- お役立ち記事
- Purchase order management to achieve both inventory reduction and delivery deadlines: Basics that new employees should learn
Purchase order management to achieve both inventory reduction and delivery deadlines: Basics that new employees should learn
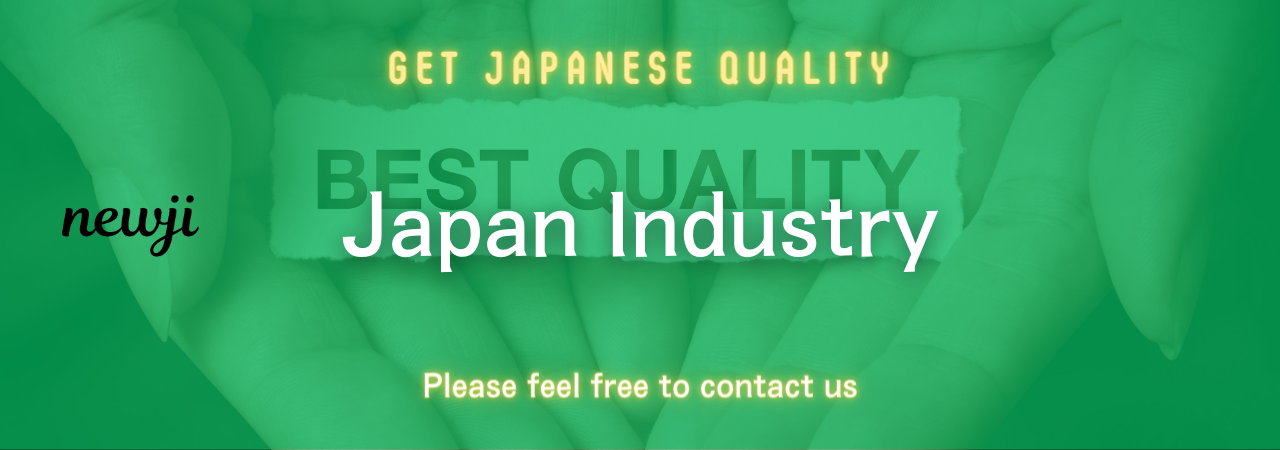
目次
Understanding Purchase Order Management
Purchase order management is a key component of supply chain management that ensures efficient operations within a business.
It involves the monitoring and management of purchase orders from the initial request through to the final delivery.
For new employees stepping into roles that require supply chain oversight, understanding the basics of purchase order management is crucial.
This includes learning how to balance inventory reduction with timely delivery deadlines to maintain customer satisfaction and operational efficiency.
The Importance of Purchase Order Management
Purchase order management serves multiple essential functions within a business.
Firstly, it helps in controlling the purchase process, ensuring everything runs smoothly and systematically.
By having a system in place, organizations can manage what they need, when they need it, reducing unnecessary inventory.
Furthermore, efficient management can significantly impact a company’s bottom line by minimizing costs associated with overstock and stockouts.
Being able to deliver products on time not only enhances customer satisfaction but also builds trust and reputation, both critical for business success.
Key Components of Purchase Order Management
To manage purchase orders effectively, understanding its key components is vital.
Firstly, there is the purchase request stage, where departments identify a need and request products or materials.
Next is supplier selection, an important step that involves finding reliable suppliers who can provide quality products at competitive prices.
The purchase order creation follows, where all relevant details are documented and communicated to the supplier.
Then comes the acknowledgment from the supplier, confirming receipt and understanding of the order.
Finally, ongoing tracking ensures the order is delivered as agreed, maintaining inventory levels and production timelines.
Strategies for Effective Inventory Management
Managing inventory involves striking the right balance—having enough product on hand to meet demand without creating excess.
New employees can adopt several strategies to manage inventory effectively.
One approach is implementing just-in-time (JIT) inventory systems, which reduce waste by receiving goods only as needed.
Another strategy is conducting regular inventory audits to monitor stock levels and reconcile discrepancies.
Using inventory management software can automate processes and provide real-time data insights, making it easier to forecast demand and make informed purchasing decisions.
These strategies can help in maintaining lean inventory levels while still meeting delivery deadlines.
Balancing Inventory Reduction with Delivery Deadlines
One of the biggest challenges in purchase order management is syncing inventory reduction efforts with delivery schedules.
While minimizing inventory can reduce holding costs, it’s crucial not to affect the ability to meet customer demand.
Collaborative forecasting with suppliers and customers can provide better insights into market demand.
This enables new employees to schedule orders that align with expected demand, reducing the risk of overstock or stockouts.
Flexibility in supply chain operations and building strong relationships with reliable suppliers can also provide a buffer against unexpected disruptions.
Clear communication and a proactive approach are key to striking this delicate balance.
Common Challenges and Solutions in Purchase Order Management
Even seasoned professionals face challenges in purchase order management, but new employees should be prepared.
One common challenge is handling supplier delays, which can ripple through the supply chain.
Establishing a network of multiple suppliers can provide alternatives if one doesn’t perform.
Another challenge is managing inaccuracies in purchase orders, often caused by manual data entry errors.
Implementing automated systems can eliminate this issue, ensuring data integrity.
Additionally, navigating fluctuating demand can be tricky.
Regular market analysis and demand forecasting can provide the necessary foresight to adjust purchasing strategies accordingly.
Technological Tools to Enhance Purchase Order Management
Leveraging technology is no longer optional but essential for efficient purchase order management.
There are various tools available that can streamline the process and enhance accuracy.
Enterprise Resource Planning (ERP) systems integrate all aspects of the business, providing a comprehensive view of operations.
This enables better tracking of purchase orders and inventory levels.
Automated purchase order software can manage requests and approvals quickly, reducing processing times.
Moreover, technologies like Artificial Intelligence (AI) and Machine Learning (ML) can predict trends and provide insights, allowing for more informed decision-making.
Technological tools not only improve efficiency but also provide a competitive edge in the market.
Final Thoughts
For new employees in supply chain and operations roles, mastering the basics of purchase order management is critical.
By understanding its importance, key components, and strategic approaches, they can contribute significantly to their organization’s efficiency and success.
Balancing inventory reduction with timely deliveries demands skill and precision, but with the right strategies and technological tools, it is entirely achievable.
Staying informed, proactive, and adaptable is vital in navigating the complexities of purchase order management, ultimately leading to improved productivity and customer satisfaction.
資料ダウンロード
QCD調達購買管理クラウド「newji」は、調達購買部門で必要なQCD管理全てを備えた、現場特化型兼クラウド型の今世紀最高の購買管理システムとなります。
ユーザー登録
調達購買業務の効率化だけでなく、システムを導入することで、コスト削減や製品・資材のステータス可視化のほか、属人化していた購買情報の共有化による内部不正防止や統制にも役立ちます。
NEWJI DX
製造業に特化したデジタルトランスフォーメーション(DX)の実現を目指す請負開発型のコンサルティングサービスです。AI、iPaaS、および先端の技術を駆使して、製造プロセスの効率化、業務効率化、チームワーク強化、コスト削減、品質向上を実現します。このサービスは、製造業の課題を深く理解し、それに対する最適なデジタルソリューションを提供することで、企業が持続的な成長とイノベーションを達成できるようサポートします。
オンライン講座
製造業、主に購買・調達部門にお勤めの方々に向けた情報を配信しております。
新任の方やベテランの方、管理職を対象とした幅広いコンテンツをご用意しております。
お問い合わせ
コストダウンが利益に直結する術だと理解していても、なかなか前に進めることができない状況。そんな時は、newjiのコストダウン自動化機能で大きく利益貢献しよう!
(Β版非公開)