- お役立ち記事
- GMP-compliant equipment maintenance and maintenance that new employees in the equipment management department of the pharmaceutical manufacturing industry should know.
GMP-compliant equipment maintenance and maintenance that new employees in the equipment management department of the pharmaceutical manufacturing industry should know.
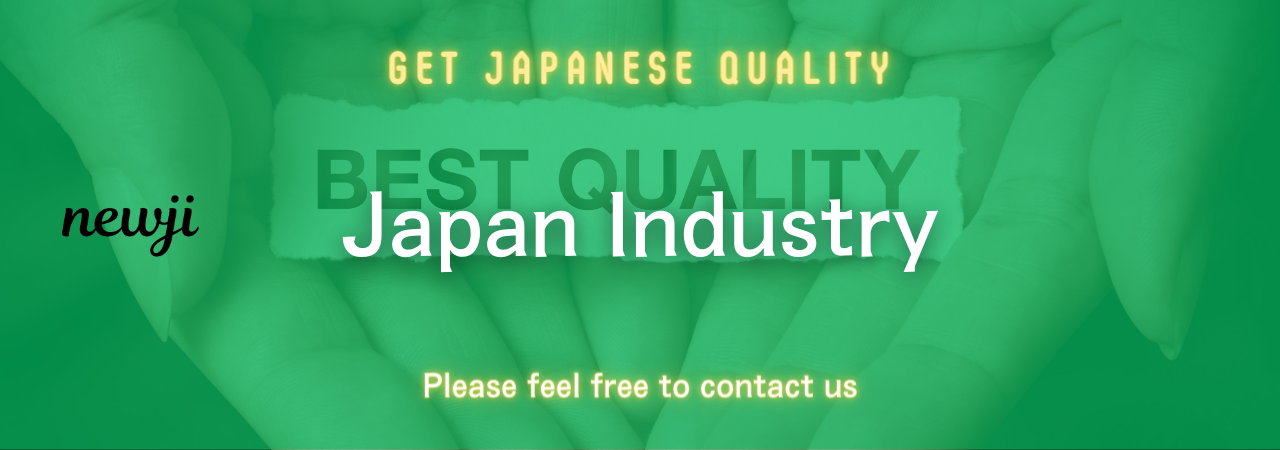
目次
Introduction to GMP Compliance
Good Manufacturing Practice (GMP) is a system that ensures products are consistently produced and controlled according to quality standards.
Globally, GMP compliance is essential in the pharmaceutical manufacturing industry to safeguard the health of consumers by ensuring that drugs meet high-quality standards.
For new employees in the equipment management department, understanding GMP compliance is crucial to maintaining the integrity of the manufacturing process.
This involves not only the operation of equipment but also routine maintenance and validation.
Understanding GMP Standards
What is GMP?
GMP is a set of guidelines that outlines the minimally acceptable standards in the production of pharmaceuticals and other health-related products.
It covers all aspects of production from raw materials, facilities, equipment, training, and personal hygiene to end products, ensuring the products not only meet quality standards but are also safe for consumer use.
The scope of GMP encompasses the entire production process, including the machines and equipment used in manufacturing.
This brings us to the importance of maintaining GMP-compliant equipment.
Why is GMP Equipment Maintenance Important?
Adhering to GMP standards isn’t just about product quality; it is vital for legal compliance and to avoid costly recalls and reputational damage.
Proper equipment maintenance ensures that machinery operates efficiently and reduces the risk of contamination, errors, or breakdowns that could interrupt production and compromise product quality.
Regular maintenance also prolongs the life of equipment, making it a cost-effective strategy in the long run.
New employees must understand that maintenance is not a one-time task but a continuous process that is critical in a GMP environment.
Maintenance Planning and Scheduling
Developing a Maintenance Plan
A well-structured maintenance plan is crucial.
It should include detailed procedures for routine inspections, cleaning, lubrication, adjustments, and repairs.
Each piece of equipment will have specific needs based on its function in the production line.
The plan should be adaptable and reviewed periodically to incorporate technological advances or changes in production requirements.
Scheduling Regular Maintenance
Effective scheduling ensures maintenance tasks do not disrupt the production process.
New employees should familiarize themselves with the concept of planned downtime, which is strategically integrated into the production schedule to allow for maintenance without impacting productivity severely.
Using software tools for scheduling can streamline this process, providing reminders for upcoming maintenance activities and keeping a record of past maintenance tasks.
Executing Maintenance Procedures
Training and Documentation
All staff involved in maintenance should receive thorough training on GMP standards and equipment-specific procedures.
Training ensures maintenance is performed correctly and consistently.
It is equally important to maintain detailed documentation of all maintenance activities.
Records should include the type of maintenance performed, the date, any parts that were replaced, observations during maintenance, and names of personnel involved.
This documentation is crucial during inspections to demonstrate compliance and traceability.
Implementation of Inspection Checks
Routine inspections are an integral part of maintenance.
Regular checks allow for early detection of potential issues, which can be resolved before leading to breakdowns or affecting product quality.
Checklists for each piece of equipment should clearly outline inspection criteria to ensure thorough reviews are conducted.
Validation and Calibration
The Role of Validation
Validation is the process of proving that equipment and processes will reliably produce the desired outcomes.
For new employees, understanding the role of validation in GMP is important as it confirms that equipment consistently operates within specified limits and produces conforming products.
Validation should be documented thoroughly, including performance qualifications and operational qualifications, to ensure compliance with GMP standards.
Importance of Calibration
Calibration of equipment is essential in ensuring precision and accuracy in measurements that affect product quality.
This involves adjusting the equipment to meet the manufacturer’s specifications.
Routine calibration should be part of the standard practice in equipment maintenance.
New employees should ensure that calibration records are meticulously kept and updated, serving as proof of compliance and contributing to a culture of quality assurance in the company.
Conclusion
For new employees in the equipment management department, mastering the principles of GMP-compliant equipment maintenance is crucial.
It supports the safe and efficient production of pharmaceuticals, ensuring products meet high-quality standards and regulatory compliance.
By understanding and implementing GMP practices, new employees can help to uphold the reputation and reliability of their manufacturing processes, which ultimately safeguards consumer health and aligns with the core objectives of the pharmaceutical industry.
資料ダウンロード
QCD調達購買管理クラウド「newji」は、調達購買部門で必要なQCD管理全てを備えた、現場特化型兼クラウド型の今世紀最高の購買管理システムとなります。
ユーザー登録
調達購買業務の効率化だけでなく、システムを導入することで、コスト削減や製品・資材のステータス可視化のほか、属人化していた購買情報の共有化による内部不正防止や統制にも役立ちます。
NEWJI DX
製造業に特化したデジタルトランスフォーメーション(DX)の実現を目指す請負開発型のコンサルティングサービスです。AI、iPaaS、および先端の技術を駆使して、製造プロセスの効率化、業務効率化、チームワーク強化、コスト削減、品質向上を実現します。このサービスは、製造業の課題を深く理解し、それに対する最適なデジタルソリューションを提供することで、企業が持続的な成長とイノベーションを達成できるようサポートします。
オンライン講座
製造業、主に購買・調達部門にお勤めの方々に向けた情報を配信しております。
新任の方やベテランの方、管理職を対象とした幅広いコンテンツをご用意しております。
お問い合わせ
コストダウンが利益に直結する術だと理解していても、なかなか前に進めることができない状況。そんな時は、newjiのコストダウン自動化機能で大きく利益貢献しよう!
(Β版非公開)