- お役立ち記事
- For new leaders in the production technology department of the auto parts manufacturing industry! Basics and applications of laser drilling
For new leaders in the production technology department of the auto parts manufacturing industry! Basics and applications of laser drilling
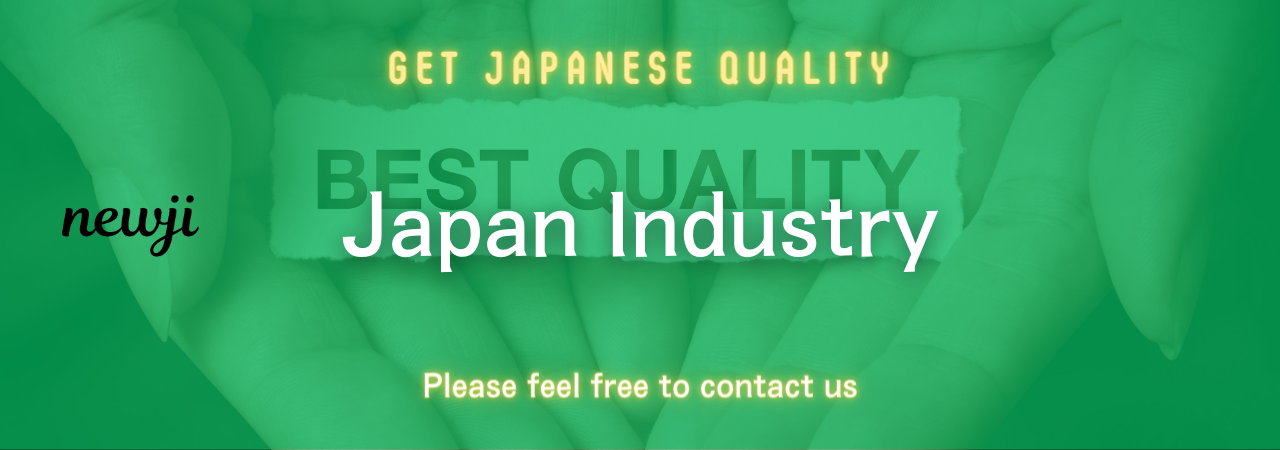
Understanding Laser Drilling in Auto Parts Manufacturing
In the auto parts manufacturing industry, various cutting-edge technologies are employed to enhance efficiency and precision.
One such innovative technology is laser drilling, a process that utilizes concentrated laser beams to create holes in materials.
For new leaders in the production technology department, understanding the basics and applications of laser drilling is crucial.
What is Laser Drilling?
Laser drilling is a non-contact process that uses a high-energy laser beam to remove material, creating holes through vaporization or melting.
This method is ideal for drilling precise and clean holes in different materials, including metals, plastics, and ceramics.
The laser’s ability to focus on very small areas makes it exceptionally precise, offering greater control over the drilling process compared to traditional methods.
How Does Laser Drilling Work?
The laser drilling process begins with directing a laser beam onto a specific spot on the material.
This beam is highly concentrated and can generate extreme heat.
When the beam makes contact with the material, it causes rapid heating, melting, and even vaporization of the material at the target spot.
Different types of lasers, such as CO2, Nd:YAG, and fiber lasers, can be employed, each with unique properties suitable for specific applications.
The choice of laser depends on factors such as material type, desired hole size, and production speed.
Advantages of Laser Drilling
Laser drilling offers several benefits over traditional drilling methods, making it a preferred choice in the automotive industry.
1. **Precision and Accuracy**: Laser drilling provides exceptional precision, capable of creating highly accurate holes with consistent quality.
This precision is vital in the manufacture of components that require exact specifications.
2. **Speed and Efficiency**: Laser drilling can be significantly faster than mechanical drilling, especially for small holes or complex geometries.
This speed translates into increased productivity and reduced lead times.
3. **Non-contact Process**: As a non-contact process, laser drilling minimizes the risk of mechanical wear and tear on the material.
This quality reduces the need for frequent maintenance and lowers the overall cost of production.
4. **Versatility**: The ability of laser drills to handle various materials and thicknesses makes them versatile tools in the production line.
They can efficiently drill through tough materials like steel or delicate ones like thin plastics.
5. **Minimal Deformation**: The high precision and focus of laser drilling lead to minimal thermal deformation of the surrounding material, preserving the integrity of the components being drilled.
Applications in the Auto Parts Manufacturing Industry
Laser drilling finds numerous applications within the auto parts manufacturing sector.
1. **Fuel Injection Components**: The automotive industry demands precise fuel injection components for efficient engine performance.
Laser drilling is instrumental in producing small-diameter holes in fuel injector nozzles, ensuring optimal fuel flow and atomization.
2. **Airbags**: The deployment system of airbags requires reliability and precision.
Laser drilling is used to accurately drill holes in pyrotechnic devices, ensuring timely inflation during accidents.
3. **Turbochargers**: The manufacture of turbochargers involves intricate designs and materials.
Laser drilling caters to the precise airflow management requirements by creating holes in compressor wheels and housing, optimizing performance.
4. **Exhaust Systems**: Laser drilling is pivotal in the fabrication of lightweight exhaust systems, particularly for components that need to withstand high temperature and pressure.
It creates holes necessary for noise suppression and emission control.
5. **Battery Components for Electric Vehicles**: As the shift towards electrification progresses, the demand for precise battery components increases.
Laser drilling is used in the production of compact and efficient batteries, improving electric vehicle performance.
Challenges and Considerations
While laser drilling presents numerous advantages, there are also challenges and considerations to keep in mind.
1. **Cost**: The initial investment for laser drilling setups can be relatively high.
However, the long-term benefits, such as reduced maintenance and faster production, often outweigh these costs.
2. **Complexity of Operation**: Operating laser drilling equipment requires skilled personnel with a good understanding of the technology to ensure optimal performance and safety.
3. **Material Limitations**: Some materials may not be suitable for laser drilling due to their reflectiveness or thermal properties.
In such cases, careful selection of laser type and parameters is crucial.
The Future of Laser Drilling in Automotive Manufacturing
The future of laser drilling in auto parts manufacturing looks promising as the industry continues to advance.
With developments in laser technology, including ultrafast lasers and improved automation, the precision and efficiency of laser drilling are expected to reach new heights.
As more automotive manufacturers adopt environmentally friendly practices, laser drilling’s ability to increase production efficiency while maintaining high-quality standards will be increasingly valuable.
Laser drilling will continue to support innovation, not only in traditional combustion vehicles but also in the growing electric vehicle sector.
Understanding the fundamentals of laser drilling and its applications helps new leaders in the production technology department contribute to their organization’s success.
By leveraging this sophisticated technology, they can ensure that their manufacturing processes remain at the forefront of industry standards, delivering quality auto parts that meet the demands of modern vehicles.
資料ダウンロード
QCD調達購買管理クラウド「newji」は、調達購買部門で必要なQCD管理全てを備えた、現場特化型兼クラウド型の今世紀最高の購買管理システムとなります。
ユーザー登録
調達購買業務の効率化だけでなく、システムを導入することで、コスト削減や製品・資材のステータス可視化のほか、属人化していた購買情報の共有化による内部不正防止や統制にも役立ちます。
NEWJI DX
製造業に特化したデジタルトランスフォーメーション(DX)の実現を目指す請負開発型のコンサルティングサービスです。AI、iPaaS、および先端の技術を駆使して、製造プロセスの効率化、業務効率化、チームワーク強化、コスト削減、品質向上を実現します。このサービスは、製造業の課題を深く理解し、それに対する最適なデジタルソリューションを提供することで、企業が持続的な成長とイノベーションを達成できるようサポートします。
オンライン講座
製造業、主に購買・調達部門にお勤めの方々に向けた情報を配信しております。
新任の方やベテランの方、管理職を対象とした幅広いコンテンツをご用意しております。
お問い合わせ
コストダウンが利益に直結する術だと理解していても、なかなか前に進めることができない状況。そんな時は、newjiのコストダウン自動化機能で大きく利益貢献しよう!
(Β版非公開)