- お役立ち記事
- For equipment engineers in the automotive industry! Guidelines for maximizing equipment life through TPM activities
For equipment engineers in the automotive industry! Guidelines for maximizing equipment life through TPM activities
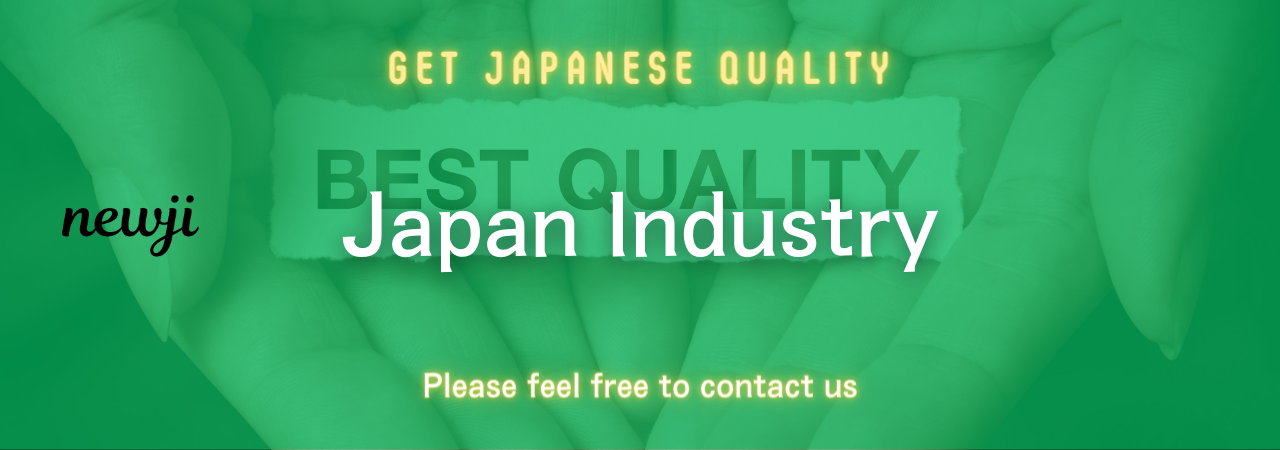
目次
Understanding TPM and Its Importance
Total Productive Maintenance, or TPM, is an innovative approach to equipment maintenance that aims to maximize equipment efficiency and lifespan.
Originally developed in Japan, TPM focuses on proactive and preventive maintenance to improve the reliability and durability of equipment within manufacturing processes.
In the automotive industry, where equipment is constantly subjected to wear and tear, implementing TPM activities is crucial for sustained productivity and cost efficiency.
Industries often face challenges related to frequent equipment breakdowns, unexpected downtime, and costly repairs.
TPM addresses these challenges by emphasizing the importance of maintaining equipment in top-notch condition.
This practice revolves around involving all employees, from top management to frontline workers, in maintaining and improving equipment effectiveness.
By facilitating collaborative efforts, TPM elevates operational performance and fortifies the foundation for a seamless manufacturing process.
Core Principles of TPM
TPM is built around eight foundational pillars, each serving an essential purpose in achieving optimal equipment performance.
1. Autonomous Maintenance
This principle empowers operators to carry out routine maintenance activities themselves.
By taking charge of equipment upkeep, operators can promptly spot any irregularities, ensure cleanliness, and address minor issues before they escalate into major problems.
This proactive approach reduces downtime and fosters a sense of ownership among employees.
2. Planned Maintenance
Transitioning from reactive to proactive maintenance is key to minimizing unexpected equipment failures.
Planned maintenance focuses on scheduling regular check-ups, parts replacement, and inspections to ensure that equipment operates efficiently without unforeseen interruptions.
This systematic approach helps in extending equipment life and reducing repair costs.
3. Quality Maintenance
Enhancing the quality of output while maintaining equipment integrity is the cornerstone of quality maintenance.
By prioritizing defect-free production and continuously monitoring equipment performance, automotive engineers can identify potential issues that might affect product quality.
Addressing these concerns preemptively ensures consistent product reliability.
4. Focused Improvement
The principle of focused improvement targets small, incremental changes that collectively contribute to significant enhancements in equipment productivity.
By gathering data, analyzing performance metrics, and collaborating with cross-functional teams, equipment engineers can pinpoint areas for improvement.
This iterative process leads to continuous optimization of equipment and processes.
5. Early Equipment Management
Integrating TPM into the equipment design and acquisition phase is essential for long-term success.
During this stage, involving equipment engineers in decision-making allows them to provide insights into design modifications, material selection, and best practices.
This proactive involvement ensures that new equipment aligns with TPM goals from the outset.
6. Training and Education
A well-trained workforce is crucial for the successful implementation of TPM activities.
Providing ongoing training and education equips employees with the skills needed to handle maintenance tasks effectively.
This not only boosts employee confidence but also fosters a culture of continuous learning and improvement.
7. Safety, Health, and Environment
Ensuring a safe and healthy working environment is paramount in any manufacturing setting.
TPM emphasizes safety management by identifying potential hazards, conducting risk assessments, and implementing preventive measures.
By safeguarding employees and equipment, automotive industries create a sustainable and productive workplace.
8. Administrative and Support Functions
The seamless integration of administrative and support functions is essential for achieving TPM objectives.
Departments such as purchasing, logistics, and human resources play a vital role in providing the necessary support for maintenance activities.
Collaboration among these departments ensures that resources are efficiently allocated and that equipment engineers have the tools they need.
Benefits of Implementing TPM in the Automotive Industry
Adopting a TPM strategy in the automotive industry yields numerous benefits that contribute to enhanced equipment longevity and operational efficiency.
Increased Equipment Reliability
By proactively addressing maintenance needs, TPM reduces the likelihood of unexpected equipment breakdowns.
This translates to improved reliability, minimizing disruptions to production schedules and ensuring consistent output quality.
Improved Product Quality
With a strong emphasis on quality maintenance, TPM ensures that equipment functions optimally, leading to high-quality products.
Seamless equipment operation reduces the chances of defects and rejects, resulting in increased customer satisfaction.
Cost Optimization
TPM’s focus on planned maintenance and early issue detection leads to a reduction in overall maintenance costs.
Preventing major breakdowns and extending the life of equipment allows automotive manufacturers to allocate resources more efficiently and improve their bottom line.
Enhanced Employee Engagement
By involving employees at all levels, TPM fosters a culture of collaboration and ownership.
Operators, engineers, and managers work together to achieve common goals, leading to higher job satisfaction and employee morale.
Increased Equipment Lifespan
Regular maintenance and early detection of potential issues prolong the life of equipment.
This translates to fewer capital expenditures on new machinery, as existing equipment continues to operate effectively over time.
Steps to Initiate TPM Activities in Your Organization
Implementing TPM requires a well-structured approach.
Follow these steps to initiate TPM activities within your automotive organization:
1. Assessment and Goal Setting
Begin by assessing the current state of your equipment and identifying areas that require improvement.
Set clear, measurable goals that align with corporate objectives and drive the implementation process forward.
2. Leadership Commitment
Secure commitment from top leadership to ensure the successful adoption of TPM activities.
Leadership support is crucial for resource allocation, employee engagement, and overall program success.
3. Employee Involvement and Training
Foster a culture of collaboration by involving employees at all levels in TPM initiatives.
Provide comprehensive training to equip them with the necessary skills and knowledge to execute maintenance tasks effectively.
4. Develop a TPM Plan
Create a detailed plan outlining the steps, resources, and timelines required to implement TPM successfully.
This plan should include guidelines for each TPM pillar, with specific targets and metrics to track progress.
5. Execute and Monitor
Implement the TPM plan and monitor progress regularly.
Gather data, analyze performance, and make necessary adjustments to continuously improve the effectiveness of maintenance activities.
6. Celebrate Successes
Recognize and celebrate achievements to motivate employees and reinforce the value of TPM efforts.
Acknowledging successes boosts morale and encourages continued commitment to TPM practices.
Conclusion
Total Productive Maintenance is a powerful strategy for maximizing equipment life and enhancing operational efficiency in the automotive industry.
By focusing on proactive maintenance, employee engagement, and continuous improvement, TPM empowers organizations to overcome maintenance challenges and thrive in a competitive market.
Implementing TPM requires commitment, collaboration, and a collective effort towards a common goal: achieving optimal equipment performance and ultimately driving business success.
資料ダウンロード
QCD調達購買管理クラウド「newji」は、調達購買部門で必要なQCD管理全てを備えた、現場特化型兼クラウド型の今世紀最高の購買管理システムとなります。
ユーザー登録
調達購買業務の効率化だけでなく、システムを導入することで、コスト削減や製品・資材のステータス可視化のほか、属人化していた購買情報の共有化による内部不正防止や統制にも役立ちます。
NEWJI DX
製造業に特化したデジタルトランスフォーメーション(DX)の実現を目指す請負開発型のコンサルティングサービスです。AI、iPaaS、および先端の技術を駆使して、製造プロセスの効率化、業務効率化、チームワーク強化、コスト削減、品質向上を実現します。このサービスは、製造業の課題を深く理解し、それに対する最適なデジタルソリューションを提供することで、企業が持続的な成長とイノベーションを達成できるようサポートします。
オンライン講座
製造業、主に購買・調達部門にお勤めの方々に向けた情報を配信しております。
新任の方やベテランの方、管理職を対象とした幅広いコンテンツをご用意しております。
お問い合わせ
コストダウンが利益に直結する術だと理解していても、なかなか前に進めることができない状況。そんな時は、newjiのコストダウン自動化機能で大きく利益貢献しよう!
(Β版非公開)