- お役立ち記事
- Quality Assurance of Imported Goods Supplier evaluation and audit procedures that should be carried out by the purchasing department
Quality Assurance of Imported Goods Supplier evaluation and audit procedures that should be carried out by the purchasing department
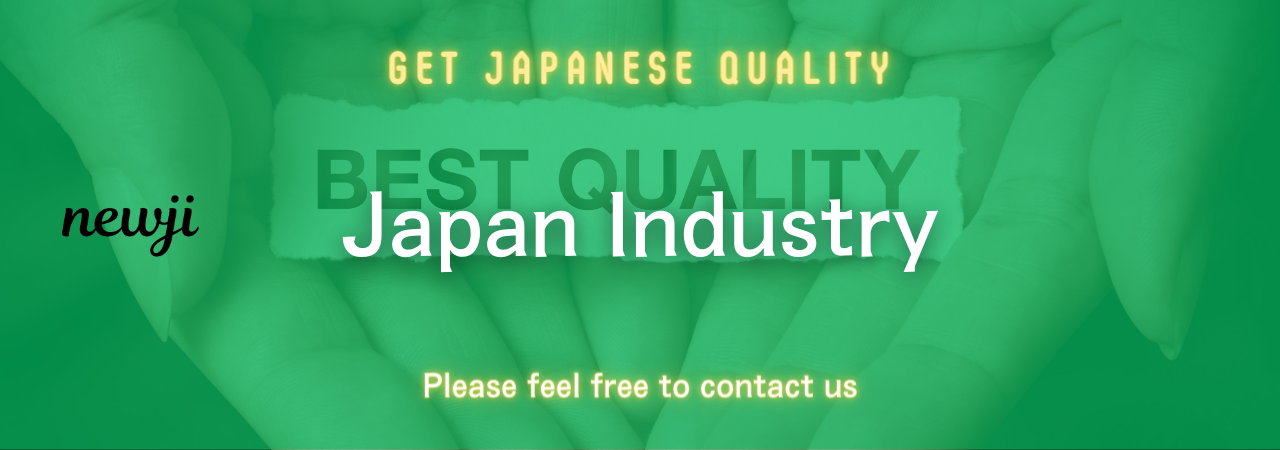
目次
Understanding Quality Assurance in Imported Goods
In today’s global market, businesses often rely on imported goods to meet consumer demands.
Ensuring the quality of these imported products is essential to maintain customer satisfaction and brand reputation.
Quality assurance involves a systematic process that includes supplier evaluation and audit procedures, mainly carried out by the purchasing department.
This article will explore these steps to ensure that imported goods consistently meet the required standards.
The Importance of Quality Assurance
Quality assurance is a critical aspect of the supply chain management process.
It ensures that the products sourced from international suppliers meet the set quality standards before reaching the end consumer.
This is particularly important for imported goods, which may have different regulatory standards and quality benchmarks.
Effective quality assurance helps prevent costly recalls, reduces customer complaints, and secures the brand’s position in the market.
It also ensures compliance with legal and safety regulations, which vary from country to country.
Supplier Evaluation: The First Step
Evaluating potential suppliers is the first step in ensuring quality assurance for imported goods.
This process involves a thorough assessment of a supplier’s ability to deliver products that meet quality expectations.
Determine Criteria for Evaluation
Before assessing suppliers, establish the criteria that will be used in the evaluation process.
These may include the supplier’s production capabilities, quality management systems, financial stability, and reputation.
Additionally, consider their ability to meet delivery timelines and their adherence to legal and ethical standards.
Conduct Supplier Audits
Supplier audits are a crucial component of the evaluation process.
These audits are performed on-site to inspect the manufacturing facilities, processes, and systems in place.
During an audit, the purchasing team assesses aspects such as cleanliness, safety standards, employee training, and overall quality control processes.
Evaluate Past Performance
Analyzing the supplier’s past performance can provide insight into their reliability and consistency in delivering quality products.
Reviewing previous business relationships, quality records, and customer feedback can help in making an informed decision.
Setting Up an Effective Audit Procedure
Once a supplier is selected, the purchasing department must regularly conduct audits to ensure continued compliance with quality standards.
An effective audit procedure includes several key elements.
Plan and Prepare
A successful audit requires adequate planning and preparation.
Defining the audit scope, objectives, and checklist ensures that the process is thorough and efficient.
Auditors should be well-trained and knowledgeable about the products and standards being evaluated.
Conducting the Audit
During the audit, it’s important to maintain open communication with the supplier to ensure transparency.
The audit team should follow the pre-defined checklist while maintaining flexibility to address any unforeseen issues.
It is vital to observe processes, interview staff, and review documentation related to quality control.
Report Findings and Implement Improvements
After the audit, the findings should be documented in a detailed report.
This report should highlight areas of compliance, as well as areas needing improvement.
Share these findings with the supplier and work collaboratively to develop a corrective action plan, implementing any necessary improvements.
Continuous Monitoring and Evaluation
Quality assurance does not end with one-time evaluations or audits.
It is an ongoing process that requires continuous monitoring and reevaluation of suppliers.
Regular Supplier Reviews
Conduct regular reviews of supplier performance to ensure ongoing compliance with quality standards.
These reviews can include periodic audits, shipment inspections, and regular communication to address any arising issues.
Utilize Technology
Leverage technology to track and monitor quality parameters such as defect rates, delivery timelines, and compliance with standards.
Implementing software solutions can facilitate real-time data analysis and reporting, enhancing decision-making and efficiency in the quality assurance process.
Feedback and Improvement
Encouraging open feedback from all stakeholders involved in the supply chain process is crucial.
Utilize feedback to identify potential weaknesses in the quality assurance process and work on continuous improvement strategies.
Conclusion
Quality assurance for imported goods is a vital aspect of maintaining a reputable supply chain.
By implementing thorough supplier evaluation and audit procedures, businesses can ensure that they source quality products consistently.
The purchasing department plays a pivotal role in this process, safeguarding brand reputation and customer satisfaction through effective quality assurance practices.
In an ever-evolving global market, staying vigilant and proactive in quality assurance will ultimately lead to a sustainable and successful business.
資料ダウンロード
QCD調達購買管理クラウド「newji」は、調達購買部門で必要なQCD管理全てを備えた、現場特化型兼クラウド型の今世紀最高の購買管理システムとなります。
ユーザー登録
調達購買業務の効率化だけでなく、システムを導入することで、コスト削減や製品・資材のステータス可視化のほか、属人化していた購買情報の共有化による内部不正防止や統制にも役立ちます。
NEWJI DX
製造業に特化したデジタルトランスフォーメーション(DX)の実現を目指す請負開発型のコンサルティングサービスです。AI、iPaaS、および先端の技術を駆使して、製造プロセスの効率化、業務効率化、チームワーク強化、コスト削減、品質向上を実現します。このサービスは、製造業の課題を深く理解し、それに対する最適なデジタルソリューションを提供することで、企業が持続的な成長とイノベーションを達成できるようサポートします。
オンライン講座
製造業、主に購買・調達部門にお勤めの方々に向けた情報を配信しております。
新任の方やベテランの方、管理職を対象とした幅広いコンテンツをご用意しております。
お問い合わせ
コストダウンが利益に直結する術だと理解していても、なかなか前に進めることができない状況。そんな時は、newjiのコストダウン自動化機能で大きく利益貢献しよう!
(Β版非公開)