- お役立ち記事
- A must-see for leaders in production control departments in the automobile industry! Operation guidelines for JIT (just-in-time) production systems
A must-see for leaders in production control departments in the automobile industry! Operation guidelines for JIT (just-in-time) production systems
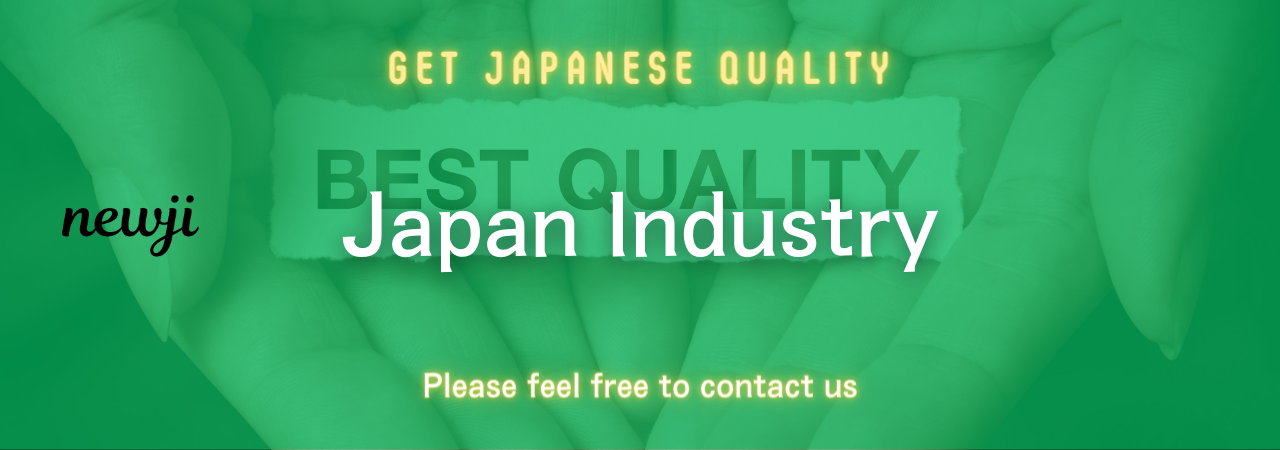
目次
Understanding Just-In-Time Production
Just-In-Time (JIT) production is a methodology that originated in the automobile industry, particularly with Toyota in Japan.
It revolves around reducing waste in production by receiving materials only as they are needed in the production process.
This helps to improve efficiency and decrease the need for holding excess inventory.
For leaders in production control departments, understanding and implementing JIT can significantly optimize operations and enhance product quality.
Key Principles of JIT Production
At its core, JIT relies on the efficient use of resources and the elimination of waste.
There are several key principles that guide JIT systems:
1. **Waste Reduction:** JIT focuses on eliminating waste throughout the production process.
This includes reducing overproduction, waiting times, transportation delays, and excess inventory.
2. **Continuous Improvement:** Also known as Kaizen, this principle involves constantly seeking ways to improve efficiency and quality in production processes.
3. **Pull System:** In a pull system, production is based on customer demand rather than forecasted demand.
Materials are only supplied when needed for production, minimizing inventory costs.
4. **Total Quality Management:** Ensuring high-quality products at every stage of production is critical. JIT emphasizes quality control and minimizes defects in the process.
The Benefits of JIT in the Automobile Industry
Implementing JIT in the automobile industry offers several benefits:
1. **Reduced Inventory Costs:** By delivering materials and components only when needed, JIT reduces the costs associated with storing inventory.
This leads to a more streamlined process and frees up capital for other uses.
2. **Enhanced Efficiency:** JIT creates a more efficient production line by minimizing downtime and reducing delays.
This allows automobile manufacturers to respond more swiftly to changes in customer demand.
3. **Improved Quality:** With a focus on quality control and eliminating defects, JIT systems can enhance the overall quality of manufactured vehicles.
By addressing quality issues early in the process, manufacturers can reduce waste and improve customer satisfaction.
4. **Flexibility:** JIT systems provide greater flexibility to adapt production schedules based on customer requirements.
This allows manufacturers to remain competitive in the fast-paced automobile market.
Steps to Implement JIT in Production Control
For leaders in production control departments, successfully implementing JIT involves several key steps:
Assess Current Processes
Begin by evaluating the current production processes to identify areas of waste and inefficiency.
This can include examining inventory levels, production timelines, and supply chain operations.
Set Clear Objectives
Clearly define the objectives of implementing JIT.
Whether it’s reducing costs, improving quality, or increasing efficiency, having clear goals helps guide the implementation process.
Engage the Team
Successful JIT implementation requires the engagement and cooperation of the entire team.
Ensure that all employees understand the principles of JIT and their roles in achieving the desired outcomes.
Strengthen Supplier Relationships
JIT relies heavily on reliable and timely deliveries from suppliers.
Develop strong relationships with suppliers to ensure a consistent flow of materials when needed.
Implement a Pull System
Shift from a push to a pull system by aligning production schedules more closely with customer demand.
Use real-time data and forecasts to adjust production accordingly.
Focus on Quality
Implement robust quality control measures to catch defects early in the process.
This not only enhances product quality but also reduces waste and rework.
Common Challenges and Solutions
While JIT offers numerous benefits, it also presents challenges:
Supply Chain Disruptions
JIT systems depend on timely deliveries from suppliers.
Disruptions in the supply chain can halt production and lead to delays.
**Solution:** Develop contingency plans and establish relationships with multiple suppliers to mitigate risks.
Demand Fluctuations
Variations in customer demand can impact production schedules and inventory levels.
**Solution:** Utilize forecasting and data analytics to better predict demand and adjust production accordingly.
Employee Resistance
Changes in processes can be met with resistance from employees.
**Solution:** Provide training and communicate the benefits of JIT clearly to all team members.
Empower employees to contribute ideas for improvement.
Conclusion
Implementing a Just-In-Time production system in the automobile industry can significantly improve efficiency, reduce costs, and enhance product quality.
By understanding the key principles and taking proactive steps to address potential challenges, leaders in production control departments can successfully integrate JIT into their operations.
The journey towards a fully functional JIT system may require time and effort, but the long-term benefits for a company’s production process are well worth it.
資料ダウンロード
QCD調達購買管理クラウド「newji」は、調達購買部門で必要なQCD管理全てを備えた、現場特化型兼クラウド型の今世紀最高の購買管理システムとなります。
ユーザー登録
調達購買業務の効率化だけでなく、システムを導入することで、コスト削減や製品・資材のステータス可視化のほか、属人化していた購買情報の共有化による内部不正防止や統制にも役立ちます。
NEWJI DX
製造業に特化したデジタルトランスフォーメーション(DX)の実現を目指す請負開発型のコンサルティングサービスです。AI、iPaaS、および先端の技術を駆使して、製造プロセスの効率化、業務効率化、チームワーク強化、コスト削減、品質向上を実現します。このサービスは、製造業の課題を深く理解し、それに対する最適なデジタルソリューションを提供することで、企業が持続的な成長とイノベーションを達成できるようサポートします。
オンライン講座
製造業、主に購買・調達部門にお勤めの方々に向けた情報を配信しております。
新任の方やベテランの方、管理職を対象とした幅広いコンテンツをご用意しております。
お問い合わせ
コストダウンが利益に直結する術だと理解していても、なかなか前に進めることができない状況。そんな時は、newjiのコストダウン自動化機能で大きく利益貢献しよう!
(Β版非公開)