- お役立ち記事
- For managers of production operations departments! How to maximize work efficiency by thoroughly implementing 5S activities
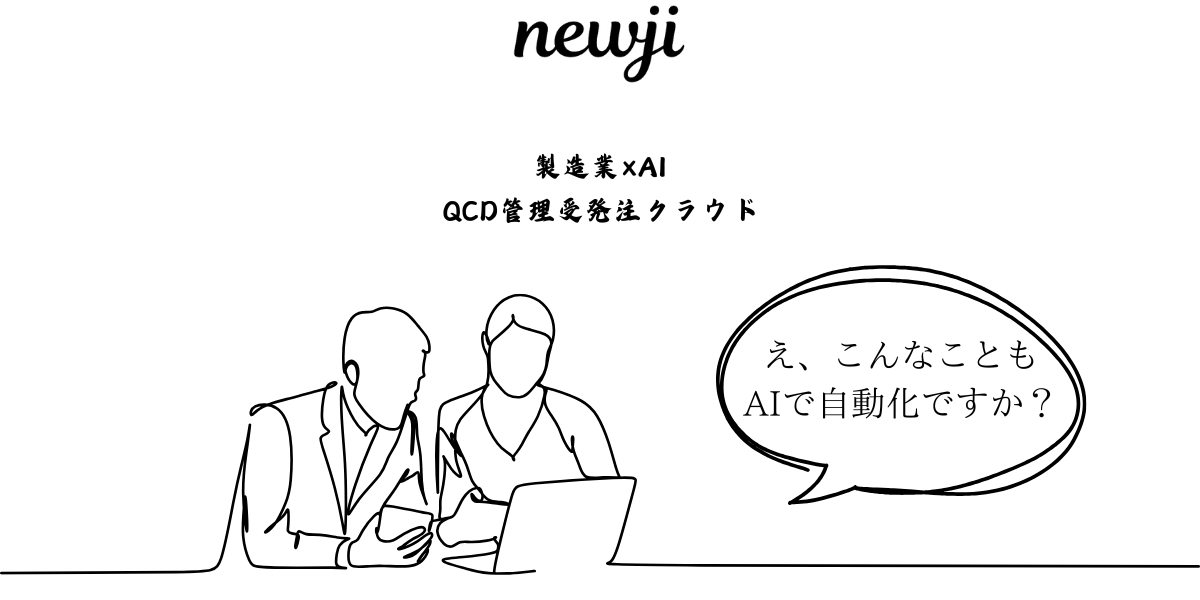
For managers of production operations departments! How to maximize work efficiency by thoroughly implementing 5S activities
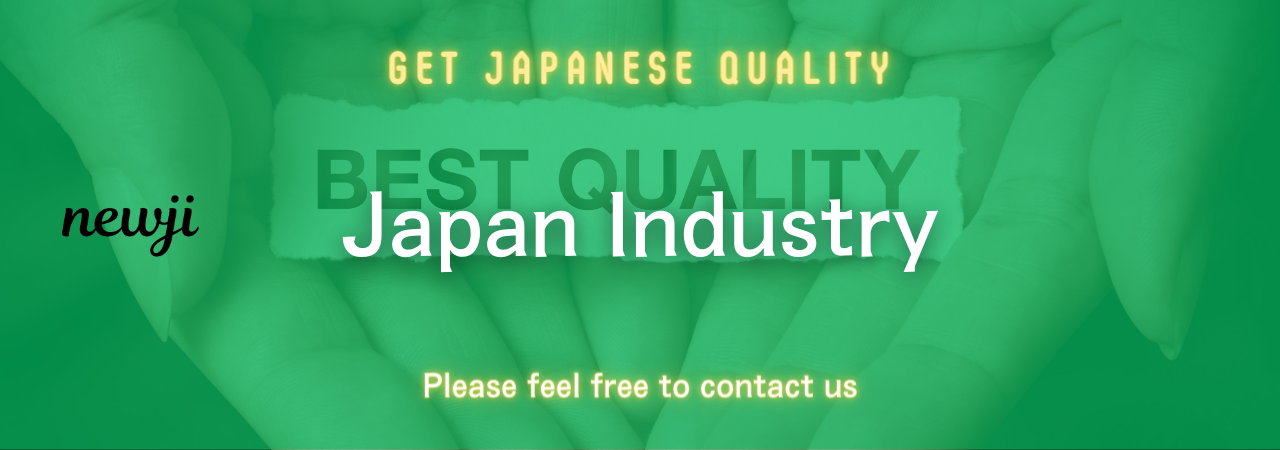
目次
Understanding 5S Activities
5S is a workplace organization method that originated in Japan and has been widely adopted around the world for its effectiveness in improving work efficiency and productivity.
The term “5S” stands for five Japanese words: Seiri, Seiton, Seiso, Seiketsu, and Shitsuke.
In English, these translate to Sort, Set in Order, Shine, Standardize, and Sustain.
Each of these elements plays a crucial role in streamlining processes, minimizing waste, and fostering a safer and more organized work environment.
Sort (Seiri)
The first step in 5S, Sort, involves identifying and eliminating unnecessary items from the workspace.
By removing clutter, employees can focus on essential tools and materials, thus reducing time spent searching for them.
Sorting not only enhances efficiency but also aids in preventing accidents and improving overall quality.
To implement this step effectively, create a checklist of items that are truly needed and regularly assess the workspace to remove unneeded objects.
Set in Order (Seiton)
Once unnecessary items are removed, the next step, Set in Order, involves organizing the remaining items for easy access.
Every item should have a designated place, which minimizes the time spent searching and retrieving tools or materials.
Use labels, color coding, and signage to support this organization.
The goal is to ensure that everything is in place and easy to locate, thereby optimizing workflow and reducing delays in production activities.
Shine (Seiso)
Shine focuses on keeping the work environment clean and maintained at all times.
Regular cleaning routines prevent the buildup of dirt and dust, which can impact equipment performance and safety.
By maintaining a clean workspace, you also promote a sense of pride among employees and foster an atmosphere of discipline and respect.
Incorporate daily or weekly cleaning tasks into the routine, with clear responsibilities assigned to ensure that cleanliness is a shared responsibility among team members.
Standardize (Seiketsu)
Standardize aims to integrate the practice of sorting, setting in order, and shining into the daily workflow.
Developing standardized procedures ensures consistency and helps maintain the improvements achieved through the first three steps of 5S.
Make use of visual aids like charts and diagrams to communicate standardized processes.
Regular training and meetings should reinforce the importance of adhering to these standards to assure collective commitment towards operational excellence.
Sustain (Shitsuke)
The final step, Sustain, is about maintaining and nurturing a culture of continuous improvement.
Encourage teams to stick to the standards set and hold regular audits and reviews to ensure compliance.
Sustainability in 5S activities involves ongoing education and adjustments as necessary to accommodate changes in the production environment.
A continuous feedback loop can help identify bottlenecks and opportunities for further enhancement, thereby ingraining 5S as a core aspect of daily operations.
Benefits of Implementing 5S
Applying the principles of 5S can yield numerous benefits for production operations.
One of the most significant advantages is the increase in efficiency due to reduced time searching for materials and tools.
This efficiency leads to faster production times and potentially increased output.
Moreover, a well-organized workspace reduces the risk of accidents and injuries, promoting a safer work environment.
When tools and materials are stored appropriately, there is less chance of tripping hazards and equipment malfunction.
Improving safety also tends to boost employee morale and satisfaction, leading to better employee retention.
Another key benefit is the enhancement of product quality.
With a cleaner and more organized workspace, there is less likelihood of errors occurring or defects being overlooked, which can improve the overall quality of the products being manufactured.
Additionally, 5S implementation encourages a culture of continuous improvement within the organization.
This mindset not only applies to the physical work environment but extends to processes and workflows, fostering innovation and productivity throughout the company.
Implementing 5S in Your Production Operations
For managers looking to implement 5S activities to maximize operational efficiency, it’s crucial to start with education.
Ensure that all employees understand the principles of 5S and how they contribute to the work environment’s overall efficiency and safety.
Next, involve everyone in the process of implementation.
Encouraging participation promotes ownership and accountability throughout the organization.
Employees who are involved from the beginning are more likely to adhere to the principles and contribute ideas for further improvements.
It’s also important to set measurable objectives and continuously monitor progress.
Use metrics to gauge the effectiveness of 5S activities, such as reduced time spent on tasks, increased safety incident reports, or improved product quality ratings.
Moreover, regular training and workshops help sustain the momentum of 5S activities and keep employees engaged.
These sessions serve as opportunities to refresh knowledge and introduce new techniques or tools that can contribute to efficiency.
Finally, celebrate successes and recognize employees who contribute to maintaining 5S standards.
Acknowledgement reinforces positive behaviors and encourages a culture of continuous improvement.
Conclusion
For managers in the production operations department, implementing 5S activities can be a powerful tool to maximize work efficiency.
By sorting, setting items in order, maintaining cleanliness, standardizing procedures, and sustaining improvements, you can significantly enhance productivity and quality in your operations.
By fostering a culture of continuous improvement, you not only optimize workflows but also promote safety and innovation, leading to the overall success of your organization.
資料ダウンロード
QCD調達購買管理クラウド「newji」は、調達購買部門で必要なQCD管理全てを備えた、現場特化型兼クラウド型の今世紀最高の購買管理システムとなります。
ユーザー登録
調達購買業務の効率化だけでなく、システムを導入することで、コスト削減や製品・資材のステータス可視化のほか、属人化していた購買情報の共有化による内部不正防止や統制にも役立ちます。
NEWJI DX
製造業に特化したデジタルトランスフォーメーション(DX)の実現を目指す請負開発型のコンサルティングサービスです。AI、iPaaS、および先端の技術を駆使して、製造プロセスの効率化、業務効率化、チームワーク強化、コスト削減、品質向上を実現します。このサービスは、製造業の課題を深く理解し、それに対する最適なデジタルソリューションを提供することで、企業が持続的な成長とイノベーションを達成できるようサポートします。
オンライン講座
製造業、主に購買・調達部門にお勤めの方々に向けた情報を配信しております。
新任の方やベテランの方、管理職を対象とした幅広いコンテンツをご用意しております。
お問い合わせ
コストダウンが利益に直結する術だと理解していても、なかなか前に進めることができない状況。そんな時は、newjiのコストダウン自動化機能で大きく利益貢献しよう!
(Β版非公開)