- お役立ち記事
- A must-see for quality assurance department managers! How to thoroughly identify the cause of defects using why-why analysis
A must-see for quality assurance department managers! How to thoroughly identify the cause of defects using why-why analysis
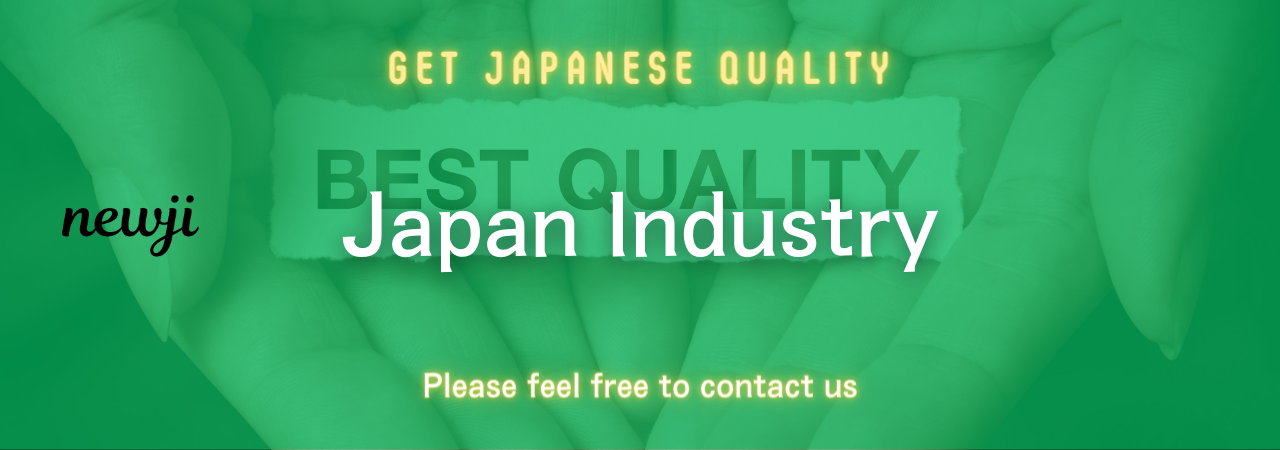
目次
Understanding Why-Why Analysis
Why-why analysis is a methodical approach used to identify the root causes of defects and problems in a process or product.
This technique involves asking “why” multiple times, typically five, to drill down into the layers of a problem and uncover underlying issues that may not be immediately apparent.
By doing so, teams can move beyond addressing symptoms and aim for long-lasting solutions that prevent recurrence.
The Importance of Identifying Root Causes
For quality assurance department managers, pinpointing the root cause of defects is crucial.
Without a thorough understanding of the underlying issues, any corrective actions taken might be temporary or ineffective.
By focusing on the reason behind a defect rather than just its symptom, organizations can improve processes, enhance product quality, and reduce costs associated with rework or recalls.
Getting Started with Why-Why Analysis
Step 1: Assemble the Right Team
The first step in conducting a successful why-why analysis is to gather a cross-functional team.
This group should comprise individuals with varying expertise related to the process or product affected by the defect.
Their diverse perspectives will help uncover different aspects of the problem.
Step 2: Clearly Define the Problem
Before diving into the analysis, clearly articulate the problem that needs to be addressed.
Everyone involved should have a shared understanding of what the defect is and its impact on the process or product.
Step 3: Start Asking “Why”
Begin by asking why the defect occurred.
Document the answer and then ask “why” again based on that response.
Continue this process, delving deeper with each question, until you’ve asked “why” at least five times or until a root cause is identified.
Example of a Why-Why Analysis
Let’s consider a hypothetical case where a manufacturing facility experiences frequent machine breakdowns.
Here’s how a why-why analysis might proceed:
1. **Why did the machine break down?**
– It overheated.
2. **Why did it overheat?**
– The cooling system failed.
3. **Why did the cooling system fail?**
– The coolant was not circulating properly.
4. **Why was the coolant not circulating properly?**
– The pump malfunctioned.
5. **Why did the pump malfunction?**
– It wasn’t serviced on schedule due to a miscommunication.
As seen above, the root cause was a lack of regular servicing due to miscommunication.
Addressing this issue by improving communication and establishing a robust maintenance schedule could prevent future breakdowns.
Benefits of Why-Why Analysis
Why-why analysis has several benefits for quality assurance managers and their teams:
– **Improved Process Understanding:**
Team members gain a better grasp of the process or system, which can lead to further enhancements.
– **Prevention of Recurrence:**
By addressing root causes instead of symptoms, organizations can implement changes that prevent future defects.
– **Reduction in Costs:**
Effective root cause identification reduces costs associated with handling defects, such as rework, recalls, and lost customer trust.
– **Enhanced Collaboration:**
The collaborative nature of why-why analysis fosters team communication and engagement, leading to a more cohesive problem-solving effort.
Challenges and Tips for Effective Why-Why Analysis
While why-why analysis is a powerful tool, it does come with potential challenges.
Here are some tips to overcome them:
– **Avoiding Assumptions:**
Ensure that every answer is evidence-based.
Assumptions can lead the analysis astray.
– **Being Comprehensive:**
Sometimes, asking “why” needs to expand beyond five times to identify the real root cause.
– **Involving the Right People:**
Include team members with firsthand knowledge of the process or product to provide accurate insights.
– **Documenting the Process:**
Keep detailed records of the questions and answers to ensure clarity and facilitate future analysis if needed.
Conclusion
For quality assurance department managers, mastering the art of why-why analysis is critical to resolving defects effectively.
By systematically identifying root causes, organizations can achieve greater product quality, customer satisfaction, and operational efficiency.
Incorporating why-why analysis into regular problem-solving activities will bolster a culture of continuous improvement and pave the way for sustained success.
資料ダウンロード
QCD調達購買管理クラウド「newji」は、調達購買部門で必要なQCD管理全てを備えた、現場特化型兼クラウド型の今世紀最高の購買管理システムとなります。
ユーザー登録
調達購買業務の効率化だけでなく、システムを導入することで、コスト削減や製品・資材のステータス可視化のほか、属人化していた購買情報の共有化による内部不正防止や統制にも役立ちます。
NEWJI DX
製造業に特化したデジタルトランスフォーメーション(DX)の実現を目指す請負開発型のコンサルティングサービスです。AI、iPaaS、および先端の技術を駆使して、製造プロセスの効率化、業務効率化、チームワーク強化、コスト削減、品質向上を実現します。このサービスは、製造業の課題を深く理解し、それに対する最適なデジタルソリューションを提供することで、企業が持続的な成長とイノベーションを達成できるようサポートします。
オンライン講座
製造業、主に購買・調達部門にお勤めの方々に向けた情報を配信しております。
新任の方やベテランの方、管理職を対象とした幅広いコンテンツをご用意しております。
お問い合わせ
コストダウンが利益に直結する術だと理解していても、なかなか前に進めることができない状況。そんな時は、newjiのコストダウン自動化機能で大きく利益貢献しよう!
(Β版非公開)