- お役立ち記事
- Basics of crash simulation using CAE that new employees in the R&D department of the auto parts manufacturing industry should know
Basics of crash simulation using CAE that new employees in the R&D department of the auto parts manufacturing industry should know
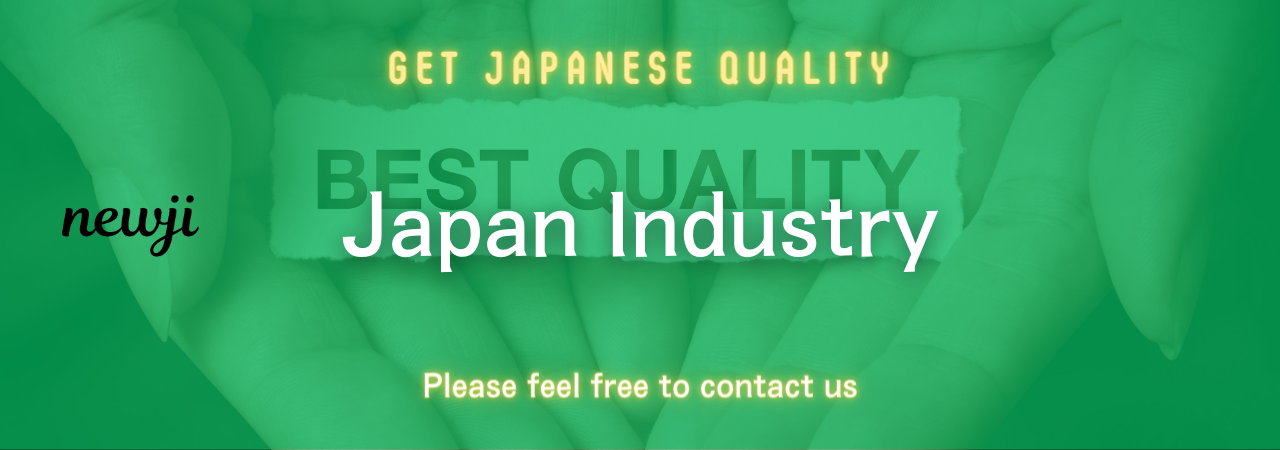
目次
Introduction to Crash Simulation
Crash simulation is a vital component in the automotive industry, particularly in the research and development (R&D) sector of auto parts manufacturing.
It involves using Computer-Aided Engineering (CAE) tools to predict how automotive components will behave in the event of a collision.
Understanding the basics of crash simulation is essential for new employees entering this field, as it ensures safety and efficiency in automobile design.
Why Crash Simulation Matters
In the competitive world of auto parts manufacturing, safety is paramount.
Crash simulation offers a virtual platform to test the potential outcomes of accidents.
This helps in minimizing risks, reducing costs, and ensuring compliance with safety standards.
By simulating crashes, manufacturers can enhance the quality of their products and provide safer vehicles for consumers.
This technology not only saves lives but also improves the brand’s reputation by preventing costly recalls and legal issues.
The Role of CAE in Crash Simulation
CAE is the cornerstone of modern crash simulation.
It allows engineers to create models of vehicle components and simulate their behavior under different crash scenarios.
By using CAE tools, engineers can analyze the stress, strain, and deformation of parts, helping to identify weak points and optimize designs.
CAE software includes different modules that cater to various aspects of crash simulation, such as impact dynamics and material properties.
This comprehensive approach helps achieve accurate and reliable results.
Key Components of Crash Simulation
Crash simulation involves several critical components that new employees should become familiar with.
Modeling
The foundation of crash simulation is modeling the vehicle and its parts.
This involves creating a detailed digital representation that includes geometry, material properties, and connections.
The accuracy of the model directly influences the reliability of the simulation results.
Meshing
Meshing is the process of dividing the model into smaller elements that can be analyzed individually.
The mesh must be fine enough to capture significant deformations but not so fine that it makes the computation unnecessarily complex.
Boundary Conditions
Setting up boundary conditions is crucial in defining how the crash scenario will unfold.
These conditions include initial speeds, impact angles, and environmental factors such as gravity.
Material Properties
Understanding and inputting the correct material properties is essential for realistic simulation outcomes.
Different materials behave differently under stress, and accurate data ensures that the simulation mimics real-world behavior.
Solver
A solver is a crucial part of the CAE software that computes the results of the simulation based on the predefined conditions and inputs.
Selecting the right solver is important to ensure efficiency and precision.
Steps Involved in Crash Simulation
For those new to the field, it’s important to understand the process of crash simulation.
1. Define Objectives
Before starting a simulation, it is essential to define what you aim to achieve.
This might include improving the structural integrity of a part, reducing weight, or meeting specific safety standards.
2. Model Creation
Create a detailed CAD model of the part or assembly to be analyzed.
This model includes all geometric and material details necessary for the simulation.
3. Set Up the Simulation
Input all the relevant data into the CAE software, including material properties, boundary conditions, and meshing.
Ensure all settings align with your simulation objectives.
4. Running the Simulation
Once everything is in place, the simulation can be executed.
Depending on the complexity, this step can take time as the software computes the results based on the provided inputs.
5. Analyze Results
After the simulation, analyze the results to understand how the part behaves under stress.
Look for any weak points or areas for improvement.
6. Iterate and Optimize
Use the insights gained to modify the design and run further simulations if necessary.
This iterative process helps refine and optimize the design for better performance and safety.
Challenges in Crash Simulation
While crash simulation offers numerous benefits, it also comes with its challenges.
Accuracy
Achieving accurate results requires precise data and sophisticated modeling techniques.
Errors in material properties or boundary conditions can lead to unreliable outcomes.
Complexity
Crash simulations can become highly complex, especially when dealing with full-vehicle models.
Managing this complexity requires a thorough understanding of CAE tools and physics.
Computation Time
Depending on the complexity of the simulation, it may require significant computational resources and time.
Efficient use of resources and advanced solvers can help manage this.
The Future of Crash Simulation
Crash simulation continues to evolve with advancements in technology.
Better algorithms, increased computational power, and more detailed modeling capabilities are making simulations faster and more accurate.
Moreover, the integration of artificial intelligence is paving the way for more automated and intelligent simulations.
This progress helps the automotive industry design safer, more efficient vehicles while reducing development time and costs.
Conclusion
Understanding the basics of crash simulation using CAE is essential for new employees in the R&D departments of auto parts manufacturing.
By mastering the essential processes and overcoming challenges, engineers can significantly contribute to creating safer and more reliable vehicles.
As technology evolves, crash simulation will only become a more critical tool in the automotive industry, leading to advancements in safety and innovation.
資料ダウンロード
QCD調達購買管理クラウド「newji」は、調達購買部門で必要なQCD管理全てを備えた、現場特化型兼クラウド型の今世紀最高の購買管理システムとなります。
ユーザー登録
調達購買業務の効率化だけでなく、システムを導入することで、コスト削減や製品・資材のステータス可視化のほか、属人化していた購買情報の共有化による内部不正防止や統制にも役立ちます。
NEWJI DX
製造業に特化したデジタルトランスフォーメーション(DX)の実現を目指す請負開発型のコンサルティングサービスです。AI、iPaaS、および先端の技術を駆使して、製造プロセスの効率化、業務効率化、チームワーク強化、コスト削減、品質向上を実現します。このサービスは、製造業の課題を深く理解し、それに対する最適なデジタルソリューションを提供することで、企業が持続的な成長とイノベーションを達成できるようサポートします。
オンライン講座
製造業、主に購買・調達部門にお勤めの方々に向けた情報を配信しております。
新任の方やベテランの方、管理職を対象とした幅広いコンテンツをご用意しております。
お問い合わせ
コストダウンが利益に直結する術だと理解していても、なかなか前に進めることができない状況。そんな時は、newjiのコストダウン自動化機能で大きく利益貢献しよう!
(Β版非公開)