- お役立ち記事
- A must-see for new employees in the blade holder manufacturing industry for automatic cutting machines! Material selection to achieve both safety and precision
A must-see for new employees in the blade holder manufacturing industry for automatic cutting machines! Material selection to achieve both safety and precision
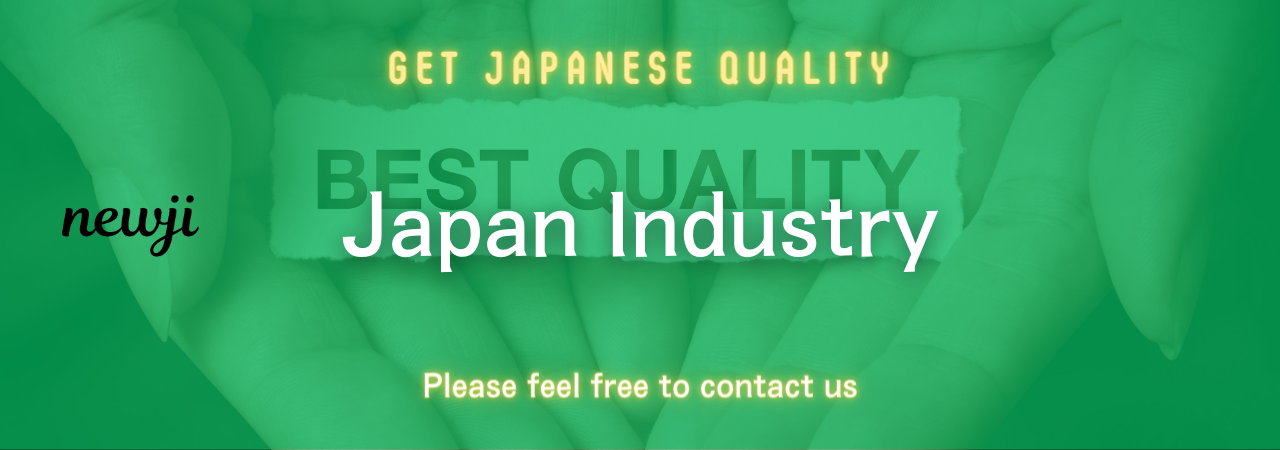
目次
Understanding the Importance of Material Selection
Entering the blade holder manufacturing industry for automatic cutting machines can be an exciting yet challenging journey for new employees.
The backbone of producing reliable and efficient products in this field lies significantly in the choice of materials.
Material selection not only impacts the precision and efficiency of the cutting machines but also plays a pivotal role in ensuring safety during operations.
A meticulous approach to choosing materials can help achieve these dual objectives, ensuring that you contribute to the production of top-notch blade holders.
The Role of Materials in Blade Holder Functionality
Blade holders are crucial components in automatic cutting machines, responsible for maintaining the position and stability of the blade during operation.
The choice of material for these holders directly influences their strength, durability, and resistance to wear and tear.
By selecting the appropriate materials, manufacturers can ensure that the blade holders perform efficiently over extended periods.
Materials that offer high tensile strength and resilience are often preferred, as they are capable of withstanding the intense forces exerted during cutting processes.
A material that stands up to friction and heat generated during cutting operations is invaluable to prolong the life of the blade holder and reduce maintenance costs.
Essential Criteria for Material Selection
New employees must familiarize themselves with the essential criteria when selecting materials for blade holders.
These criteria ensure safety and precision, which are vital to the successful operation of cutting machines.
1. Durability and Longevity
In the blade holder manufacturing industry, durability is paramount.
A material with high durability ensures that the blade holder remains functional over long periods of continuous use.
When a material is robust and long-lasting, it minimizes the likelihood of mechanical failure, thus preventing downtime and additional costs associated with repairs or replacements.
This longevity is crucial not just for operational efficiency but also for maintaining safety standards.
2. Corrosion Resistance
Another vital aspect is the material’s ability to resist corrosion.
Exposure to different environmental factors such as moisture, chemicals, and varying temperatures can lead to corrosion, compromising the blade holder’s structural integrity.
Materials that exhibit strong resistance to corrosion ensure that the blade holder retains its structural and functional properties over time, safeguarding the precision and effectiveness of the cutting machine.
3. Weight Considerations
The weight of the blade holder is an important factor in its functionality.
Lightweight materials are preferable as they enhance the machine’s overall efficiency by reducing the load and allowing for faster movements.
A lighter blade holder also contributes to energy savings, translating to cost-effectiveness for the end-user.
However, it is important to strike a balance between weight and strength to ensure that the blade holder can perform its functions without bending or breaking.
4. Thermal Conductivity
During the cutting process, significant heat can be generated due to friction between the blade and the material being cut.
A material with suitable thermal conductivity can help dissipate heat effectively, minimizing thermal deformation that can adversely affect precision.
By selecting materials that manage heat well, manufacturers ensure that the blade holder maintains its shape and functionality, even under extreme conditions.
Popular Materials Used in Blade Holder Manufacturing
Different materials are chosen in the manufacturing process, each providing unique benefits that contribute to safety and precision.
1. Stainless Steel
Stainless steel is one of the most commonly used materials in blade holder manufacturing, known for its excellent corrosion resistance and high strength.
It offers a unique combination of durability and resistance to environmental damage, making it ideal for long-term applications.
Its aesthetic appeal and ease of maintenance also add to its popularity.
2. Aluminum Alloys
Aluminum alloys are favored for their lightweight nature and good thermal conductivity.
These properties make aluminum an excellent choice for applications where reducing the weight of the blade holder is crucial.
While aluminum alloys may not provide the same level of strength as stainless steel, technological advancements have enabled enhanced alloy compositions that offer improved durability for rigorous cutting tasks.
3. Titanium
Titanium is a premium choice for high-performance blade holders.
It offers exceptional strength-to-weight ratio and excellent corrosion resistance, ideal for demanding environments.
Titanium’s biocompatibility also makes it suitable for specialized applications, such as medical cutting machines.
However, the higher cost of titanium limits its usage to niche markets where performance is prioritized over cost.
Conclusion: Striking the Right Balance
For new employees in the blade holder manufacturing industry, understanding the importance of material selection is a critical stepping stone to contributing positively to the sector.
Achieving a balance between safety and precision requires thoughtful consideration of material properties and performance outcomes.
With advancements in material science continually emerging, staying informed about the latest technology and trends can offer competitive advantages.
By being diligent in material selection, employees ensure that their products not only meet industry standards but also exceed expectations for safety and efficiency.
This commitment to quality and innovation is what drives success in the blade holder manufacturing industry.
資料ダウンロード
QCD調達購買管理クラウド「newji」は、調達購買部門で必要なQCD管理全てを備えた、現場特化型兼クラウド型の今世紀最高の購買管理システムとなります。
ユーザー登録
調達購買業務の効率化だけでなく、システムを導入することで、コスト削減や製品・資材のステータス可視化のほか、属人化していた購買情報の共有化による内部不正防止や統制にも役立ちます。
NEWJI DX
製造業に特化したデジタルトランスフォーメーション(DX)の実現を目指す請負開発型のコンサルティングサービスです。AI、iPaaS、および先端の技術を駆使して、製造プロセスの効率化、業務効率化、チームワーク強化、コスト削減、品質向上を実現します。このサービスは、製造業の課題を深く理解し、それに対する最適なデジタルソリューションを提供することで、企業が持続的な成長とイノベーションを達成できるようサポートします。
オンライン講座
製造業、主に購買・調達部門にお勤めの方々に向けた情報を配信しております。
新任の方やベテランの方、管理職を対象とした幅広いコンテンツをご用意しております。
お問い合わせ
コストダウンが利益に直結する術だと理解していても、なかなか前に進めることができない状況。そんな時は、newjiのコストダウン自動化機能で大きく利益貢献しよう!
(Β版非公開)