- お役立ち記事
- A must-see for new employees in the design department of the aircraft parts manufacturing industry! Fundamentals of airfoil design using CFD (computational fluid dynamics)
A must-see for new employees in the design department of the aircraft parts manufacturing industry! Fundamentals of airfoil design using CFD (computational fluid dynamics)
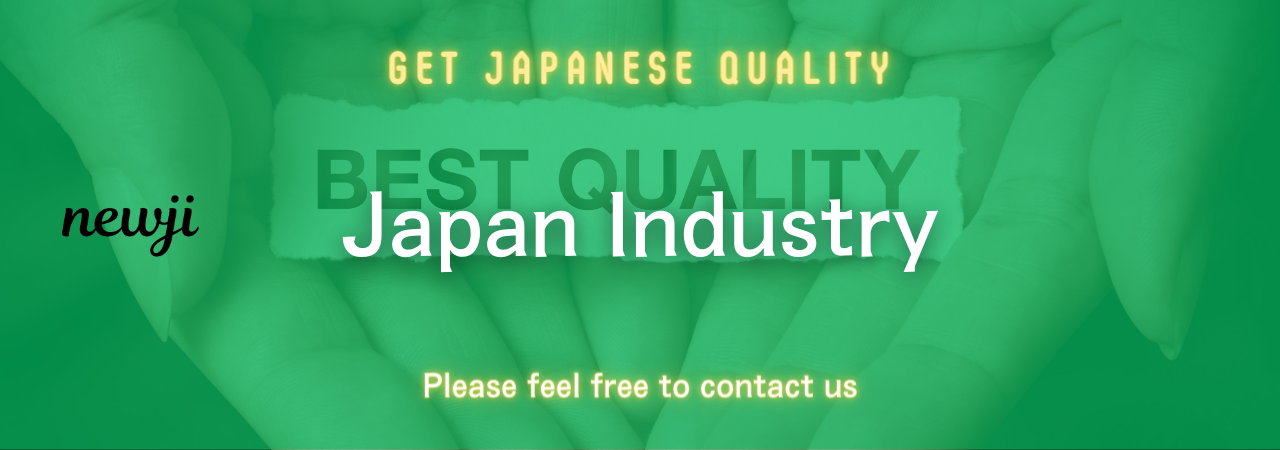
目次
Introduction to Airfoil Design
Embarking on a career in the design department of the aircraft parts manufacturing industry is exciting and challenging.
One key area that you’ll likely encounter is airfoil design.
An airfoil is a critical component of an aircraft’s wings, and its design determines the efficiency and performance of the aircraft in flight.
As a new employee, understanding the fundamentals of airfoil design using Computational Fluid Dynamics (CFD) is essential.
This technology has revolutionized the way airfoils are developed, allowing designers to predict the aerodynamic performance of different shapes and configurations with great accuracy.
What is Computational Fluid Dynamics?
Computational Fluid Dynamics, or CFD, is a branch of fluid mechanics that uses numerical analysis and algorithms to solve problems involving fluid flows.
CFD helps simulate the interaction of liquids and gases with surfaces, making it invaluable for airfoil design.
By applying CFD, designers can visualize how air moves over the surface of an airfoil, assessing factors like lift, drag, and airflow patterns.
This information is crucial in refining the design to meet specific performance requirements, ensuring aircraft can achieve maximum efficiency and safety.
The Basics of Airfoil Design
Before delving into CFD, it’s essential to grasp some basic concepts of airfoil design.
An airfoil’s shape determines how air travels over it, affecting lift and drag forces.
Key Features of an Airfoil
– **Leading Edge:** This is the front part of the airfoil, where the air first makes contact.
It should be rounded to minimize drag and maximize lift.
– **Trailing Edge:** This is the rear part of the airfoil.
A sharp trailing edge helps reduce drag and improve efficiency.
– **Camber:** This refers to the curvature of an airfoil.
A well-designed camber increases lift by creating a pressure difference between the upper and lower surfaces.
– **Angle of Attack:** This is the angle between the chord line of the airfoil and the oncoming airflow.
The angle of attack significantly impacts lift and drag performance.
Applying CFD to Airfoil Design
Using CFD in airfoil design involves several critical steps that allow engineers to simulate real-world conditions and optimize the airfoil’s shape.
1. Defining the Geometry
The first step is to define the geometry of the airfoil.
This includes establishing the shape, size, and boundary layers.
These parameters form the basis of the CFD model, allowing simulations to reflect realistic aerodynamic conditions.
2. Meshing the Airfoil
Meshing involves dividing the airfoil’s surface into small, discrete elements.
These elements form a grid, which the CFD software uses to solve fluid flow equations.
A finer mesh typically yields more accurate results, though it may also require increased computational power.
3. Setting Boundary Conditions
Boundary conditions specify the external influences on the airfoil, such as airflow velocity, temperature, and environmental pressure.
Correctly specifying these conditions ensures the simulation mimics real-world flight scenarios, providing reliable insights into how the airfoil will perform.
4. Running the Simulation
With the geometry, mesh, and boundary conditions in place, the next step is running the CFD simulation.
The software calculates the airflow over the airfoil, producing data on lift, drag, and pressure distribution.
Interpreting these results allows designers to identify areas for improvement and refine the airfoil’s design.
5. Analyzing Results and Iterating
The final step is to analyze the results from the CFD simulation.
This involves reviewing the airflow patterns, lift coefficients, and drag coefficients.
With these insights, designers can make informed adjustments to the airfoil’s shape, leading to subsequent iterations that often enhance performance.
The Benefits of Using CFD in Airfoil Design
CFD offers numerous advantages in airfoil design which explain its widespread adoption in the aircraft industry.
Cost-Effective
CFD reduces the need for costly physical prototypes and wind tunnel testing.
Simulation allows for early detection of design flaws, saving time and resources that would otherwise be spent on rework.
Enhanced Accuracy
With CFD, designers benefit from highly accurate predictions of aerodynamic performance.
This precision leads to more effective designs and helps in meeting stringent safety and efficiency standards.
Faster Design Cycles
The speed at which CFD provides results allows for quicker iterations and a faster design process.
This agility is critical in an industry where innovation and time-to-market are pivotal.
Conclusion
Understanding the fundamentals of airfoil design using CFD is an invaluable skill for anyone in the aircraft parts manufacturing industry.
By leveraging CFD, you can design highly efficient and innovative airfoils that meet the rigorous demands of modern aviation.
As you develop this expertise, you’ll contribute to safer, more sustainable aircraft and position yourself as a vital asset in your field.
Good luck as you begin your journey into the exciting world of airfoil design with CFD.
資料ダウンロード
QCD調達購買管理クラウド「newji」は、調達購買部門で必要なQCD管理全てを備えた、現場特化型兼クラウド型の今世紀最高の購買管理システムとなります。
ユーザー登録
調達購買業務の効率化だけでなく、システムを導入することで、コスト削減や製品・資材のステータス可視化のほか、属人化していた購買情報の共有化による内部不正防止や統制にも役立ちます。
NEWJI DX
製造業に特化したデジタルトランスフォーメーション(DX)の実現を目指す請負開発型のコンサルティングサービスです。AI、iPaaS、および先端の技術を駆使して、製造プロセスの効率化、業務効率化、チームワーク強化、コスト削減、品質向上を実現します。このサービスは、製造業の課題を深く理解し、それに対する最適なデジタルソリューションを提供することで、企業が持続的な成長とイノベーションを達成できるようサポートします。
オンライン講座
製造業、主に購買・調達部門にお勤めの方々に向けた情報を配信しております。
新任の方やベテランの方、管理職を対象とした幅広いコンテンツをご用意しております。
お問い合わせ
コストダウンが利益に直結する術だと理解していても、なかなか前に進めることができない状況。そんな時は、newjiのコストダウン自動化機能で大きく利益貢献しよう!
(Β版非公開)