- お役立ち記事
- For new employees in the project management department of the chemical manufacturing industry! Fundamentals of handling hazardous materials and legal compliance
For new employees in the project management department of the chemical manufacturing industry! Fundamentals of handling hazardous materials and legal compliance
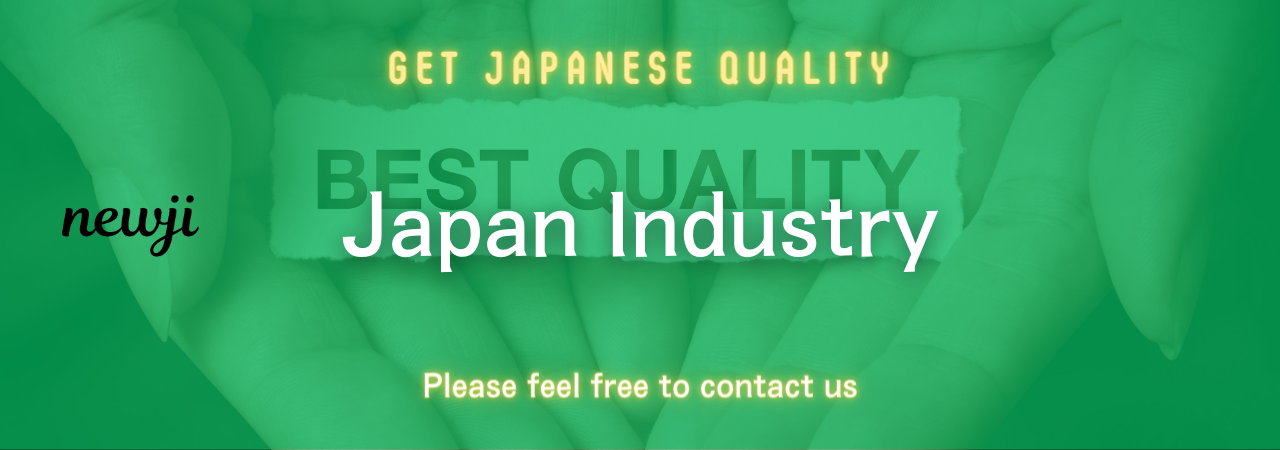
目次
Introduction to Hazardous Materials Handling
Working in the chemical manufacturing industry can be both exciting and challenging, especially if you are new to the project management department.
One of the key responsibilities you will encounter is handling hazardous materials safely and ensuring your team complies with legal regulations.
Understanding how to manage these materials is crucial for workplace safety, environmental protection, and staying within the bounds of the law.
This guide serves as an introductory resource to help you get started with the basics of handling hazardous materials and legal compliance.
Understanding Hazardous Materials
Before diving into handling practices and legal regulations, it’s important to understand what constitutes hazardous materials.
These are substances that pose potential risks to health, safety, or the environment, and they come in various forms such as solids, liquids, or gases.
Examples include toxic chemicals, flammable substances, corrosive agents, and reactive materials.
Recognizing the types and properties of hazardous materials you will work with is the first step in managing them safely.
Common Hazardous Materials in the Industry
In the chemical manufacturing industry, several hazardous materials are commonly encountered:
– **Flammable Liquids:** These include solvents like ethanol and acetone, which can easily ignite in the presence of a heat source.
– **Corrosive Substances:** Such as sulfuric acid and sodium hydroxide, which can cause severe skin burns and eye damage on contact.
– **Toxic Chemicals:** Including substances like benzene and formaldehyde, known for their ability to cause adverse health effects.
– **Reactive Materials:** These are chemicals like sodium or potassium, which can react violently with water or air.
Identifying the materials in your workplace and understanding their risks is crucial for effective hazard management.
Fundamentals of Safe Handling
Once you have identified the hazardous materials, the next step is to implement safe handling practices.
These practices are designed to minimize risks to you, your colleagues, and the environment.
Personal Protective Equipment (PPE)
Wear appropriate Personal Protective Equipment (PPE) at all times while dealing with hazardous materials.
Basic PPE includes gloves, goggles, lab coats, and sometimes respirators, depending on the material you are handling.
Proper use of PPE provides a first line of defense against chemical exposure.
Storage and Labeling
Proper storage and labeling of hazardous materials are critical to prevent accidents.
Ensure that all materials are stored in compatible containers and away from incompatible substances.
Label each container clearly with its contents, hazards, and any handling instructions.
Following the Global Harmonized System (GHS) for labeling can standardize communication of hazard information.
Handling and Transport
When moving hazardous materials, use designated containers and equipment to prevent spills and leaks.
Train your team on proper lifting techniques and secure all materials during transport to avoid damage or exposure.
Limit exposure to open flames or high heat sources, and ensure immediate access to decontamination facilities in case of accidental contact.
Emergency Procedures
Familiarize yourself and your team with the emergency procedures for handling hazardous material incidents.
Conduct regular training sessions and drills to ensure preparedness.
Key procedures should include evacuation routes, emergency contact numbers, the location of safety equipment, and first-aid measures.
Legal Compliance in Hazardous Materials Management
Legal compliance is a cornerstone of working with hazardous materials.
Failing to adhere to regulations can result in severe penalties, reputational damage, and jeopardize employee safety.
Know the Relevant Regulations
Various laws and regulations govern the handling of hazardous materials.
Familiarize yourself with national and local laws such as the Occupational Safety and Health Administration (OSHA) standards and the Environmental Protection Agency (EPA) regulations in the United States.
Internationally, organizations must also comply with the standards set by the International Maritime Dangerous Goods (IMDG) Code and the United Nations Economic Commission for Europe’s regulations.
Understand Your Responsibilities
As a project manager, you have specific responsibilities under regulatory frameworks.
These include ensuring proper training for all employees handling hazardous materials, maintaining accurate records of material usage and incidents, and conducting regular safety audits.
Understanding and fulfilling these obligations are essential to maintaining compliance.
Best Practices for Compliance
Implementing best practices can help sustain compliance.
Conduct regular audits and inspections to identify potential risks and address them promptly.
Engage in continuous education and training for employees to keep up with the latest regulations and safety practices.
Additionally, maintain thorough records of all hazardous materials inventories, incidents, and training activities.
Conclusion
Handling hazardous materials in the chemical manufacturing industry requires a comprehensive understanding of the risks involved and the mitigation actions that must be taken.
By mastering the fundamentals of safe handling and ensuring legal compliance, you contribute to creating a safer work environment for yourself and your colleagues.
Being proactive in implementing good practices and adhering to regulatory standards can prevent accidents, reduce liability, and enhance productivity within your department.
As a new employee in the project management department, embrace these responsibilities with dedication and commitment to achieving excellence in safety and compliance.
資料ダウンロード
QCD調達購買管理クラウド「newji」は、調達購買部門で必要なQCD管理全てを備えた、現場特化型兼クラウド型の今世紀最高の購買管理システムとなります。
ユーザー登録
調達購買業務の効率化だけでなく、システムを導入することで、コスト削減や製品・資材のステータス可視化のほか、属人化していた購買情報の共有化による内部不正防止や統制にも役立ちます。
NEWJI DX
製造業に特化したデジタルトランスフォーメーション(DX)の実現を目指す請負開発型のコンサルティングサービスです。AI、iPaaS、および先端の技術を駆使して、製造プロセスの効率化、業務効率化、チームワーク強化、コスト削減、品質向上を実現します。このサービスは、製造業の課題を深く理解し、それに対する最適なデジタルソリューションを提供することで、企業が持続的な成長とイノベーションを達成できるようサポートします。
オンライン講座
製造業、主に購買・調達部門にお勤めの方々に向けた情報を配信しております。
新任の方やベテランの方、管理職を対象とした幅広いコンテンツをご用意しております。
お問い合わせ
コストダウンが利益に直結する術だと理解していても、なかなか前に進めることができない状況。そんな時は、newjiのコストダウン自動化機能で大きく利益貢献しよう!
(Β版非公開)