- お役立ち記事
- Specific approaches to “yield improvement”—Indicators and improvement methods that manufacturing managers should be aware of
Specific approaches to “yield improvement”—Indicators and improvement methods that manufacturing managers should be aware of
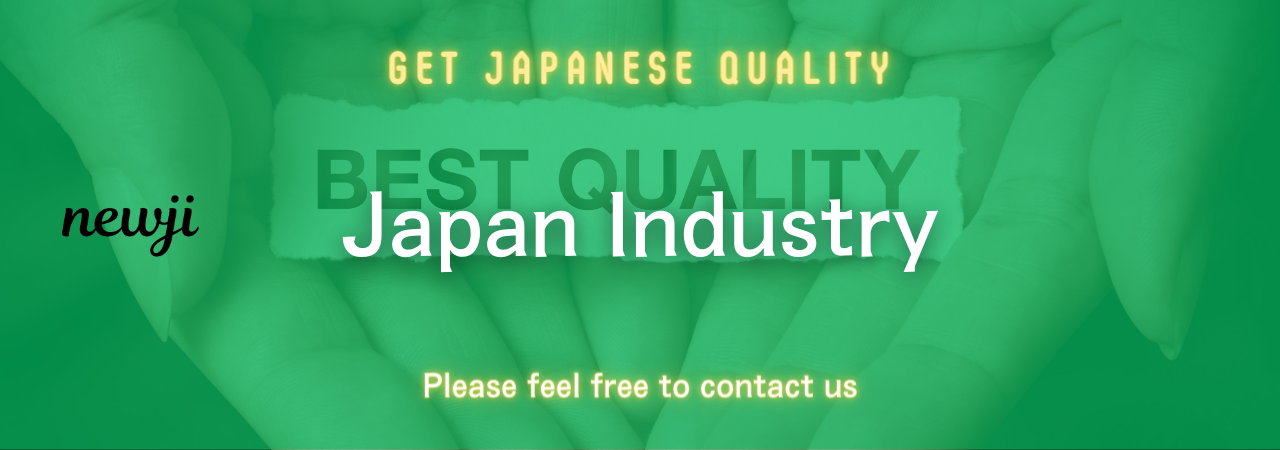
目次
Understanding Yield Improvement
In the manufacturing industry, enhancing production efficiency is a primary goal for managers to ensure profitability and competitiveness.
Yield improvement represents one crucial aspect of this efficiency, referring to the percentage of products that meet quality standards without requiring rework.
It is a key indicator of how effectively a manufacturing process is operating.
By focusing on yield improvement, companies can significantly reduce waste, lower costs, and increase overall production quality.
The Importance of Yield Improvement Indicators
Yield improvement indicators are essential tools that help manufacturing managers understand current production efficiency and identify areas needing attention.
These indicators can guide decision-making processes by providing quantitative data on production performance.
The main indicators include the First Pass Yield (FPY), scrap rates, rework percentages, and Total Productive Maintenance (TPM) metrics.
The First Pass Yield is one critical metric that measures the percentage of products manufactured correctly without any need for rework.
A higher FPY indicates a highly efficient production process, while a lower FPY suggests potential inefficiencies that need addressing.
Scrap rates and rework percentages highlight the proportion of materials wasted or products needing correction, directly impacting overall yield and cost.
Total Productive Maintenance focuses on the efficiency of equipment and machinery involved in production.
Regular maintenance and attention to machinery health can prevent downtime and ensure consistent product quality, contributing to improved yields.
Steps to Improve Yield in Manufacturing
Improving yield in manufacturing involves a comprehensive approach that considers process efficiency, employee training, and the use of advanced technologies.
Below are specific strategies that manufacturing managers can use to enhance yield.
Streamlining Processes
One of the first steps towards yield improvement is streamlining manufacturing processes.
This involves evaluating each process stage to identify bottlenecks and inefficiencies.
Managers should employ lean manufacturing principles, which emphasize value stream mapping and continuous improvement initiatives.
By eliminating unnecessary steps and simplifying workflows, production can operate more effectively, thus improving yield.
It’s also critical to establish clear standard operating procedures (SOPs) for each production stage.
SOPs ensure consistency in operations and reduce the chances of errors, directly impacting the yield positively.
Employee Training and Engagement
Employees play a crucial role in achieving high yields.
Investing in comprehensive training programs ensures that workers are equipped with the necessary skills and knowledge to perform their tasks efficiently.
This includes educating them on the importance of quality control and how their specific roles contribute to overall yield.
Encouraging a culture of continuous improvement among employees can also foster proactive problem-solving and innovation.
Managers should engage employees regularly, soliciting their feedback and involving them in process improvement discussions.
By empowering workers, there is a collective movement towards enhancing yield and quality.
Implementing Advanced Technologies
Advancements in technology can significantly aid in yield improvement.
The incorporation of automation and robotics can enhance precision, reduce human error, and speed up production processes.
Automated systems can consistently perform repetitive tasks with high accuracy, thus improving yield.
Furthermore, the integration of data analytics and IoT in manufacturing can provide actionable insights into production performance.
By analyzing data in real-time, managers can quickly identify process issues, monitor machine health, and optimize resource allocation to boost yield.
Regular Monitoring and Analysis
Continuous monitoring and analysis of production processes are paramount for maintaining high yield levels.
Manufacturing managers must consistently review performance data to track the effectiveness of implemented strategies.
Regular audits and inspections help identify potential issues before they become significant problems, allowing for timely interventions.
Implementing a comprehensive quality management system (QMS) can standardize monitoring processes and maintain a high product quality level.
By setting quality benchmarks and establishing regular metrics reviews, manufacturers can sustain high yields and identify areas for continued improvement.
Root Cause Analysis
Whenever production issues impact yield, conducting a root cause analysis is vital to identify underlying problems.
By employing techniques such as the “5 Whys” or fishbone diagram analyses, managers can pinpoint the exact causes of inefficiencies and implement effective corrective actions.
Understanding the root causes not only resolves immediate problems but also prevents the recurrence of similar issues, thereby enhancing yield over the long term.
Conclusion
Yield improvement is a multifaceted approach that requires ongoing effort and attention from manufacturing managers.
By focusing on key performance indicators, streamlining processes, engaging employees, leveraging advanced technologies, and maintaining consistent monitoring, companies can enhance their production yields substantially.
These strategies lead to reduced waste, lower operational costs, and higher product quality, ultimately promoting a more profitable and competitive manufacturing operation.
For managers overseeing these processes, a commitment to continuous improvement and adaptability to emerging technologies is crucial in the pursuit of excellence in yield improvement.
資料ダウンロード
QCD調達購買管理クラウド「newji」は、調達購買部門で必要なQCD管理全てを備えた、現場特化型兼クラウド型の今世紀最高の購買管理システムとなります。
ユーザー登録
調達購買業務の効率化だけでなく、システムを導入することで、コスト削減や製品・資材のステータス可視化のほか、属人化していた購買情報の共有化による内部不正防止や統制にも役立ちます。
NEWJI DX
製造業に特化したデジタルトランスフォーメーション(DX)の実現を目指す請負開発型のコンサルティングサービスです。AI、iPaaS、および先端の技術を駆使して、製造プロセスの効率化、業務効率化、チームワーク強化、コスト削減、品質向上を実現します。このサービスは、製造業の課題を深く理解し、それに対する最適なデジタルソリューションを提供することで、企業が持続的な成長とイノベーションを達成できるようサポートします。
オンライン講座
製造業、主に購買・調達部門にお勤めの方々に向けた情報を配信しております。
新任の方やベテランの方、管理職を対象とした幅広いコンテンツをご用意しております。
お問い合わせ
コストダウンが利益に直結する術だと理解していても、なかなか前に進めることができない状況。そんな時は、newjiのコストダウン自動化機能で大きく利益貢献しよう!
(Β版非公開)