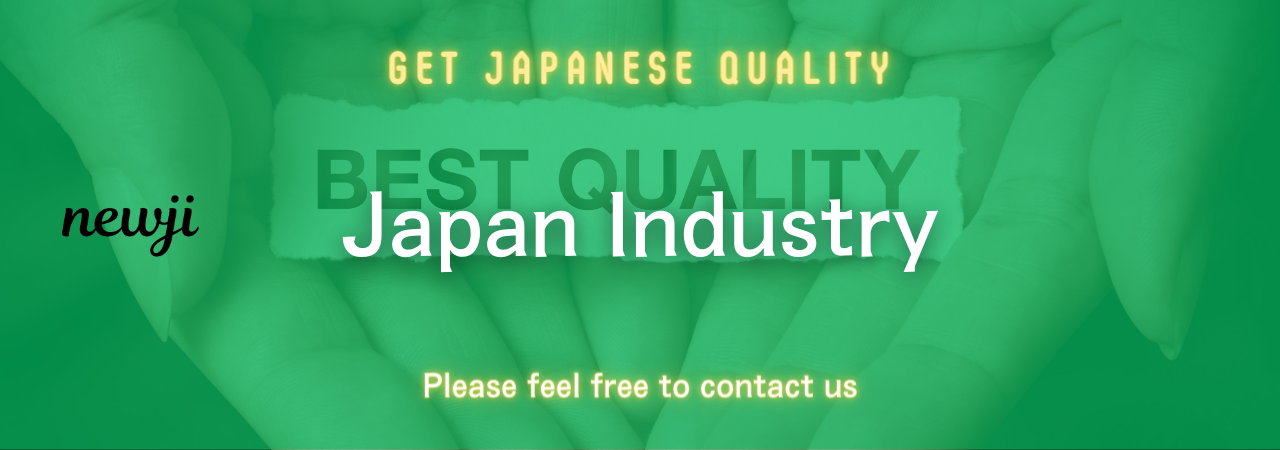
目次
Understanding the Basics of Tool Selection in Milling
Tool selection is a critical aspect of the milling process.
As processing engineers, understanding the different types of tools and their applications can significantly impact both the quality of the part being machined and the efficiency of the entire process.
It is important to choose a tool based on the material and the specific milling process involved.
Different materials such as steel, aluminum, and composite require different types of tools.
For example, carbide tools are highly recommended for steel due to their hardness and wear resistance.
Meanwhile, high-speed steel tools are generally preferred for milling soft materials like aluminum.
When it comes to different milling processes, such as shoulder milling or face milling, certain tools are better suited than others.
End mills, for instance, work best for side milling, while face mills excel at making flat surfaces.
Choosing the correct tool geometry is equally crucial.
Geometry affects the cutting process in terms of chip removal, tool stability, and surface finish.
Key Factors in Tool Selection
There are multiple criteria to consider when selecting a tool for milling:
1. **Material Compatibility**: The tool must be suitable for the material being machined.
2. **Tool Geometry**: Factors like the number of flutes, helix angle, and coating affect the tool’s performance.
3. **Cutting Parameters**: This includes the tool’s ability to handle speed, feed rate, and depth of cut.
4. **Cost and Durability**: These should be balanced to achieve a cost-effective machining process without sacrificing quality.
Optimizing Cutting Conditions
Once the right tool is selected, optimizing the cutting conditions is the next step to ensuring a successful milling operation.
Cutting conditions directly impact the tool’s life, the surface finish of the workpiece, and the overall efficiency of the machining process.
Speed and Feed Rate
Cutting speed and feed rate are two primary parameters in setting cutting conditions.
The cutting speed is the rate at which the cutting tool moves through the material.
High cutting speeds can lead to increased heat generation but can also reduce machining time and improve surface finishes.
It is essential to find a balance to prevent tool wear and maintain part quality.
The feed rate is the distance the tool advances along the workpiece for each revolution.
An optimal feed rate ensures efficient removal of material while maintaining the appropriate load on the tool.
If the feed rate is too high, it can cause tool breakage, while a too-low rate can lead to increased wear and longer machining times.
Depth of Cut
The depth of cut refers to the thickness of the material removed in one pass of the tool.
This should be set to match the tool’s specifications and the material’s properties.
A shallow depth of cut results in a better surface finish but takes longer to complete, whereas a deeper cut can speed up production but runs the risk of decreasing tool life.
Utilizing Advanced Technologies
To further optimize tool selection and cutting conditions, leveraging modern machining technologies is invaluable.
Advanced software and machinery can offer predictive analytics, automation, and precision.
CNC Machining and Software
Computer Numerical Control (CNC) machines have revolutionized how milling is performed.
They allow for precise control over tool movements and cutting parameters.
Integrating these with advanced CAM (Computer-Aided Manufacturing) software can allow engineers to simulate the milling operations before actual machining.
This helps in predicting tool wear, evaluating part geometry, and making necessary adjustments prior to production.
Simulation tools can also analyze different cutting scenarios to suggest the best tool paths and conditions.
This ultimately reduces the setup time and minimizes errors, ensuring a smoother production process.
Sensors and Monitoring Systems
Incorporating sensors and monitoring systems in milling operations can provide real-time data on tool wear, vibration, and temperature.
This data can be used to adjust cutting conditions dynamically, thus preventing potential issues such as tool failure and improving the quality of the final product.
These systems alert operators about critical issues and suggest maintenance or tool changes.
They enhance productivity by reducing machine downtime and ensuring consistent performance.
The Impact of Optimization
Optimization of tool selection and cutting conditions directly influences efficiency, cost, and product quality in the machining industry.
With the right tools and conditions, waste is minimized, cycle times are reduced, and workpieces have improved finishes with tighter tolerances.
Moreover, by optimizing these aspects, companies can increase their competitive advantage in the industry.
Good tool management and condition optimization lead to lesser energy consumption, prolonging tool life, and reducing machine stress.
The result is a comprehensive improvement in operational efficiency and product deliverables.
To stay ahead, processing engineers must continuously educate themselves on the latest trends and technologies in the machining world.
Utilizing industry best practices and innovations will ensure the sustainability and profitability of machining operations.
In conclusion, the road to excelling in the machining industry involves not just understanding the traditional practices but also integrating modern technologies and methodologies.
By optimizing tool selection and cutting conditions, machining processes can achieve remarkable improvements in productivity and quality.
資料ダウンロード
QCD調達購買管理クラウド「newji」は、調達購買部門で必要なQCD管理全てを備えた、現場特化型兼クラウド型の今世紀最高の購買管理システムとなります。
ユーザー登録
調達購買業務の効率化だけでなく、システムを導入することで、コスト削減や製品・資材のステータス可視化のほか、属人化していた購買情報の共有化による内部不正防止や統制にも役立ちます。
NEWJI DX
製造業に特化したデジタルトランスフォーメーション(DX)の実現を目指す請負開発型のコンサルティングサービスです。AI、iPaaS、および先端の技術を駆使して、製造プロセスの効率化、業務効率化、チームワーク強化、コスト削減、品質向上を実現します。このサービスは、製造業の課題を深く理解し、それに対する最適なデジタルソリューションを提供することで、企業が持続的な成長とイノベーションを達成できるようサポートします。
オンライン講座
製造業、主に購買・調達部門にお勤めの方々に向けた情報を配信しております。
新任の方やベテランの方、管理職を対象とした幅広いコンテンツをご用意しております。
お問い合わせ
コストダウンが利益に直結する術だと理解していても、なかなか前に進めることができない状況。そんな時は、newjiのコストダウン自動化機能で大きく利益貢献しよう!
(Β版非公開)