- お役立ち記事
- Supplier management method to “prevent delivery delays”—Risk mitigation strategies for purchasing departments
Supplier management method to “prevent delivery delays”—Risk mitigation strategies for purchasing departments
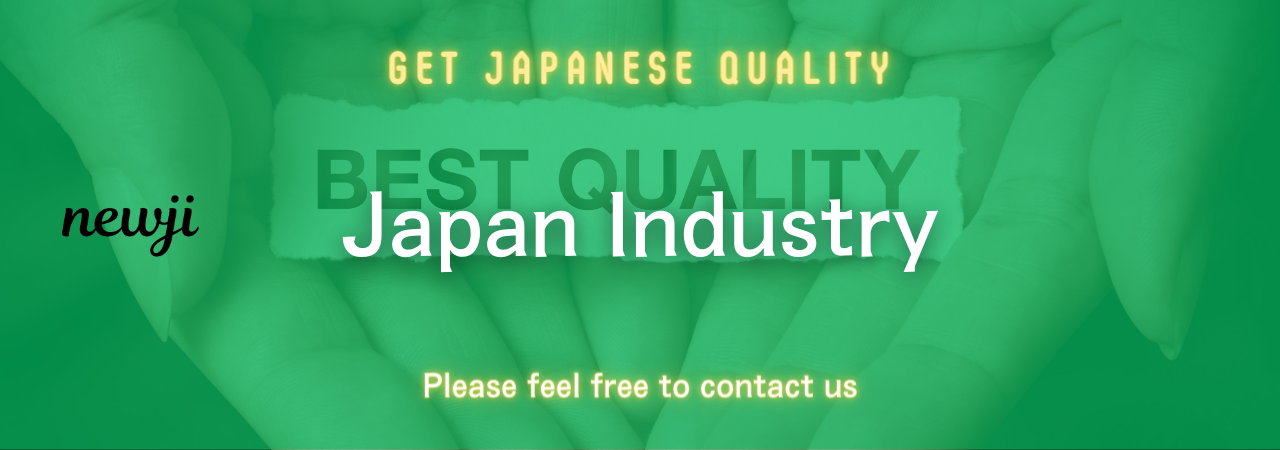
目次
Understanding Supplier Management
Supplier management is a crucial aspect of any business that relies on external vendors for materials or services.
It involves the systematic and strategic approach to managing supplier relationships to ensure consistent quality, timely delivery, and cost-effectiveness.
By efficiently managing suppliers, companies can mitigate risks associated with supply chain disruptions, such as delivery delays, which can have significant repercussions on business operations.
To proactively prevent delivery delays, it’s essential for purchasing departments to implement effective supplier management strategies.
These strategies involve close coordination and communication with suppliers, diligent oversight of their performance, and risk management techniques tailored to address potential challenges in the supply chain.
Identifying Potential Risks in the Supply Chain
The first step in mitigating risks associated with supplier management is to identify potential threats that can lead to delivery delays.
These risks can include:
– **Supplier Capacity Limitations:** Sometimes suppliers may overcommit their resources, leading to potential backlogs and delays.
– **Logistical Challenges:** Transportation issues, such as inadequate logistics planning or geopolitical factors, can cause delays.
– **Quality Issues:** Poor quality products might be rejected, causing rescheduling of deliveries and potential delays.
– **Supplier Financial Instability:** Financial troubles can hinder a supplier’s ability to fulfill orders or maintain their operational base.
Evaluating Supplier Performance
Regular evaluation of supplier performance is critical for understanding their reliability and capability.
Several key performance indicators (KPIs) should be assessed, such as on-time delivery rates, defect rates, and adherence to contract terms.
By maintaining an effective supplier scorecard, businesses can track performance over time and identify areas for improvement or concern.
Building Strong Supplier Relationships
The strength of relationships with suppliers plays a crucial role in preventing delivery delays.
Open, transparent, and two-way communication fosters trust and creates a partnership that benefits both parties.
Establishing Clear Expectations
To prevent misunderstandings that could lead to delivery delays, purchasing departments must set clear expectations from the outset.
This includes defining delivery schedules, quality standards, and communication protocols.
Contracts should be detailed yet flexible enough to accommodate unforeseen circumstances.
Regular Communication and Feedback
Regular meetings and communication channels should be established to facilitate information exchange.
This could include:
– Routine status updates on order progress.
– Regular feedback sessions to discuss performance metrics.
– Collaborative problem-solving to address any emerging issues.
Prompt feedback helps suppliers understand areas needing improvement and enhances their service.
Implementing Risk Mitigation Strategies
Purchasing departments need to adopt specific strategies to mitigate risks and ensure timely deliveries.
Diversification of Supplier Base
Relying on a single supplier can be risky.
By diversifying the supplier base, companies can reduce dependency on any single source.
Having multiple suppliers provides a buffer, ensuring that if one supplier fails, others can potentially fill the gap.
Developing Contingency Plans
Having a well-documented contingency plan is crucial for addressing potential disruptions.
These plans should outline steps to be taken in case of delivery delays, such as leveraging alternative suppliers or expediting shipments where possible.
Investment in Technology
Utilizing technology can greatly enhance supplier management.
Supply chain management software provides real-time visibility into the supply chain, helping companies track shipments, monitor supplier performance, and predict potential delays before they occur.
Building Long-Term Partnerships
Another effective method of preventing delivery delays is through forging long-term partnerships with suppliers.
By closely working with key suppliers, businesses can align goals and objectives for mutual benefit.
Joint Risk Assessment
Engaging suppliers in joint risk assessment workshops can help identify potential risks and develop strategies to mitigate them.
This collaborative approach fosters a deeper understanding and a shared commitment to preventing disruptions.
Incentives for Performance
Incentivizing suppliers for excellent performance can motivate them to maintain high standards.
Incentives might include preferred supplier status, longer-term contracts, or financial rewards for meeting delivery or quality benchmarks.
Regular Training and Development
Investing in training and development for the purchasing department can significantly improve supplier management capabilities.
Training programs can equip employees with the skills to negotiate better contracts, manage supplier relationships more effectively, and develop innovative risk management strategies.
Continuous Learning
Continuous learning initiatives, such as workshops, seminars, and industry conferences, can keep the team informed about the latest trends and best practices in supplier management.
Conclusion
Preventing delivery delays requires an integrated approach to supplier management that includes thorough risk identification, strong relationship-building, strategic diversification, and effective technology use.
By adopting these strategies, purchasing departments can minimize disruptions and enhance the overall resilience of their supply chains.
The ultimate goal is to create a stable and reliable supply chain that consistently delivers value to the organization and its customers.
資料ダウンロード
QCD調達購買管理クラウド「newji」は、調達購買部門で必要なQCD管理全てを備えた、現場特化型兼クラウド型の今世紀最高の購買管理システムとなります。
ユーザー登録
調達購買業務の効率化だけでなく、システムを導入することで、コスト削減や製品・資材のステータス可視化のほか、属人化していた購買情報の共有化による内部不正防止や統制にも役立ちます。
NEWJI DX
製造業に特化したデジタルトランスフォーメーション(DX)の実現を目指す請負開発型のコンサルティングサービスです。AI、iPaaS、および先端の技術を駆使して、製造プロセスの効率化、業務効率化、チームワーク強化、コスト削減、品質向上を実現します。このサービスは、製造業の課題を深く理解し、それに対する最適なデジタルソリューションを提供することで、企業が持続的な成長とイノベーションを達成できるようサポートします。
オンライン講座
製造業、主に購買・調達部門にお勤めの方々に向けた情報を配信しております。
新任の方やベテランの方、管理職を対象とした幅広いコンテンツをご用意しております。
お問い合わせ
コストダウンが利益に直結する術だと理解していても、なかなか前に進めることができない状況。そんな時は、newjiのコストダウン自動化機能で大きく利益貢献しよう!
(Β版非公開)