- お役立ち記事
- Basics of material mechanics and processing technology that new leaders of mechanical design departments should tackle
Basics of material mechanics and processing technology that new leaders of mechanical design departments should tackle
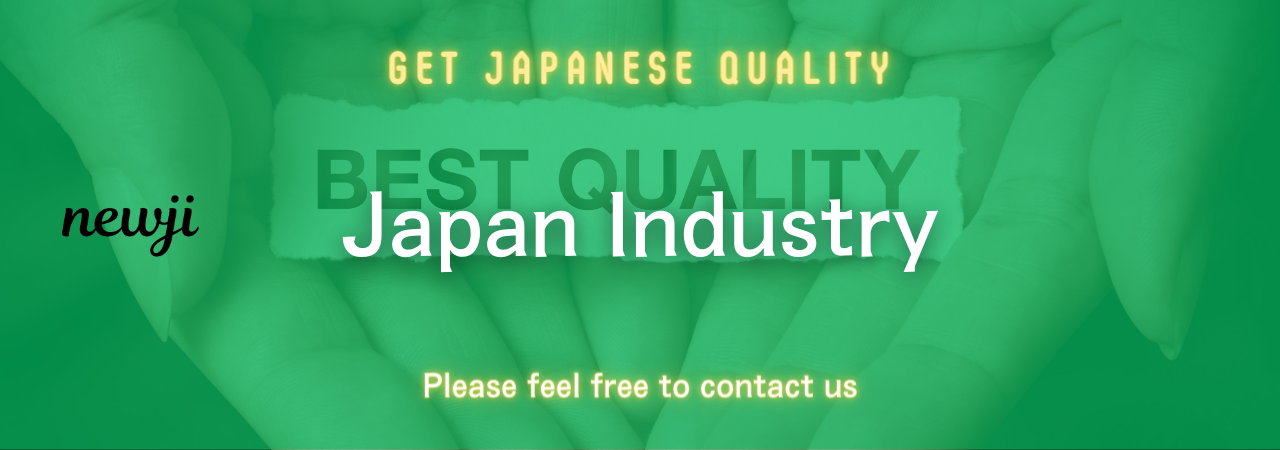
目次
Introduction to Material Mechanics
Understanding material mechanics is fundamental for leaders in mechanical design departments.
Material mechanics, often referred to as the mechanics of materials or strength of materials, is the study of how different materials behave under various forces and conditions.
It involves analyzing the properties of materials to determine how they will react to applied stresses, whether they will bend, stretch, or break.
For new leaders in mechanical design, having a firm grasp of these principles is crucial for creating reliable and efficient designs.
Key Concepts in Material Mechanics
The basic concepts of material mechanics include stress, strain, elasticity, plasticity, and toughness.
Stress is the force applied to a material divided by the area over which it is applied.
Strain is the deformation or displacement of material relative to its original length when stress is applied.
Elasticity refers to a material’s ability to return to its original shape after the stress is removed.
Plasticity is the ability of a material to permanently deform without breaking when a force is applied.
Toughness measures a material’s ability to absorb energy and deform plastically before fracturing.
Importance of Understanding Material Properties
For mechanical design leaders, understanding material properties is critical in choosing the right materials for specific applications.
Different materials have different strengths and weaknesses.
Metals, for instance, tend to be strong and malleable, while ceramics are brittle but very heat-resistant.
Polymers are often lightweight and corrosion-resistant but may not withstand high temperatures as well as metals.
Comprehending these properties ensures that the designs will function effectively and safely under the expected working conditions.
This foundational knowledge guides the decision-making process, from selecting materials to determining the manufacturing methods that should be employed.
Basics of Processing Technology
Processing technology refers to the operations involved in transforming raw materials into finished products.
For mechanical design leaders, a deep understanding of processing technology is essential to produce designs that are not only innovative but also manufacturable and cost-effective.
Common Processing Techniques
There are several major techniques used in material processing, including casting, machining, forming, and joining.
Casting involves pouring liquid material into a mold where it solidifies into a specific shape.
Machining is the process of removing material from a workpiece to achieve desired shapes and features.
This technique includes operations such as drilling, milling, and turning.
Forming processes change the shape of materials without removing any material.
This includes techniques like forging, extrusion, and rolling.
Joining involves the assembly of multiple pieces, often through welding, soldering, or adhesive bonding.
Each of these processes has its own set of advantages and suitability for different materials and applications.
Emerging Technologies in Material Processing
The field of material processing is constantly evolving with new advancements and technologies.
Additive manufacturing, commonly known as 3D printing, is a revolutionary development allowing for the creation of complex shapes and structures layer by layer.
This technique reduces waste and can produce custom components rapidly.
Nanotechnology is another frontier, enabling the manipulation of materials at the molecular level to achieve desirable properties.
This can lead to stronger, lighter, or more heat-resistant materials, opening up new possibilities for mechanical design.
Advanced materials, like composites, combine two or more materials to create an end product with superior qualities.
Leaders in design must stay abreast of these technologies to ensure their products remain competitive.
Implementing Knowledge into Design
Applying the principles of material mechanics and processing technology effectively is where the role of a mechanical design leader truly comes into focus.
A comprehensive approach involves analyzing the requirements, selecting appropriate materials, and choosing the right manufacturing techniques.
Design Process and Material Selection
The design process begins with clearly defining the problem and requirements.
This involves considering the environment in which the final product will operate, such as temperature, pressure, and potential exposure to corrosive substances.
With the requirements outlined, the next step is selecting materials.
This involves considering not only the mechanical properties but also factors like availability, cost, and environmental impact.
Choosing the right material is critical for ensuring performance, durability, and sustainability.
Prototyping and Testing
Prototyping is an integral part of the design process.
It allows the design to be tested and validated before full-scale production begins.
Through prototyping, designers can identify potential issues and make necessary modifications.
It is also a chance to experiment with different processing technologies to find the most efficient and effective method for production.
Testing must be rigorous to ensure the product meets all performance and safety standards.
This includes subjecting prototypes to stress tests, thermal cycles, and fatigue tests to simulate real-world conditions.
Leadership and Continuous Learning
As a leader in the mechanical design department, it is crucial to foster a culture of continuous learning and innovation.
Material mechanics and processing technologies are dynamic fields that require constant updating of knowledge and skills.
Encouraging Team Development
Encourage team members to attend workshops, seminars, and industry conferences to stay updated with the latest advancements and trends.
Facilitate training sessions and share resources about new materials and technologies.
Creating an environment where team members feel inspired to innovate will lead to greater discoveries and improved designs.
Collaborating with Industry Experts
Collaborate with material scientists, engineers, and manufacturers to gain insights and feedback.
These collaborations can provide practical knowledge that goes beyond textbooks and enhance the design’s manufacturability and performance.
In conclusion, mastering the basics of material mechanics and processing technologies is fundamental for any leader in a mechanical design department.
Through a careful blend of material understanding, processing expertise, and leadership, innovative and efficient designs can be achieved, ensuring success in an evolving industry landscape.
資料ダウンロード
QCD調達購買管理クラウド「newji」は、調達購買部門で必要なQCD管理全てを備えた、現場特化型兼クラウド型の今世紀最高の購買管理システムとなります。
ユーザー登録
調達購買業務の効率化だけでなく、システムを導入することで、コスト削減や製品・資材のステータス可視化のほか、属人化していた購買情報の共有化による内部不正防止や統制にも役立ちます。
NEWJI DX
製造業に特化したデジタルトランスフォーメーション(DX)の実現を目指す請負開発型のコンサルティングサービスです。AI、iPaaS、および先端の技術を駆使して、製造プロセスの効率化、業務効率化、チームワーク強化、コスト削減、品質向上を実現します。このサービスは、製造業の課題を深く理解し、それに対する最適なデジタルソリューションを提供することで、企業が持続的な成長とイノベーションを達成できるようサポートします。
オンライン講座
製造業、主に購買・調達部門にお勤めの方々に向けた情報を配信しております。
新任の方やベテランの方、管理職を対象とした幅広いコンテンツをご用意しております。
お問い合わせ
コストダウンが利益に直結する術だと理解していても、なかなか前に進めることができない状況。そんな時は、newjiのコストダウン自動化機能で大きく利益貢献しよう!
(Β版非公開)