- お役立ち記事
- Basics of risk assessment using FMEA that new employees in the quality assurance department should know
Basics of risk assessment using FMEA that new employees in the quality assurance department should know
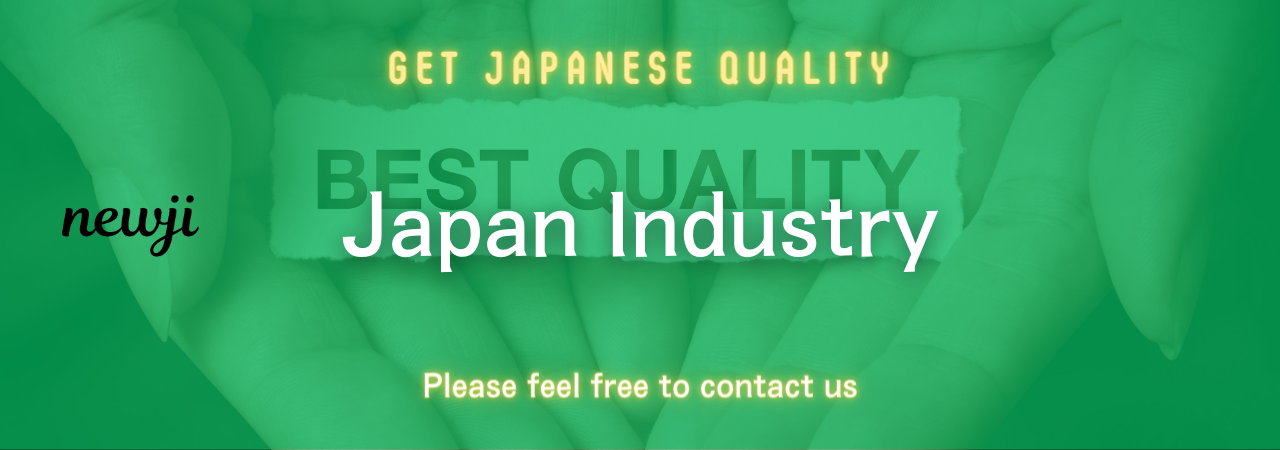
目次
Understanding FMEA: A Key Tool in Risk Assessment
Failure Mode and Effects Analysis (FMEA) is a systematic approach used to identify potential failures in a product, process, or service and evaluate their possible effects.
This critical tool helps organizations prioritize risks and implement corrective actions to prevent defects and improve overall quality.
For new employees in the quality assurance department, understanding the basics of FMEA is essential to ensuring the company’s standards and customer satisfaction.
What is FMEA?
FMEA stands for Failure Mode and Effects Analysis.
It’s a structured method that allows teams to identify potential failure modes of a product or process.
These are the ways in which something could fail to meet the expectations of the customer or violate product specifications.
The process involves evaluating the effect of these failures and determining how they might be prevented or mitigated.
FMEA begins with assembling a cross-functional team to bring diverse perspectives into the analysis.
The team identifies all possible failure modes and their effects on the system or process.
Once identified, the risk associated with each failure mode is assessed based on severity, occurrence, and detection.
The Goals of FMEA
The primary goal of FMEA is to improve the quality and reliability of products and processes by anticipating potential issues.
This enables organizations to:
– Enhance customer satisfaction by delivering defect-free products.
– Reduce costs associated with failures and repairs.
– Comply with industry standards and regulations.
– Boost the company’s reputation by consistently meeting quality standards.
Types of FMEA
There are several types of FMEA, and knowing which type to apply is crucial for effective risk management:
1. **Design FMEA (DFMEA):**
This type assesses risks associated with product design.
It helps identify potential design weaknesses that could lead to failures.
2. **Process FMEA (PFMEA):**
Used to evaluate processes, this type helps identify operational issues that might cause product defects.
3. **System FMEA:**
This broader analysis considers the entire system instead of focusing on individual components or processes.
By understanding these types, quality assurance teams can tailor their approach to address specific risks effectively.
The FMEA Process: A Step-by-Step Guide
Conducting an FMEA involves several key steps:
1. Define the Scope
Begin by defining the scope of the analysis.
Determine the boundaries of the system, product, or process under review.
This step is crucial to ensure the analysis remains focused and relevant.
2. Assemble the Team
Compile a team with diverse expertise.
Include individuals from different departments such as design, manufacturing, and quality assurance.
This diversity ensures a comprehensive analysis from multiple angles.
3. Identify Potential Failure Modes
Brainstorm potential failure modes and list them.
Each team member should contribute based on their experience and expertise.
4. Determine the Effects of Failure
For each failure mode, determine the potential effects on the product or process.
Consider how these failures could impact customer satisfaction and compliance with standards.
5. Assign Severity, Occurrence, and Detection Ratings
Use a consistent rating scale to assess the severity, likelihood of occurrence, and detectability of each failure mode.
Severity considers how serious the effects of a failure could be.
Occurrence estimates the probability of the failure happening.
Detection assesses how easily the failure can be detected before reaching the customer.
6. Calculate the Risk Priority Number (RPN)
For each failure mode, calculate the Risk Priority Number by multiplying the severity, occurrence, and detection ratings:
\[ \text{RPN} = \text{Severity} \times \text{Occurrence} \times \text{Detection} \]
The RPN helps prioritize which failure modes require immediate attention.
Higher RPN values indicate higher risks that need to be addressed promptly.
7. Develop and Implement Actions
Based on the analysis, develop action plans to mitigate identified risks.
This could involve design changes, process improvements, or enhanced inspection processes.
Benefits of Implementing FMEA
Understanding and utilizing FMEA provides numerous advantages:
– **Proactive Risk Management:**
FMEA allows organizations to address potential failures before they occur, avoiding costly disruptions.
– **Improved Product Quality:**
By identifying and mitigating risks early, products meet or exceed quality standards.
– **Enhanced Team Collaboration:**
The cross-functional approach encourages teamwork and knowledge sharing, leading to better solutions.
– **Customer Satisfaction:**
Delivering reliable products enhances customer trust and loyalty.
Challenges and Best Practices
Like any tool, implementing FMEA comes with its challenges.
New employees in the quality assurance department may face difficulties such as inadequate team participation or inconsistent analysis methods.
To overcome these, consider these best practices:
– **Ensuring Team Diversity:**
Engage colleagues from various backgrounds to provide a comprehensive analysis.
– **Regular Training:**
Invest in training to keep up with the latest FMEA techniques and methodologies.
– **Consistent Documentation:**
Maintain thorough documentation of the FMEA process to ensure traceability and facilitate audits.
– **Continuous Improvement:**
Regularly update FMEA analyses to reflect changes in products or processes.
Conclusion
For new employees entering the quality assurance field, mastering FMEA is an essential skill.
It equips individuals with the ability to foresee and mitigate potential failures, enhancing product quality and customer satisfaction.
By adhering to the systematic approach outlined in this article, new quality assurance personnel will contribute significantly to their organization’s success.
Despite the challenges, when executed correctly, FMEA serves as a powerful tool for risk assessment and management, ensuring that only the finest, failure-free products reach the customer.
資料ダウンロード
QCD調達購買管理クラウド「newji」は、調達購買部門で必要なQCD管理全てを備えた、現場特化型兼クラウド型の今世紀最高の購買管理システムとなります。
ユーザー登録
調達購買業務の効率化だけでなく、システムを導入することで、コスト削減や製品・資材のステータス可視化のほか、属人化していた購買情報の共有化による内部不正防止や統制にも役立ちます。
NEWJI DX
製造業に特化したデジタルトランスフォーメーション(DX)の実現を目指す請負開発型のコンサルティングサービスです。AI、iPaaS、および先端の技術を駆使して、製造プロセスの効率化、業務効率化、チームワーク強化、コスト削減、品質向上を実現します。このサービスは、製造業の課題を深く理解し、それに対する最適なデジタルソリューションを提供することで、企業が持続的な成長とイノベーションを達成できるようサポートします。
オンライン講座
製造業、主に購買・調達部門にお勤めの方々に向けた情報を配信しております。
新任の方やベテランの方、管理職を対象とした幅広いコンテンツをご用意しております。
お問い合わせ
コストダウンが利益に直結する術だと理解していても、なかなか前に進めることができない状況。そんな時は、newjiのコストダウン自動化機能で大きく利益貢献しよう!
(Β版非公開)