- お役立ち記事
- For new employees in the screw manufacturing industry for plastic molding machines! Designed for wear resistance and high precision
For new employees in the screw manufacturing industry for plastic molding machines! Designed for wear resistance and high precision
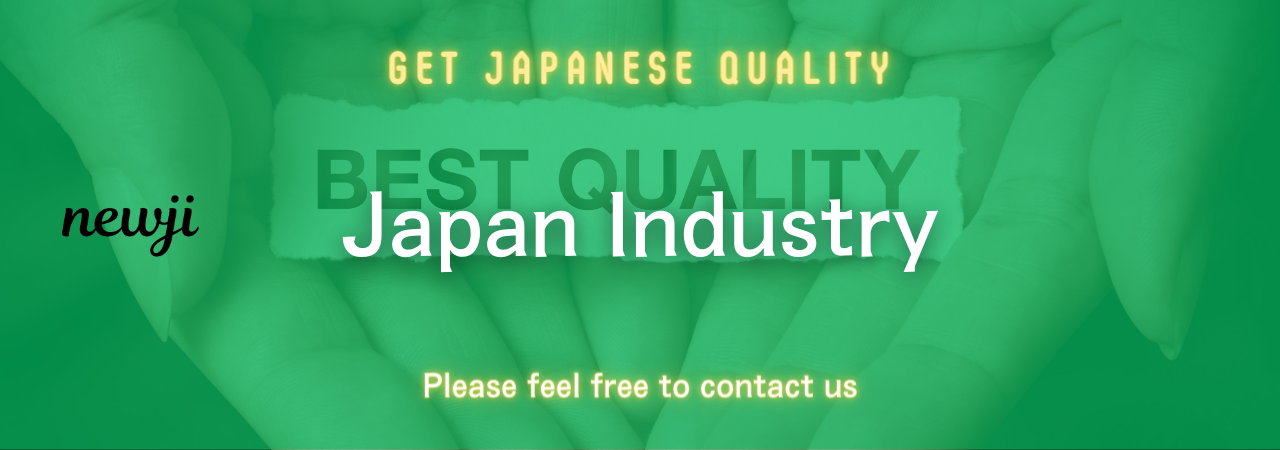
目次
Understanding the Importance of Wear Resistance and Precision
Entering the screw manufacturing industry, especially for plastic molding machines, can be an exciting yet daunting journey for new employees.
One of the primary aspects you’ll quickly come to appreciate is the importance of designing screws that boast high wear resistance and precision.
These attributes ensure the durability and accuracy of the machinery, which are critical for maintaining the quality and efficiency of the molding process.
Wear resistance is crucial because screws are constantly subjected to friction and pressure as they facilitate the plastic molding process.
Over time, these forces can lead to gradual deterioration of the screw if not properly accounted for in its design.
Engineers and manufacturers aim to use materials and coatings that can withstand these harsh conditions, which ultimately prolongs the machine’s lifespan and maintains production efficiency.
Precision, on the other hand, is about achieving exactness in the dimensions and functionality of the screws.
In plastic molding, even the smallest deviation in screw design can lead to defects in the final product.
Accuracy ensures that each mold is filled with the correct amount of material, reducing waste and ensuring consistent product quality.
Materials and Coatings That Enhance Wear Resistance
As a new employee in the screw manufacturing industry, you’ll find that selecting the right materials is a fundamental step.
Common materials used for manufacturing these screws include hardened steel, stainless steel, and sometimes even advanced ceramics.
Each of these materials offers different benefits and levels of wear resistance depending on the specific requirements of the plastic molding machine.
Hardened steel is often favored for its robustness and ability to endure significant mechanical stress.
It is frequently used in environments where heavy-duty processing is required.
Stainless steel, known for its anti-corrosive properties, is optimal in conditions where moisture could lead to rust and weaken the screw.
Advanced ceramics offer superior hardness and can significantly increase the screw’s lifespan, although they may come at a higher cost.
Additionally, coatings can play a pivotal role in enhancing wear resistance.
Coatings such as PVD (Physical Vapor Deposition), nitriding, or hard chrome plating create a protective layer on the screw surface, decreasing friction and enhancing durability.
Understanding the different material and coating combinations will be critical in your journey as you learn to design parts that meet the demands of modern plastic molding machines.
Advancing Precision with Cutting-edge Technology
Achieving high precision in screw manufacturing often involves leveraging advanced technology.
Computer Numerical Control (CNC) machines are paramount in this context, allowing manufacturers to produce screws with incredibly accurate specifications.
These machines are led by precise digital designs, enabling multifaceted cuts and designs that cannot be achieved through manual processes.
Furthermore, precision measurement tools, such as laser scanners and CMM (Coordinate Measuring Machines), allow manufacturers to verify the specifications of a screw down to the micron level.
This technology ensures that each screw meets strict standards before it’s deemed suitable for use in a machinery system.
New employees will benefit from learning how to operate and interpret data from these machines, therefore guaranteeing the reliability of the end product.
Quality assurance processes also advance precision in screw fabrication.
Implementing rigorous testing phases and adhering to international standards ensures that each screw consistently meets the high demands of plastic molding operations.
As you grow in your role, understanding these standards and integrating them into your production process is key to maintaining product integrity.
Application of Screws in Plastic Molding Machines
In plastic molding machines, screws play a vital role in the entirety of the production process.
Their primary function is to move, compress, and melt plastic materials before they are injected into a mold to form a product.
This requires careful consideration of the screw design, length, diameter, and pitch to ensure optimal processing efficiency.
Designing screws suitable for various types of plastic materials, such as thermoplastics or bioplastics, will be an inevitable part of your role.
Understanding the properties of these materials and how they interact with the screw during the molding process will help you design more efficient and specialized screws for specific applications.
Additionally, working in the screw manufacturing industry will also involve liaising with machine operators and engineers.
This collaboration ensures that the screws produced meet the specific requirements of different machines and manufacturing environments.
By engaging with these teams, new employees can gain insights into practical challenges and innovative solutions that improve screw performance.
Innovation and Future Trends in Screw Manufacturing
The screw manufacturing industry, particularly for plastic molding machines, is experiencing rapid innovation and change.
As a new employee, staying informed about future trends can provide you with an edge in this competitive field.
Sustainability is becoming increasingly important, pushing manufacturers to explore environmentally friendly materials and production processes.
Recyclable and biodegradable materials are being developed as alternatives to traditional metals and plastics, offering new challenges and opportunities in screw design and manufacturing.
Moreover, the integration of Internet of Things (IoT) in manufacturing processes allows real-time monitoring of machinery conditions.
This advancement can lead to preemptive maintenance and better resource management, ensuring prolonged machine life and optimizing efficiency.
Companies adopting IoT technology may require you to develop compatible screws or modify existing designs to meet these technological requirements.
Additive manufacturing, or 3D printing, is also beginning to impact the screw industry.
This technology makes it possible to create complex screw designs quickly and cost-effectively, potentially transforming traditional manufacturing processes.
Being adaptable and open to learning new technologies will be invaluable as you advance in your career.
In conclusion, entering the screw manufacturing industry for plastic molding machines opens up a world of opportunity for new employees.
By understanding the critical aspects of wear resistance and precision, learning about materials and technology, and staying informed about industry innovations, you can contribute significantly to the development and efficiency of modern plastic molding systems.
資料ダウンロード
QCD調達購買管理クラウド「newji」は、調達購買部門で必要なQCD管理全てを備えた、現場特化型兼クラウド型の今世紀最高の購買管理システムとなります。
ユーザー登録
調達購買業務の効率化だけでなく、システムを導入することで、コスト削減や製品・資材のステータス可視化のほか、属人化していた購買情報の共有化による内部不正防止や統制にも役立ちます。
NEWJI DX
製造業に特化したデジタルトランスフォーメーション(DX)の実現を目指す請負開発型のコンサルティングサービスです。AI、iPaaS、および先端の技術を駆使して、製造プロセスの効率化、業務効率化、チームワーク強化、コスト削減、品質向上を実現します。このサービスは、製造業の課題を深く理解し、それに対する最適なデジタルソリューションを提供することで、企業が持続的な成長とイノベーションを達成できるようサポートします。
オンライン講座
製造業、主に購買・調達部門にお勤めの方々に向けた情報を配信しております。
新任の方やベテランの方、管理職を対象とした幅広いコンテンツをご用意しております。
お問い合わせ
コストダウンが利益に直結する術だと理解していても、なかなか前に進めることができない状況。そんな時は、newjiのコストダウン自動化機能で大きく利益貢献しよう!
(Β版非公開)