- お役立ち記事
- A must-see for managers of quality assurance departments in the food processing industry! How to streamline hygiene management by introducing ATP rapid testing
A must-see for managers of quality assurance departments in the food processing industry! How to streamline hygiene management by introducing ATP rapid testing
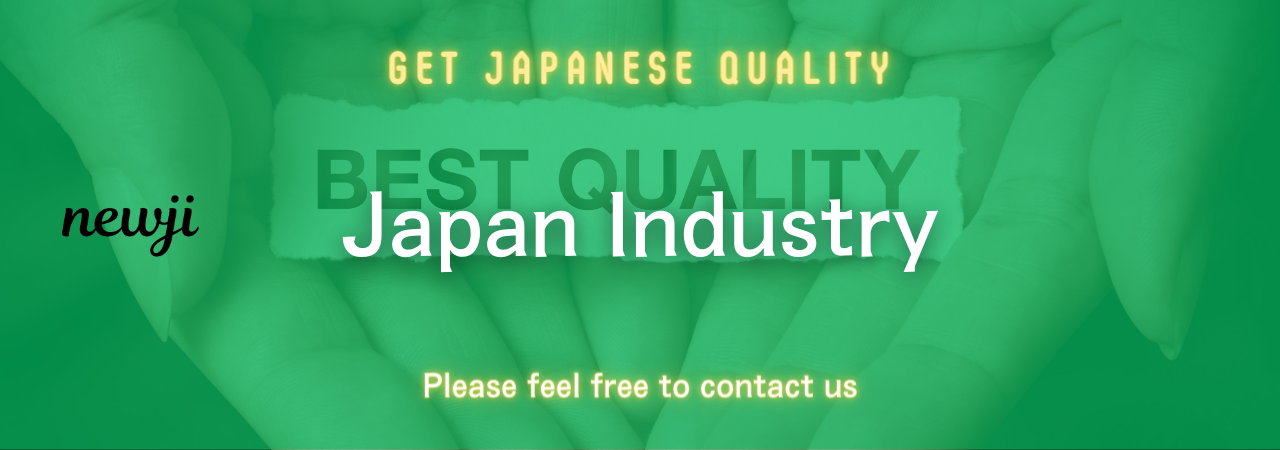
目次
Understanding the Importance of Hygiene Management in Food Processing
In the food processing industry, maintaining high standards of hygiene is crucial.
It directly impacts the safety and quality of food products, which are vital for ensuring public health and safeguarding a company’s reputation.
However, managing hygiene effectively can be a challenging task, particularly for quality assurance departments that oversee multiple aspects of production.
This is where ATP (Adenosine Triphosphate) rapid testing can prove to be a game-changer.
What is ATP Rapid Testing?
ATP rapid testing is a method used to assess the cleanliness of surfaces by detecting the presence of organic matter, such as bacteria, yeast, and mold residues.
Adenosine Triphosphate (ATP) is an energy molecule found in all living cells and its presence on surfaces is a strong indicator of microbial contamination.
The ATP rapid testing process involves swabbing a surface, extracting any ATP present, and then using a bioluminescence reaction to measure the amount of ATP.
This quick test provides immediate feedback on the sanitary condition of processing equipment and environments.
The Benefits of Using ATP Rapid Testing in Food Processing
Enhanced Efficiency in Hygiene Monitoring
Traditional methods of testing for cleanliness, such as microbial culture tests, can take days to produce results.
In contrast, ATP rapid testing delivers immediate results, enabling quality assurance teams to act swiftly if contamination is detected.
This saves time and ensures that corrective action can be taken promptly, minimizing the risk of compromised food safety.
Cost-Effectiveness
ATP rapid testing can be more cost-effective compared to other methods.
The ability to quickly identify and address contamination reduces waste resulting from compromised batches of product.
Additionally, the timely response facilitated by ATP testing can prevent costly production downtime.
Improved Accountability and Training
The immediate feedback provided by ATP rapid testing not only helps identify contamination but also serves as a valuable training tool for staff.
By seeing real-time results, employees can better understand the impact of their cleaning efforts, leading to higher accountability and adherence to hygiene protocols.
Objective Measurement
ATP rapid testing provides objective and quantifiable data on cleanliness levels, which can be integrated into quality assurance documentation.
This clear and consistent data aids in the continuous improvement of hygiene practices over time.
Supporting Compliance with Regulations
Food processing companies must comply with stringent health and safety standards set by regulatory agencies.
Using ATP rapid testing helps maintain these standards by ensuring that hygiene management is consistently effective, thereby easing compliance and audit processes.
Implementing ATP Rapid Testing in Your Organization
Assessing Your Current Hygiene Management System
Before introducing ATP rapid testing, it’s essential to evaluate your existing hygiene management practices.
Identify areas that require improvement and determine where ATP testing will most effectively enhance your processes.
Selecting the Right ATP Testing Equipment
There’s a range of ATP testing devices available on the market, each with different features and capabilities.
When choosing equipment, consider factors such as ease of use, sensitivity, cost, and the specific needs of your production environment.
Consulting with industry experts or suppliers can help you make an informed decision.
Training Your Staff
To maximize the benefits of ATP rapid testing, it’s crucial to train your staff on how to properly use the equipment and interpret results.
Providing education on the significance of ATP testing and hygiene management will foster a culture of cleanliness and responsibility within your organization.
Regularly Monitoring and Adapting Processes
Once ATP rapid testing is implemented, regular monitoring should become a routine part of your hygiene management strategy.
Analyze the data collected over time to identify patterns or recurring issues, and adjust cleaning protocols accordingly.
Continuous monitoring ensures that your processes remain effective and up-to-date with industry standards.
Overcoming Challenges in ATP Rapid Testing Implementation
Initial Costs and Equipment Investment
While the long-term benefits of ATP rapid testing are clear, the initial investment in equipment and training can be a barrier for some companies.
However, considering the potential savings from prevention of contamination and product recalls, the return on investment is well worth the upfront costs.
Resistance to Change
Introducing new methods can often be met with skepticism or resistance from employees accustomed to traditional practices.
Address this challenge by clearly communicating the advantages of ATP testing, and providing comprehensive training to alleviate concerns and promote acceptance.
Ensuring Consistent Practices
To yield reliable results, ATP testing should be conducted consistently and under similar conditions.
Establish clear guidelines for when, where, and how tests should be performed to ensure uniformity across all departments.
Conclusion
For quality assurance departments in the food processing industry, adopting ATP rapid testing for hygiene management offers numerous advantages.
It allows for enhanced efficiency, cost savings, objective measurement of cleanliness, and supports regulatory compliance.
By implementing ATP testing, not only can quality assurance teams streamline their hygiene management processes, but they can also ensure that their products meet the highest standards of safety and quality.
Empowering your team with the right tools and training will safeguard your brand’s reputation and provide a competitive edge in the increasingly demanding market.
資料ダウンロード
QCD調達購買管理クラウド「newji」は、調達購買部門で必要なQCD管理全てを備えた、現場特化型兼クラウド型の今世紀最高の購買管理システムとなります。
ユーザー登録
調達購買業務の効率化だけでなく、システムを導入することで、コスト削減や製品・資材のステータス可視化のほか、属人化していた購買情報の共有化による内部不正防止や統制にも役立ちます。
NEWJI DX
製造業に特化したデジタルトランスフォーメーション(DX)の実現を目指す請負開発型のコンサルティングサービスです。AI、iPaaS、および先端の技術を駆使して、製造プロセスの効率化、業務効率化、チームワーク強化、コスト削減、品質向上を実現します。このサービスは、製造業の課題を深く理解し、それに対する最適なデジタルソリューションを提供することで、企業が持続的な成長とイノベーションを達成できるようサポートします。
オンライン講座
製造業、主に購買・調達部門にお勤めの方々に向けた情報を配信しております。
新任の方やベテランの方、管理職を対象とした幅広いコンテンツをご用意しております。
お問い合わせ
コストダウンが利益に直結する術だと理解していても、なかなか前に進めることができない状況。そんな時は、newjiのコストダウン自動化機能で大きく利益貢献しよう!
(Β版非公開)