- お役立ち記事
- For managers of production technology departments in the auto parts industry! How to increase production efficiency with laser welding technology
For managers of production technology departments in the auto parts industry! How to increase production efficiency with laser welding technology
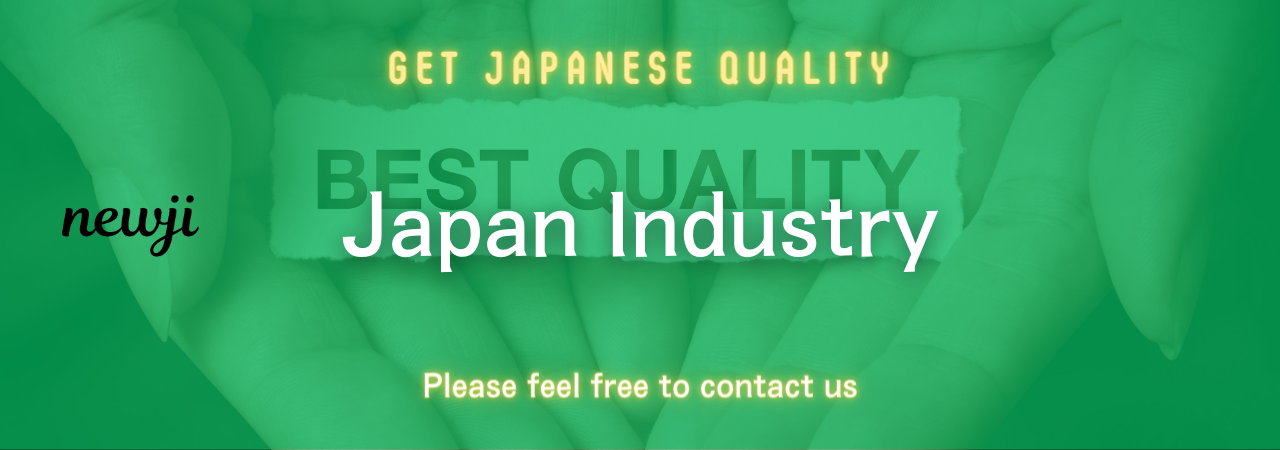
目次
Introduction to Laser Welding Technology
In the rapidly evolving auto parts industry, increasing production efficiency is a constant challenge faced by managers of production technology departments.
Laser welding technology offers a promising solution to enhance efficiency and productivity.
This advanced technique utilizes concentrated beams of light to heat materials, creating precise and strong welds without extensive tooling or manual intervention.
This article explores how laser welding technology can revolutionize production processes and provide a competitive edge.
Understanding Laser Welding
Laser welding involves a process where a laser beam is directed onto materials to fuse them together.
The high energy of the laser beam melts the material, allowing it to coalesce and form a bond.
This method is known for its precision and speed, making it an attractive choice for auto parts manufacturers.
There are several types of laser welding techniques, including keyhole welding and conduction welding.
Keyhole welding is ideal for joining thicker materials, while conduction welding is suitable for thinner layers.
Both techniques offer unique benefits, depending on the application.
Benefits of Laser Welding in Auto Parts Manufacturing
Precision and Accuracy
One of the primary advantages of laser welding is the high level of precision it offers.
The laser’s focused energy can create extremely accurate welds, essential for the intricate parts used in automobiles.
This precision reduces the need for post-weld finishing and ensures consistent quality across production runs.
Increased Speed and Efficiency
Laser welding is significantly faster than traditional welding methods, such as TIG or MIG welding.
The rapid execution of the laser beam reduces cycle times and increases throughput, enabling manufacturers to meet high demands efficiently.
This speed advantage is crucial in maintaining competitiveness in the auto parts industry.
Minimal Distortion and Stronger Welds
The concentrated energy of laser welding results in less thermal distortion.
This means parts maintain their desired shape, size, and mechanical properties better than with conventional welding methods.
Moreover, the resulting welds are often stronger, providing enhanced performance and longevity of the auto parts.
Considerations for Implementing Laser Welding
Initial Investment and Training
While the benefits of laser welding are immense, the initial investment can be significant.
Laser welding equipment is more expensive than traditional welding setups.
Additionally, staff training is crucial to ensure the correct handling and operation of the equipment.
However, the long-term gains in productivity and efficiency can outweigh the initial costs.
Material Compatibility
Not all materials are suitable for laser welding.
Managers must consider the types of materials commonly used in their production processes and whether laser welding will be effective.
Materials like aluminum and certain high-strength alloys may require adjustments to laser settings or complementary techniques.
Safety Measures
Laser systems can pose risks, such as exposure to high-intensity light and potential hazards from reflected beams.
Implementing proper safety measures and ensuring that operators are adequately trained to manage these risks is essential.
This includes protective eyewear, designated laser-safe areas, and regular safety audits.
Steps to Integrate Laser Welding into Production
Evaluate Current Production Processes
Begin by analyzing current welding processes to identify bottlenecks or areas where laser welding could offer improvements.
Understanding these key areas helps managers make a more informed decision on integrating laser technology.
Consult with Laser Welding Experts
Engage with experts in laser welding technology to gain insights into the best practices and equipment options for your specific needs.
These consultations will guide you in selecting the appropriate machinery and adapting your production processes.
Plan for a Pilot Program
Before a full-scale implementation, conduct a pilot program to assess the impact of laser welding on productivity, quality, and cost.
This trial phase allows managers to gather valuable data and make adjustments before full-scale adoption.
Train and Upskill Workforce
Provide comprehensive training for operators and technicians who will handle laser welding equipment.
Ensuring the workforce is proficient in using new technology minimizes errors and augments production efficiency.
Conclusion: The Future of Production with Laser Welding
As the auto parts industry continues to evolve, managers must explore innovative ways to boost efficiency and quality.
Laser welding presents a forward-thinking solution with the potential to transform production processes.
By harnessing its benefits of precision, speed, and enhanced quality, production technology departments can significantly optimize their operations.
While the initial investment and learning curve exist, the long-term advantages make laser welding a valuable asset in the quest for higher productivity.
By adopting laser welding technology, managers not only improve their current production capabilities but also position themselves for future industry advancements.
資料ダウンロード
QCD調達購買管理クラウド「newji」は、調達購買部門で必要なQCD管理全てを備えた、現場特化型兼クラウド型の今世紀最高の購買管理システムとなります。
ユーザー登録
調達購買業務の効率化だけでなく、システムを導入することで、コスト削減や製品・資材のステータス可視化のほか、属人化していた購買情報の共有化による内部不正防止や統制にも役立ちます。
NEWJI DX
製造業に特化したデジタルトランスフォーメーション(DX)の実現を目指す請負開発型のコンサルティングサービスです。AI、iPaaS、および先端の技術を駆使して、製造プロセスの効率化、業務効率化、チームワーク強化、コスト削減、品質向上を実現します。このサービスは、製造業の課題を深く理解し、それに対する最適なデジタルソリューションを提供することで、企業が持続的な成長とイノベーションを達成できるようサポートします。
オンライン講座
製造業、主に購買・調達部門にお勤めの方々に向けた情報を配信しております。
新任の方やベテランの方、管理職を対象とした幅広いコンテンツをご用意しております。
お問い合わせ
コストダウンが利益に直結する術だと理解していても、なかなか前に進めることができない状況。そんな時は、newjiのコストダウン自動化機能で大きく利益貢献しよう!
(Β版非公開)