- お役立ち記事
- For managers of design departments in the plastic molding industry! Implementation of gas-assisted molding and key points for weight reduction of parts
For managers of design departments in the plastic molding industry! Implementation of gas-assisted molding and key points for weight reduction of parts
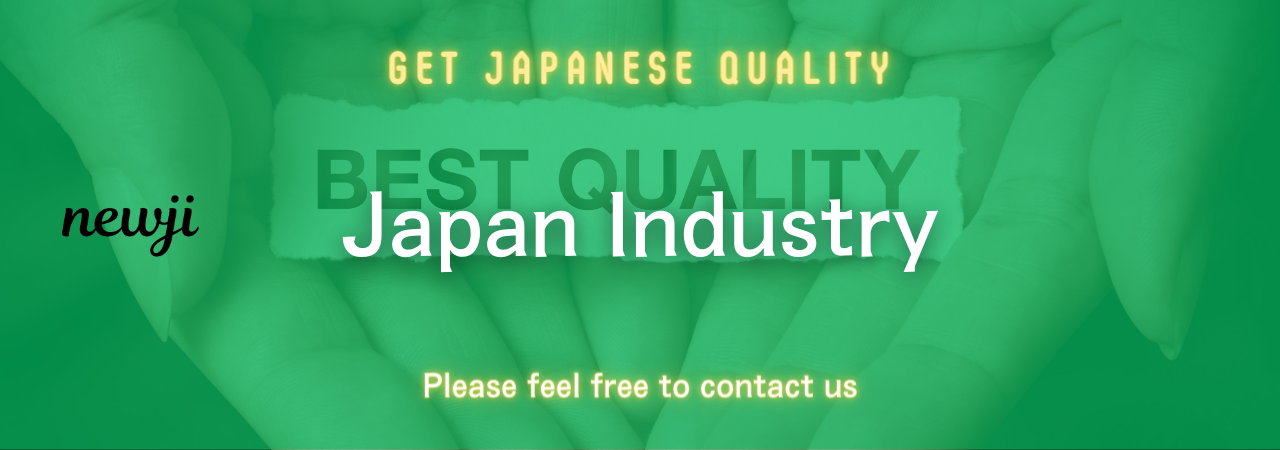
目次
Understanding Gas-Assisted Molding
Gas-assisted molding is an advanced manufacturing technique that offers numerous benefits for the plastic molding industry.
It involves injecting a compressed gas, typically nitrogen, into the mold cavity during the molding process.
This technique helps displace the molten plastic towards the mold’s extremities, resulting in hollow parts with reduced weight and increased structural integrity.
The use of gas-assisted molding is integral for modern manufacturing processes.
Its ability to produce lighter components without compromising the strength of the final product is highly desirable.
Additionally, it offers cost-effective solutions, reducing material consumption and cycle time in production.
Key Advantages of Gas-Assisted Molding
One of the standout benefits of gas-assisted molding is the reduction in part weight.
By using a gas intrusion process, this method can produce parts with hollow sections.
This leads to lighter products, which are ideal for industries aiming for sustainability and efficiency.
Besides weight reduction, this process also reduces the stress and warping commonly associated with traditional molding techniques.
It helps in minimizing sink marks and improving the overall surface quality of the finished parts.
Another benefit is the ability to make complex shapes and designs with high dimensional accuracy.
This flexibility allows design departments to experiment with innovative designs without the typical constraints of solid molding.
Key Points for Implementing Gas-Assisted Molding
To successfully implement gas-assisted molding, several critical aspects must be considered.
Understanding these elements will ensure the manufacturing process is seamless and delivers optimal results.
Mold Design Considerations
The mold design is one of the most pivotal factors in gas-assisted molding.
It should be tailored to accommodate the injection and distribution of gas.
Venting channels need to be precisely designed to control the flow and release of gas from the mold cavity.
Moreover, the mold must be robust enough to withstand the pressures involved in the gas injection process.
Material selection for mold construction should reflect durability and resistance to wear and tear.
Control and Monitoring
Proper control and monitoring of the gas-assisted process are critical.
The pressure, temperature, and timing of gas injection are all essential parameters.
Automated systems can help maintain the integrity of these variables, ensuring consistent quality and efficiency.
Maintaining the right balance of gas and plastic is crucial to producing components with the desired physical properties.
Material Selection
Choosing the right material is fundamental for achieving optimal results with gas-assisted molding.
Thermoplastics such as polypropylene, ABS, and polycarbonate are commonly used.
These materials exhibit desirable flow characteristics and react well to the gas penetration process.
Additionally, the material must be compatible with the intended application, considering factors such as mechanical strength, thermal resistance, and surface finish.
Strategies for Weight Reduction in Plastic Parts
Reducing the weight of plastic parts is a goal for many design departments.
Lighter parts contribute to eco-friendly practices and can lead to cost savings.
Design Optimization
To achieve weight reduction, employing design optimization techniques is crucial.
This involves using computer-aided design (CAD) software to simulate various design iterations.
Designers can experiment with thinner walls, optimized ribbing, and strategic placement of hollow sections, all contributing to lighter parts without compromising strength.
Material Innovation
Exploring new materials is another effective strategy.
Advancements in composite materials and high-performance polymers can offer improved strength-to-weight ratios.
These materials enable the production of durable and lightweight components, expanding the possibilities for design departments in the plastic molding industry.
Incorporation of Additive Manufacturing
Additive manufacturing, commonly known as 3D printing, can also assist in weight reduction strategies.
By fabricating prototypes and small-scale production runs, designers can test lightweight designs before mass production.
This approach facilitates a more agile design process, allowing for rapid iterations and feedback loops.
Conclusion
Gas-assisted molding presents immense potential for the plastic molding industry.
Its capability to produce lighter, structurally sound components is invaluable for manufacturers aiming to reduce material usage and costs.
Effective integration of this technology involves careful consideration of mold design, control systems, and material selection.
Moreover, combining gas-assisted molding with design optimization, exploring innovative materials, and leveraging additive manufacturing can further enhance weight reduction efforts.
By prioritizing these strategies, managers of design departments can lead the charge toward more sustainable and efficient production practices in the plastic molding industry.
資料ダウンロード
QCD調達購買管理クラウド「newji」は、調達購買部門で必要なQCD管理全てを備えた、現場特化型兼クラウド型の今世紀最高の購買管理システムとなります。
ユーザー登録
調達購買業務の効率化だけでなく、システムを導入することで、コスト削減や製品・資材のステータス可視化のほか、属人化していた購買情報の共有化による内部不正防止や統制にも役立ちます。
NEWJI DX
製造業に特化したデジタルトランスフォーメーション(DX)の実現を目指す請負開発型のコンサルティングサービスです。AI、iPaaS、および先端の技術を駆使して、製造プロセスの効率化、業務効率化、チームワーク強化、コスト削減、品質向上を実現します。このサービスは、製造業の課題を深く理解し、それに対する最適なデジタルソリューションを提供することで、企業が持続的な成長とイノベーションを達成できるようサポートします。
オンライン講座
製造業、主に購買・調達部門にお勤めの方々に向けた情報を配信しております。
新任の方やベテランの方、管理職を対象とした幅広いコンテンツをご用意しております。
お問い合わせ
コストダウンが利益に直結する術だと理解していても、なかなか前に進めることができない状況。そんな時は、newjiのコストダウン自動化機能で大きく利益貢献しよう!
(Β版非公開)