- お役立ち記事
- Basics of etching technology and process control that new employees in the production technology department of the semiconductor industry should know
Basics of etching technology and process control that new employees in the production technology department of the semiconductor industry should know
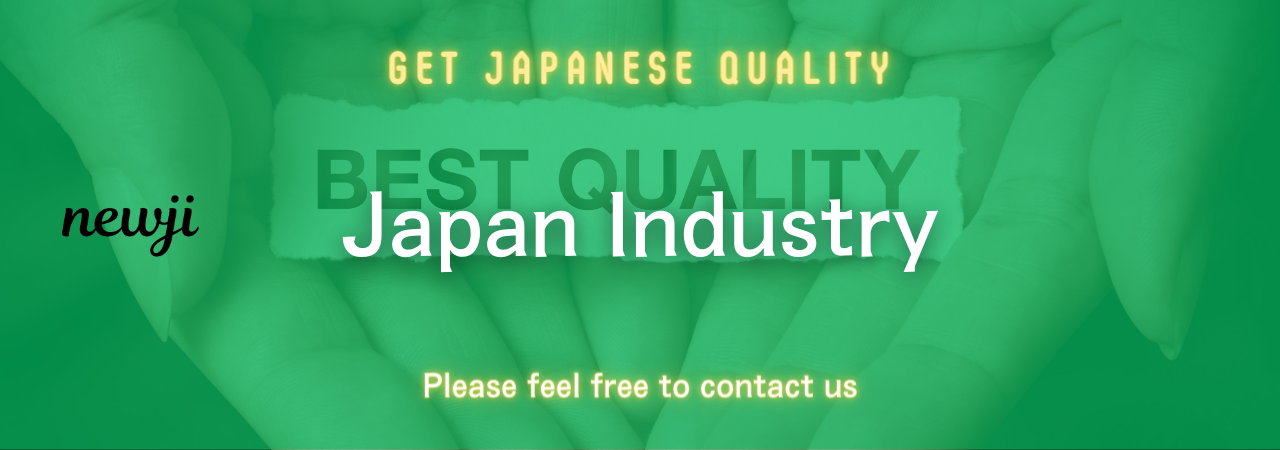
目次
Introduction to Etching Technology
Etching technology is a crucial aspect of semiconductor manufacturing, involving the process of removing layers from the surface of a wafer during the fabrication of integrated circuits.
Understanding its fundamentals is essential for new employees in the production technology department.
This process is vital for defining intricate patterns on the wafer, which are later transformed into functional components within a semiconductor device.
The Importance of Etching in Semiconductors
In the world of semiconductors, etching allows for precise patterning and layering required for complex circuits.
It plays a critical role in defining the transistor gates, contact holes, metal interconnects, and other microstructures.
Without accurate etching, the performance and reliability of semiconductor devices would be compromised.
Etching ensures that the devices’ physical layout meets the design specifications precisely, allowing for improved performance and efficiency.
Types of Etching Processes
There are primarily two types of etching processes used in semiconductor manufacturing: wet etching and dry etching.
Wet Etching
Wet etching involves using liquid chemicals to remove unwanted material from the wafer surface.
It is typically used for less complex features and provides good selectivity, meaning it can effectively etch the intended material while leaving other materials unscathed.
However, wet etching can be limited in precision and is often replaced by dry etching in applications requiring more exact control.
Dry Etching
Dry etching, also known as plasma etching, utilizes gas phase chemistry to achieve material removal.
This method involves ionizing gases and using reactive ions, atoms, or radicals to etch material from the wafer.
Dry etching offers greater precision compared to wet etching and is better suited for complex and high-resolution patterns.
It can be further classified into different types, such as reactive ion etching (RIE) and deep reactive ion etching (DRIE), each offering specific advantages for various applications.
Process Control in Etching
Effective process control is essential in etching to ensure consistent results and desired outcomes.
Process control involves monitoring and adjusting various parameters to maintain the quality and precision of the etching process.
Key Parameters in Etching
Several parameters must be precisely controlled during the etching process:
– **Etch Rate**: The speed at which material is removed. Controlling the etch rate ensures that the process does not exceed or fall short of the specification.
– **Selectivity**: The ability to etch the target material without significantly affecting other materials. High selectivity is essential to protect underlying layers and achieve the desired pattern.
– **Anisotropy**: The directional dependence of the etch rate. Anisotropic etching creates vertical sidewalls, which are critical for high-aspect-ratio structures.
– **Uniformity**: It is crucial to achieve uniform etching across the wafer to maintain consistent device performance across the entire semiconductor.
The Role of Chemistry and Equipment
The etching process relies on a blend of chemical reactions and advanced machinery to achieve the desired outcomes.
Chemicals in Etching
The selection of chemicals, either in gaseous or liquid form, plays a pivotal role in the etching process.
In wet etching, acids, bases, and oxidizing agents are commonly used, depending on the materials involved.
For dry etching, gases such as CF4, SF6, and Cl2 are utilized.
These gases undergo ionization under plasma conditions to form reactive ions capable of etching specific materials.
Equipment Used in Etching
State-of-the-art equipment is vital for precise and controlled etching.
In dry etching, reactors equipped with plasma generation capabilities are used to initiate and control the ionization process.
For wet etching, tanks and baths are often employed to immerse wafers in the chemical solutions required for the process.
Both types of equipment must be meticulously maintained and calibrated to ensure optimal performance and reliability.
Challenges in Etching and Solutions
Etching processes are complex and present several challenges that require careful management to avoid defects and achieve high yields.
Over-etching and Under-etching
Over-etching occurs when the etching process continues beyond the desired depth, potentially damaging underlying layers.
Conversely, under-etching results in incomplete pattern transfer.
Both scenarios can be mitigated by precise monitoring and control of etch rates and times.
Aspect Ratio and Maintaining Profile Integrity
Achieving high aspect ratios, where patterns are much deeper than they are wide, is increasingly challenging as technology advances.
Ensuring profile integrity, particularly in taller structures, requires precise anisotropic etching and advanced process control methodologies.
Conclusion
Understanding etching technology and its process control is fundamental for anyone entering the semiconductor industry, particularly for those in production technology departments.
Mastering the art of etching and navigating its complexities ensures the delivery of high-quality semiconductor devices with the desired performance attributes.
As the industry continues to advance, keeping up with state-of-the-art techniques and constantly refining skills is crucial for career growth and contributing effectively to semiconductor manufacturing processes.
資料ダウンロード
QCD調達購買管理クラウド「newji」は、調達購買部門で必要なQCD管理全てを備えた、現場特化型兼クラウド型の今世紀最高の購買管理システムとなります。
ユーザー登録
調達購買業務の効率化だけでなく、システムを導入することで、コスト削減や製品・資材のステータス可視化のほか、属人化していた購買情報の共有化による内部不正防止や統制にも役立ちます。
NEWJI DX
製造業に特化したデジタルトランスフォーメーション(DX)の実現を目指す請負開発型のコンサルティングサービスです。AI、iPaaS、および先端の技術を駆使して、製造プロセスの効率化、業務効率化、チームワーク強化、コスト削減、品質向上を実現します。このサービスは、製造業の課題を深く理解し、それに対する最適なデジタルソリューションを提供することで、企業が持続的な成長とイノベーションを達成できるようサポートします。
オンライン講座
製造業、主に購買・調達部門にお勤めの方々に向けた情報を配信しております。
新任の方やベテランの方、管理職を対象とした幅広いコンテンツをご用意しております。
お問い合わせ
コストダウンが利益に直結する術だと理解していても、なかなか前に進めることができない状況。そんな時は、newjiのコストダウン自動化機能で大きく利益貢献しよう!
(Β版非公開)