- お役立ち記事
- A must-see for production engineers who manufacture guide rollers for wood processing machines! Designed for smooth operation and wear resistance
A must-see for production engineers who manufacture guide rollers for wood processing machines! Designed for smooth operation and wear resistance
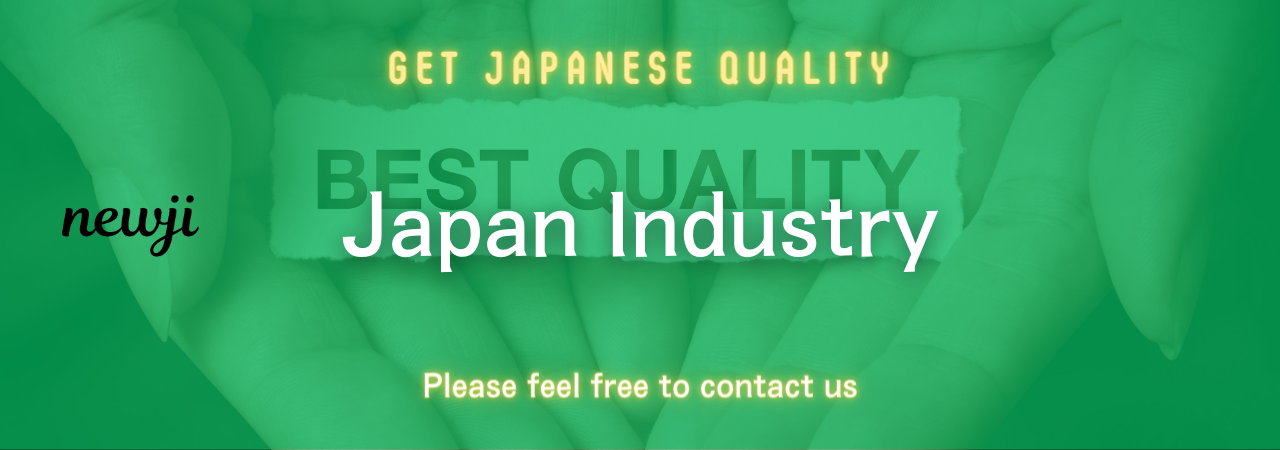
目次
Understanding Guide Rollers for Wood Processing Machines
Guide rollers play a crucial role in the manufacturing and operation of wood processing machines.
These components ensure smooth and efficient handling of wood material as it moves through various stages of processing.
For production engineers, designing guide rollers that provide smooth operation and excellent wear resistance is essential.
Before diving into the specifics of design, let’s understand what guide rollers are and why they are vital in wood processing machinery.
In essence, guide rollers help direct and stabilize the movement of wood, ensuring precision and safety during cutting, planing, or sanding.
Importance of Smooth Operation
Smooth operation in wood processing machines is imperative for several reasons.
First, it contributes to the overall efficiency of the machine, minimizing downtime and maximizing throughput.
A smooth guide roller ensures that wood pieces travel seamlessly through the machinery without unnecessary interruptions or jamming.
Moreover, precision in wood processing is central to achieving high-quality output.
If the rollers aren’t functioning smoothly, they can cause deviations in the cut or finish quality, leading to waste and increased operational costs.
Guide rollers designed for smooth performance can significantly reduce these issues.
Enhancing Wear Resistance
Wear resistance is another critical factor that production engineers need to consider when manufacturing guide rollers for wood processing machines.
Rollers are subject to constant contact and friction with wood, which can lead to wear over time.
If a guide roller wears down quickly, it not only affects the machine’s efficiency but also incurs additional costs for replacements and maintenance.
Incorporating durable materials and advanced engineering techniques in the manufacturing process can enhance wear resistance.
Production engineers should focus on materials that withstand friction and environmental factors like moisture, which can contribute to wear and degradation.
Material Selection for Guide Rollers
Choosing the right material is paramount to achieving the desired smooth operation and wear resistance.
Materials such as polyurethane or steel are commonly used for guide rollers due to their durability and capacity to handle various stresses.
Polyurethane is favored for its excellent abrasion resistance and flexibility.
It’s known for handling high-impact applications and can absorb shock better, making it suitable for guide rollers in wood processing machines.
Steel, on the other hand, is renowned for its strength and long-lasting properties.
It’s ideal for more heavy-duty applications where rollers are subjected to extreme conditions.
Production engineers must evaluate the application requirements, budget constraints, and expected workload to decide on the perfect material for the guide rollers.
Advanced Coatings and Treatments
Another approach to improving guide roller performance is utilizing advanced surface coatings and treatments.
Application of coatings like Teflon or chrome can provide added protection against wear, corrosion, and sticking, enhancing the roller’s lifespan.
Heat treatments are also beneficial, as they can increase the hardness and resilience of the roller material.
By integrating these technologies, production engineers can produce guide rollers that maintain optimal performance in demanding environments.
Design Considerations for Guide Rollers
While materials and treatments are crucial, the design of the guide rollers also contributes significantly to their functionality and durability.
Precision Engineering
Precision engineering ensures that guide rollers meet exact specifications necessary for consistent and reliable operation.
It involves intricate attention to details such as the diameter, surface texture, and balance of the rollers.
Achieving precise dimensions helps minimize vibration and noise, contributing to a smoother process.
Production engineers should incorporate the most advanced manufacturing technologies like CNC machines for accurate and repeatable outcomes.
Regular Maintenance and Inspection
Designing guide rollers for longevity also involves planning for regular maintenance and inspections.
Even the most well-designed rollers can degrade over time without proper upkeep.
Implementing a maintenance schedule helps detect early signs of wear or damage, preventing unexpected failures.
Moreover, regular inspections allow for timely adjustments or replacements, maintaining the overall efficiency and safety of the wood processing machines.
The Role of Technology in Manufacturing
Technology continually transforms the manufacturing landscape, and the production of guide rollers for wood processing is no exception.
Simulation and Testing
Before full-scale production, using simulation tools can help predict the performance of guide rollers under various conditions.
By analyzing different scenarios, production engineers can optimize the design for improved performance and durability, reducing the chances of errors and inefficiencies.
Physical testing is equally important, allowing engineers to verify the rollers’ performance in real-world applications.
This dual approach ensures that the final product is as robust and reliable as possible.
Automation and Quality Control
Automation in the manufacturing process can significantly enhance the quality and consistency of guide rollers.
Automated systems can handle intricate processes with high precision, ensuring each roller meets the required specifications.
Furthermore, utilizing quality control technologies such as laser measurements and digital imaging offers a precise way to monitor and evaluate the quality throughout the production process.
This adds another layer of assurance that the finished product will perform reliably.
Conclusion
For production engineers tasked with manufacturing guide rollers for wood processing machines, focusing on smooth operation and wear resistance is key.
By carefully selecting materials, utilizing advanced coatings and treatments, and investing in precision engineering, these critical components can perform optimally for an extended period.
Incorporating regular maintenance and leveraging technology for simulation, testing, and automation, further enhances their quality and durability.
Ultimately, this comprehensive approach not only extends the lifespan of the guide rollers but also contributes to the overall success and efficiency of wood processing operations.
資料ダウンロード
QCD調達購買管理クラウド「newji」は、調達購買部門で必要なQCD管理全てを備えた、現場特化型兼クラウド型の今世紀最高の購買管理システムとなります。
ユーザー登録
調達購買業務の効率化だけでなく、システムを導入することで、コスト削減や製品・資材のステータス可視化のほか、属人化していた購買情報の共有化による内部不正防止や統制にも役立ちます。
NEWJI DX
製造業に特化したデジタルトランスフォーメーション(DX)の実現を目指す請負開発型のコンサルティングサービスです。AI、iPaaS、および先端の技術を駆使して、製造プロセスの効率化、業務効率化、チームワーク強化、コスト削減、品質向上を実現します。このサービスは、製造業の課題を深く理解し、それに対する最適なデジタルソリューションを提供することで、企業が持続的な成長とイノベーションを達成できるようサポートします。
オンライン講座
製造業、主に購買・調達部門にお勤めの方々に向けた情報を配信しております。
新任の方やベテランの方、管理職を対象とした幅広いコンテンツをご用意しております。
お問い合わせ
コストダウンが利益に直結する術だと理解していても、なかなか前に進めることができない状況。そんな時は、newjiのコストダウン自動化機能で大きく利益貢献しよう!
(Β版非公開)