- お役立ち記事
- A must-see for quality managers in the furniture manufacturing industry! How to increase product reliability through durability testing in accordance with JIS standards
A must-see for quality managers in the furniture manufacturing industry! How to increase product reliability through durability testing in accordance with JIS standards
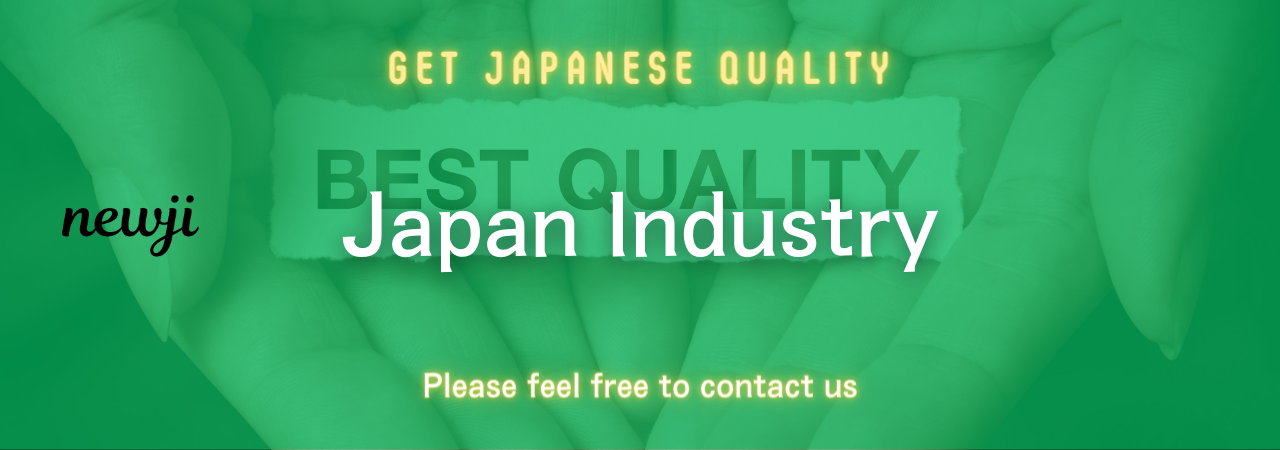
目次
Understanding the Importance of Durability Testing
In the furniture manufacturing industry, quality managers face the challenge of ensuring that products are reliable and long-lasting.
One of the best ways to meet these challenges is through durability testing.
Durability testing involves assessing the furniture’s ability to withstand wear and tear over time.
This is crucial as it directly impacts customer satisfaction and brand reputation.
To maintain high standards, many companies adhere to the Japanese Industrial Standards (JIS), which provide specific guidelines for durability testing.
What Are JIS Standards?
Japanese Industrial Standards, or JIS, are a set of internationally recognized specifications.
They guide the design, manufacturing, and quality assurance processes.
In the context of furniture durability testing, JIS standards help ensure that products meet or exceed customer expectations for reliability and safety.
By adhering to these standards, companies can differentiate themselves in the marketplace, offering products that are not only aesthetically pleasing but also robust and durable.
Benefits of Durability Testing in Furniture Manufacturing
Durability testing offers numerous benefits for quality managers in the furniture manufacturing industry.
First and foremost, it helps identify potential weaknesses in design and materials before the products reach consumers.
This proactive approach can prevent costly recalls and enhance the brand’s reputation for quality.
Moreover, durability testing aids in refining the production process.
By analyzing the data collected from tests, manufacturers can make informed decisions about material selection and production techniques.
This can result in cost savings and improved product performance.
Additionally, complying with JIS standards boosts consumer confidence in the products.
Customers are more likely to trust a brand that demonstrates commitment to upholding internationally recognized quality benchmarks.
This trust is vital for fostering brand loyalty and encouraging repeat business.
How to Conduct Durability Testing According to JIS Standards
Implementing durability testing in line with JIS standards involves a structured approach.
It begins with selecting the appropriate tests for each type of furniture.
Different furniture categories, such as seating, tables, and storage units, have specific JIS guidelines.
Once the tests are determined, setting up the testing environment is next.
This includes simulating real-world conditions as closely as possible.
Tests might involve repeated stress application, temperature variations, and exposure to moisture, depending on the furniture’s intended use.
Throughout the testing process, detailed records should be maintained.
This documentation is crucial for evaluating performance and making data-driven improvements to the product design.
It also serves as evidence for compliance with JIS standards.
Regularly reviewing and updating the testing protocols ensures alignment with changes in industry standards and technological advancements.
This continuous improvement cycle helps maintain a competitive edge and guarantees that the furniture remains reliable and durable.
Challenges in Durability Testing
While durability testing offers substantial benefits, it also presents challenges.
One major challenge is the time and resources required to conduct thorough testing.
It can be resource-intensive and time-consuming, particularly when dealing with a wide range of products.
Another challenge is keeping up with the evolving JIS standards.
As standards are periodically updated, quality managers must stay informed and adjust their testing procedures accordingly.
This requires ongoing training and investment in up-to-date testing equipment.
Moreover, effectively simulating real-world conditions can be complex.
Ensuring that the tests accurately reflect the stresses and strains furniture will face during daily use requires careful planning and skilled execution.
Best Practices for Effective Durability Testing
To overcome these challenges, quality managers can implement several best practices.
Investing in reliable and precise testing equipment is paramount.
High-quality equipment ensures accurate results and can streamline the testing process.
Collaboration with experienced testing labs that specialize in furniture testing can also be beneficial.
These labs have the expertise and technology to conduct complex tests efficiently.
Additionally, fostering a culture of quality within the organization is essential.
Training staff to understand the importance of durability testing and how to conduct it in accordance with JIS standards will enhance the overall quality of the products.
Regularly reviewing and analyzing the test results helps identify patterns and areas for improvement.
Using this data, manufacturers can adapt their designs and manufacturing processes to better meet consumer needs and maintain compliance with JIS standards.
Conclusion: The Path to Reliable Furniture
For quality managers in the furniture manufacturing industry, durability testing is an invaluable tool.
By aligning testing procedures with JIS standards, manufacturers can ensure that their products are reliable, safe, and customer-friendly.
Although challenges exist, adopting best practices and staying informed about updates in standards will pave the way for success.
Investing in durability testing not only enhances product quality but also strengthens the brand’s reputation and fosters consumer trust.
Ultimately, it leads to the production of furniture that stands the test of time, satisfying customers and securing a competitive advantage in the market.
資料ダウンロード
QCD調達購買管理クラウド「newji」は、調達購買部門で必要なQCD管理全てを備えた、現場特化型兼クラウド型の今世紀最高の購買管理システムとなります。
ユーザー登録
調達購買業務の効率化だけでなく、システムを導入することで、コスト削減や製品・資材のステータス可視化のほか、属人化していた購買情報の共有化による内部不正防止や統制にも役立ちます。
NEWJI DX
製造業に特化したデジタルトランスフォーメーション(DX)の実現を目指す請負開発型のコンサルティングサービスです。AI、iPaaS、および先端の技術を駆使して、製造プロセスの効率化、業務効率化、チームワーク強化、コスト削減、品質向上を実現します。このサービスは、製造業の課題を深く理解し、それに対する最適なデジタルソリューションを提供することで、企業が持続的な成長とイノベーションを達成できるようサポートします。
オンライン講座
製造業、主に購買・調達部門にお勤めの方々に向けた情報を配信しております。
新任の方やベテランの方、管理職を対象とした幅広いコンテンツをご用意しております。
お問い合わせ
コストダウンが利益に直結する術だと理解していても、なかなか前に進めることができない状況。そんな時は、newjiのコストダウン自動化機能で大きく利益貢献しよう!
(Β版非公開)