- お役立ち記事
- For managers of quality assurance departments in the water pressure valve manufacturing industry for high-pressure washers! Designed to be both pressure resistant and rust proof
For managers of quality assurance departments in the water pressure valve manufacturing industry for high-pressure washers! Designed to be both pressure resistant and rust proof
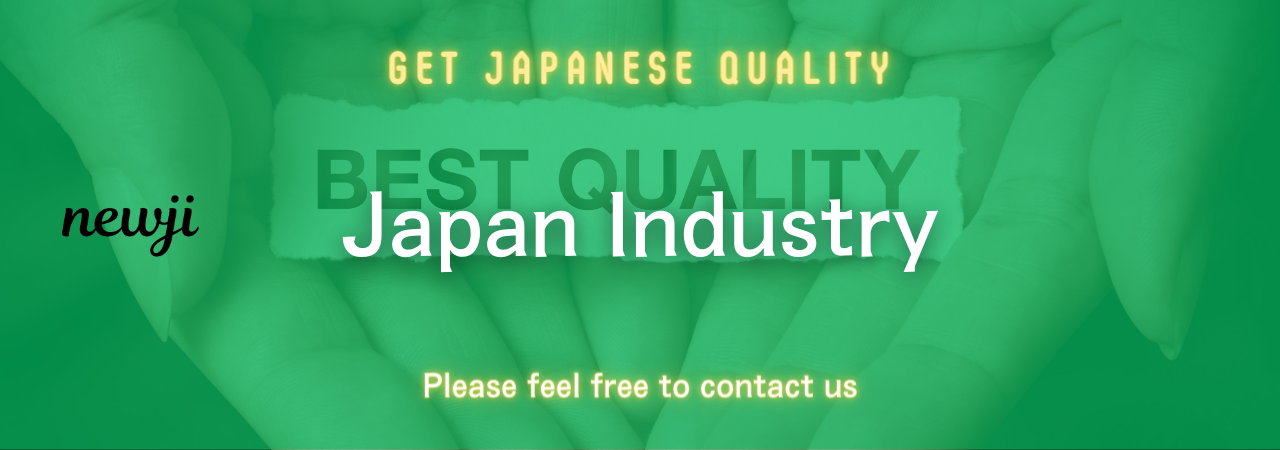
目次
Understanding the Importance of Quality Assurance in Water Pressure Valve Manufacturing
In the water pressure valve manufacturing industry, particularly for high-pressure washers, ensuring product quality is crucial.
As a manager in the quality assurance department, your role is pivotal in maintaining the high standards expected in the industry.
A well-designed valve is essential for the functionality and safety of high-pressure washers used in various applications.
The need for robust, pressure-resistant, and rust-proof valves cannot be overstated, as any failure in these components can lead to severe consequences.
The Role of Quality Assurance
Quality assurance (QA) in manufacturing involves systematic processes to ensure products meet specific requirements.
For pressure valves, this means confirming that each valve can withstand high pressure without deforming or failing.
QA teams test durability, pressure endurance, and resistance to environmental factors like rust.
A key aspect of quality assurance is implementing a rigorous testing protocol.
This involves stress testing valves to simulate real-world conditions and identifying potential points of failure.
By doing so, manufacturers can ensure that their products consistently perform to specification regardless of external conditions.
Design Considerations for Pressure-Resistant Valves
Designing pressure-resistant valves involves selecting materials that can endure high pressures without compromising functionality.
Materials such as stainless steel and specialized alloys are commonly used due to their strength and resistance to corrosion.
In addition to material selection, the valve’s design must include elements that distribute pressure evenly across the component.
This minimizes the risk of stress fractures or other failures that can occur under extreme pressure.
Furthermore, the valve’s design must facilitate easy maintenance and inspection.
This ensures that any wear and tear over time can be quickly identified and repaired, maintaining the valve’s performance throughout its lifecycle.
Ensuring Rust Proofing in High-Pressure Valves
Rust is a major concern for components exposed to water, particularly valves used in high-pressure washers.
Rust not only affects the aesthetic look of the valve but can significantly impair its performance and durability.
To combat rust, manufacturers use treatments such as galvanization or apply specialized coatings that form a protective layer on the valve surface.
Electroplating with nickel or chromium is also a common practice that provides a rust-resistant finish.
In the quality assurance process, it’s essential to test these protective coatings under various conditions to ensure they remain effective throughout the valve’s operational life.
This might include exposure to saltwater, varying temperatures, and humid environments to simulate potential operating conditions.
The Impact of Quality Valves on Performance and Safety
High-quality, pressure-resistant, and rust-proof valves directly influence the performance and safety of high-pressure washers.
A reliable valve ensures the equipment operates efficiently under high pressure, delivering consistent performance in industrial cleaning applications, car washes, and more.
From a safety perspective, robust valves prevent accidents that can occur due to valve failure, such as sudden releases of high-pressure water.
Such incidents can cause damage to property or even serious injury.
As a quality assurance manager, your role is to ensure that the valves produced are up to the highest safety standards.
This includes implementing strict quality control measures at every stage of the manufacturing process, from raw material selection to the final product inspection.
Developing a Comprehensive QA Strategy
Developing a comprehensive quality assurance strategy involves multiple stages.
Start with design validation to ensure initial concepts meet all necessary criteria for pressure and rust resistance.
This includes computer simulations and prototype testing.
Next, focus on process control where each step in the manufacturing process is monitored closely to detect any deviations from specified standards quickly.
Using automated inspection technologies, such as X-ray and ultrasonic testing, can enhance precision and reliability in detecting potential defects.
Finally, embrace continuous improvement, where gathering feedback from performance data and customer reviews helps to refine processes and product designs over time.
By fostering a culture of innovation and quality, the manufacturing team can stay ahead of industry standards and customer expectations.
Staying Ahead in the Industry
The water pressure valve manufacturing industry is highly competitive, and staying ahead requires a relentless focus on quality and innovation.
That means keeping up-to-date with the latest advancements in materials science and manufacturing technologies that can contribute to better product designs.
It also involves attending industry conferences and workshops to understand emerging trends and customer demands.
Building partnerships with suppliers and technology experts can help you gain insights into new materials or production methods that could elevate the quality of your valves.
In conclusion, as a manager of a quality assurance department in the water pressure valve manufacturing industry, your focus should be on ensuring every valve meets the highest standards of pressure resistance and rust proofing.
These qualities not only enhance the performance and longevity of the products but also safeguard users and maintain the company’s reputation in a competitive market.
資料ダウンロード
QCD調達購買管理クラウド「newji」は、調達購買部門で必要なQCD管理全てを備えた、現場特化型兼クラウド型の今世紀最高の購買管理システムとなります。
ユーザー登録
調達購買業務の効率化だけでなく、システムを導入することで、コスト削減や製品・資材のステータス可視化のほか、属人化していた購買情報の共有化による内部不正防止や統制にも役立ちます。
NEWJI DX
製造業に特化したデジタルトランスフォーメーション(DX)の実現を目指す請負開発型のコンサルティングサービスです。AI、iPaaS、および先端の技術を駆使して、製造プロセスの効率化、業務効率化、チームワーク強化、コスト削減、品質向上を実現します。このサービスは、製造業の課題を深く理解し、それに対する最適なデジタルソリューションを提供することで、企業が持続的な成長とイノベーションを達成できるようサポートします。
オンライン講座
製造業、主に購買・調達部門にお勤めの方々に向けた情報を配信しております。
新任の方やベテランの方、管理職を対象とした幅広いコンテンツをご用意しております。
お問い合わせ
コストダウンが利益に直結する術だと理解していても、なかなか前に進めることができない状況。そんな時は、newjiのコストダウン自動化機能で大きく利益貢献しよう!
(Β版非公開)