- お役立ち記事
- For equipment engineers in the precision machinery industry! How to maximize precision of carbide parts with wire-cut EDM
For equipment engineers in the precision machinery industry! How to maximize precision of carbide parts with wire-cut EDM
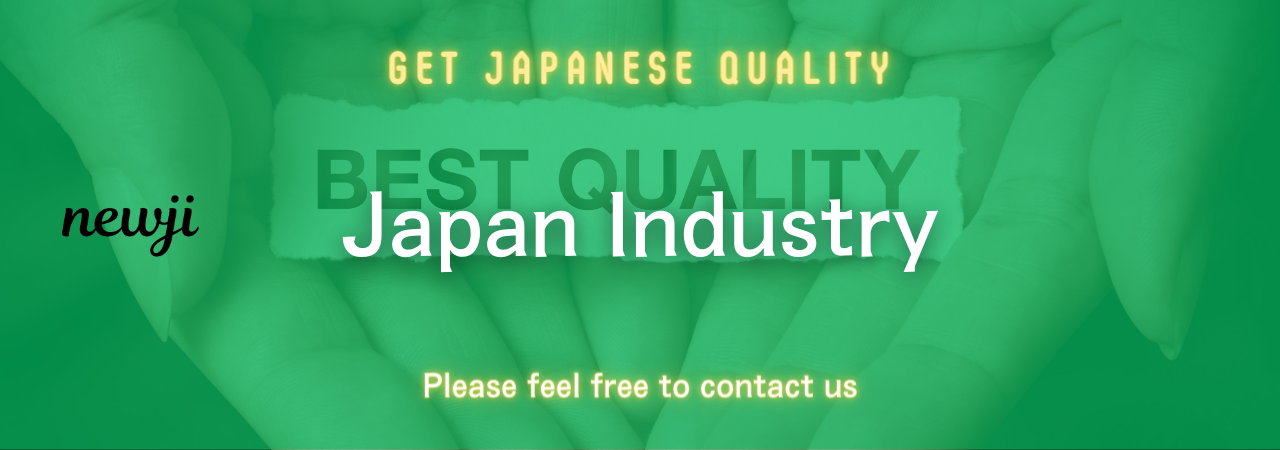
In the precision machinery industry, maintaining the highest levels of accuracy and precision is paramount.
Equipment engineers constantly seek methods and technologies that enhance the precision of their materials and products.
One such method that has gained considerable attention is Wire-Cut Electrical Discharge Machining (EDM), particularly when working with carbide parts.
This article explores how equipment engineers can maximize the precision of carbide parts using Wire-Cut EDM.
目次
Understanding Wire-Cut EDM
Wire-Cut EDM, also known as wire-cut electrical discharge machining, is a process that utilizes electrical discharges to cut complex shapes and delicate parts out of conductive materials.
This machining technique is renowned for its ability to produce precise, intricate designs without the need for physical cutting tools.
Instead, it employs a thin wire (usually made of brass or molybdenum) that creates a path for the electrical surge to cut through the material.
This method is exceptionally useful for materials that are difficult to machine with traditional methods, such as carbide.
The precision and control it offers make it a staple in the precision machinery industry.
Why Use Wire-Cut EDM for Carbide?
Carbide, a composite material made from carbon and metal, is beloved for its hardness and resistance to wear.
However, these same properties that make carbide desirable also pose challenges in machining.
Traditional cutting tools can struggle with carbide, causing damage or excessive wear to the tools themselves.
Wire-Cut EDM circumvents these issues as it does not involve direct physical contact with the material.
The electrical discharge erodes the material in a controlled manner, thus enabling clean, precise cuts on carbide.
This results in parts that maintain structural integrity while achieving desired specifications without the risk of tool wear or material damage.
Advantages of Wire-Cut EDM for Carbide Parts
The primary advantage of using Wire-Cut EDM for machining carbide is precision.
This method allows for tight tolerances, which are crucial in industries where errors can result in significant losses.
Furthermore, Wire-Cut EDM provides excellent surface finishes and can create complex geometries that are otherwise difficult to achieve.
Because of its non-contact nature, there is minimal risk of material distortion or stress, preserving the mechanical properties of the carbide.
Another advantage is its efficiency.
Wire-Cut EDM is an automated process, which minimizes the need for constant supervision and manual adjustments, freeing up time and resources.
Optimizing the Wire-Cut EDM Process
To maximize the precision of carbide parts using Wire-Cut EDM, equipment engineers must optimize various aspects of the process.
Here’s how:
1. Choose the Right Wire
The choice of wire is critical to success.
Brass and coated wires are commonly used for Wire-Cut EDM due to their conductivity and mechanical properties.
Each material and application may require a different type of wire, so it’s essential to select the wire that matches the characteristics of the carbide part to achieve optimal accuracy.
2. Calibrate the Machine
Proper calibration of the EDM machine ensures that it operates at peak performance.
This includes setting the correct electrical parameters, such as voltage and current, to match the specific requirements of the project.
Regular calibration and maintenance can prevent deviations that lead to imprecise cuts.
3. Control the Cutting Conditions
Monitoring and adjusting the cutting speed and feed rate are crucial in achieving the desired precision.
Slower cutting speeds typically result in higher precision and better surface finishes, though they may extend machining time.
Finding the right balance between speed and accuracy is essential for efficient production.
4. Cooling and Flushing
An effective cooling and flushing system is vital in the Wire-Cut EDM process.
Flushing helps to remove debris from the machining area, preventing re-cutting and ensuring that the electrical discharge operates effectively.
Coolants also help to dissipate heat, reducing thermal stress on the carbide part, which can impact precision.
5. Regular Inspection and Monitoring
Consistent inspection and monitoring of both the machinery and the workpieces throughout the process can help identify any deviations early.
This allows for real-time adjustments and corrections, maintaining the accuracy required in the final product.
Conclusion
Wire-Cut EDM has revolutionized the machining approach for hard, durable materials such as carbide.
Its precision, efficiency, and capability to produce intricate designs without compromising material integrity make it an invaluable tool in the precision machinery industry.
To maximize the benefits of Wire-Cut EDM, equipment engineers must carefully consider wire selection, machine calibration, cutting conditions, and regular inspection.
These factors are crucial for achieving the highest precision and ensuring that carbide parts meet exact specifications.
By mastering these aspects, equipment engineers can leverage the full potential of Wire-Cut EDM, delivering components that uphold the uncompromising standards of quality and performance demanded by the industry.
資料ダウンロード
QCD調達購買管理クラウド「newji」は、調達購買部門で必要なQCD管理全てを備えた、現場特化型兼クラウド型の今世紀最高の購買管理システムとなります。
ユーザー登録
調達購買業務の効率化だけでなく、システムを導入することで、コスト削減や製品・資材のステータス可視化のほか、属人化していた購買情報の共有化による内部不正防止や統制にも役立ちます。
NEWJI DX
製造業に特化したデジタルトランスフォーメーション(DX)の実現を目指す請負開発型のコンサルティングサービスです。AI、iPaaS、および先端の技術を駆使して、製造プロセスの効率化、業務効率化、チームワーク強化、コスト削減、品質向上を実現します。このサービスは、製造業の課題を深く理解し、それに対する最適なデジタルソリューションを提供することで、企業が持続的な成長とイノベーションを達成できるようサポートします。
オンライン講座
製造業、主に購買・調達部門にお勤めの方々に向けた情報を配信しております。
新任の方やベテランの方、管理職を対象とした幅広いコンテンツをご用意しております。
お問い合わせ
コストダウンが利益に直結する術だと理解していても、なかなか前に進めることができない状況。そんな時は、newjiのコストダウン自動化機能で大きく利益貢献しよう!
(Β版非公開)