- お役立ち記事
- A must-see for leaders in the production technology department of the electronics manufacturing industry! Reflow Oven Temperature Profile Optimization Guide
A must-see for leaders in the production technology department of the electronics manufacturing industry! Reflow Oven Temperature Profile Optimization Guide
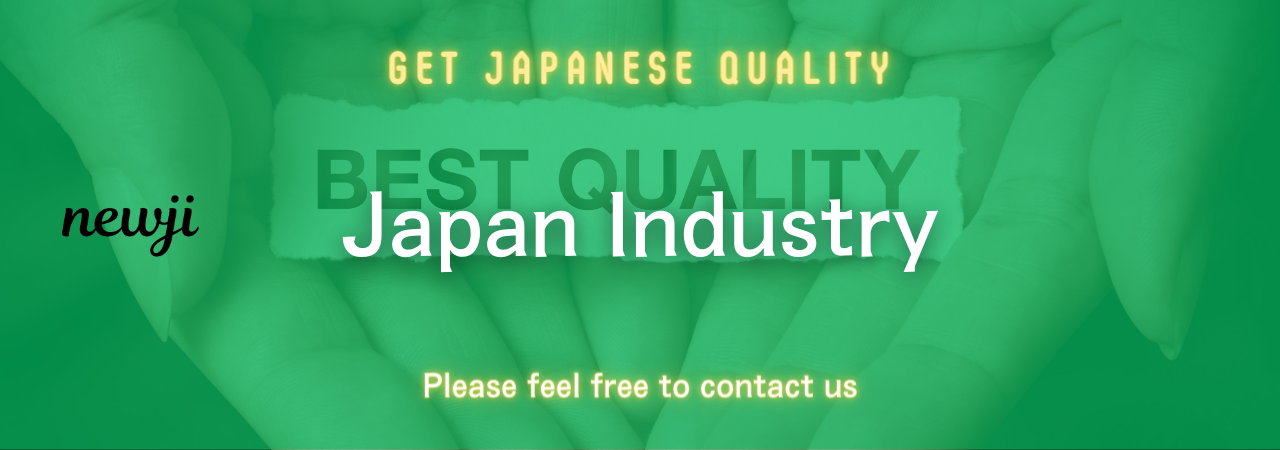
目次
Understanding Reflow Oven Temperature Profiles
Reflow soldering is a critical process in the electronics manufacturing industry.
Ensuring a consistent and accurate temperature profile in your reflow oven can significantly affect the quality and reliability of the final product.
But what exactly is a reflow oven temperature profile?
In simple terms, it’s the time-temperature curve that a printed circuit board (PCB) follows while moving through the oven.
This profile typically consists of four stages: preheat, soak, reflow, and cooling.
Each stage has specific temperature ranges and durations that must be precisely controlled to achieve optimal solder joints.
Why is Temperature Profile Optimization Important?
Optimizing the temperature profile is vital for several reasons.
Firstly, it ensures the solder paste melts correctly, creating reliable joints between components and the PCB.
This is especially important for complex PCBs used in electronic devices.
Secondly, an optimized profile can prevent defects such as solder bridging, voids, or tombstoning, which can compromise the functionality of the circuit.
Lastly, consistent profiles improve manufacturing efficiency and reduce costly rework or scrap.
Key Factors in Temperature Profile Optimization
When it comes to optimizing the reflow oven temperature profile, several factors come into play.
1. Type of Solder Paste
Different solder pastes have varying melting points and flow characteristics.
It’s essential to understand the specific requirements of the solder paste you are using.
Check the manufacturer’s datasheet to determine the recommended temperature ranges and heating rates.
2. PCB Design and Material
The design and material of the PCB can significantly affect heat distribution during reflow soldering.
Thicker boards and metal cores will absorb more heat, potentially leading to cold solder joints if not adequately compensated for in the profile.
3. Component Sensitivity
Some components are sensitive to high temperatures and prolonged exposure.
Understanding the thermal tolerances of your components is crucial to prevent damage and ensure product reliability.
4. Oven Type and Configuration
The type of reflow oven you use, whether it be a convection, vapor phase, or infrared oven, influences how heat is transferred to the PCB.
Additionally, the zone settings, belt speed, and conveyor width need careful calibration to achieve a uniform temperature profile.
Steps to Optimize Your Temperature Profile
1. Profile Assessment
Start by analyzing your current temperature profile.
Use profiling tools like thermocouples and data loggers to measure the actual temperatures and times experienced by a test PCB.
Identify any deviations from the desired profile.
2. Set Initial Parameters
Based on your analysis, establish preliminary settings for each oven zone.
These include the target temperatures and durations for the preheat, soak, reflow, and cooling stages.
Aim to follow the manufacturer’s guidelines for the solder paste and component specifications.
3. Fine-Tune Zone Settings
Make incremental adjustments to the oven zones, monitoring the impact on the temperature profile.
It’s essential to strike a balance between ensuring complete solder paste reflow and protecting heat-sensitive components.
Adjustments may involve changing belt speed, conveyor width, or individual zone temperatures.
4. Validate the Profile
Once you’ve tweaked the oven settings, validate the new profile using a sample PCB with thermocouples attached.
The profile should meet all the necessary criteria for solder joint integrity, such as peak temperature and time above melting point.
5. Document the Process
Maintain detailed records of your optimized temperature profile settings.
These should include all oven parameters, solder paste specifications, and results from the validation process.
This documentation will serve as a valuable reference and a baseline for future optimizations.
Common Challenges in Profile Optimization
Despite best efforts, there are challenges you may face during optimization.
Component Shadowing
Larger or taller components can block heat from reaching smaller parts, leading to uneven soldering.
To mitigate this, consider using a profile with a slower preheat rate to allow heat to penetrate the entire assembly.
Thermal Fatigue
Repeated thermal cycling can cause cracks in solder joints over time.
An optimized profile should minimize thermal stress by controlling the maximum temperature and cooling rate.
Consistent Quality Control
Quality control measures must be in place to monitor every batch processed through the reflow oven.
Regular checks can catch deviations early and prevent widespread defects.
Conclusion
Optimizing the reflow oven temperature profile is essential for producing high-quality PCB assemblies in the electronics manufacturing industry.
By understanding the key factors and following a systematic approach, you can achieve reliable solder joints and improve your overall production efficiency.
Remember, continuous optimization and quality control are crucial in maintaining the integrity of your manufacturing process.
Whether you’re a seasoned professional or new to the production technology department, this guide will help you navigate the complexities of temperature profile optimization.
資料ダウンロード
QCD調達購買管理クラウド「newji」は、調達購買部門で必要なQCD管理全てを備えた、現場特化型兼クラウド型の今世紀最高の購買管理システムとなります。
ユーザー登録
調達購買業務の効率化だけでなく、システムを導入することで、コスト削減や製品・資材のステータス可視化のほか、属人化していた購買情報の共有化による内部不正防止や統制にも役立ちます。
NEWJI DX
製造業に特化したデジタルトランスフォーメーション(DX)の実現を目指す請負開発型のコンサルティングサービスです。AI、iPaaS、および先端の技術を駆使して、製造プロセスの効率化、業務効率化、チームワーク強化、コスト削減、品質向上を実現します。このサービスは、製造業の課題を深く理解し、それに対する最適なデジタルソリューションを提供することで、企業が持続的な成長とイノベーションを達成できるようサポートします。
オンライン講座
製造業、主に購買・調達部門にお勤めの方々に向けた情報を配信しております。
新任の方やベテランの方、管理職を対象とした幅広いコンテンツをご用意しております。
お問い合わせ
コストダウンが利益に直結する術だと理解していても、なかなか前に進めることができない状況。そんな時は、newjiのコストダウン自動化機能で大きく利益貢献しよう!
(Β版非公開)