- お役立ち記事
- A must-read for quality assurance department leaders in the battery pack manufacturing industry! Material selection for safety and longevity
A must-read for quality assurance department leaders in the battery pack manufacturing industry! Material selection for safety and longevity
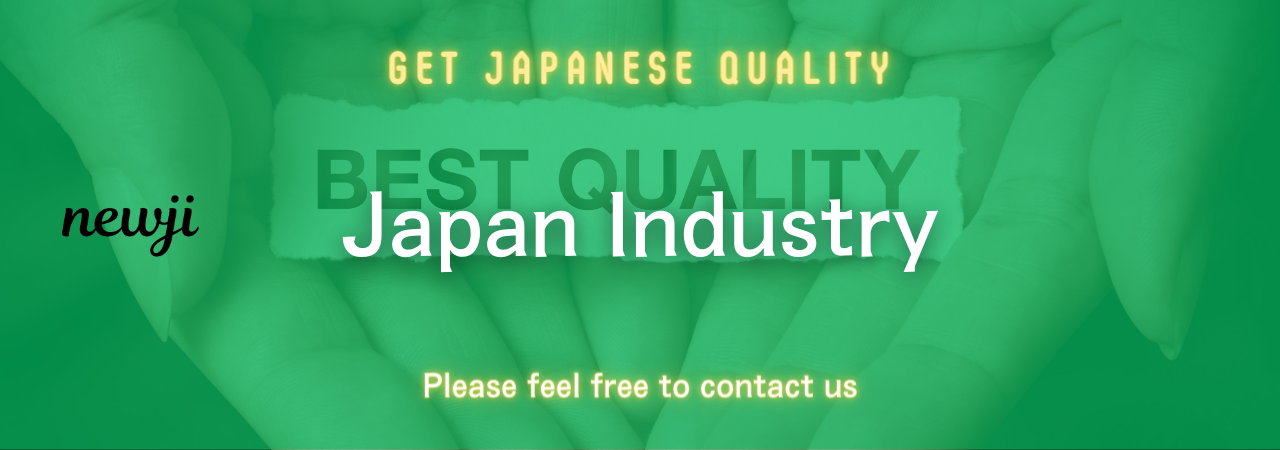
目次
Importance of Material Selection in Battery Pack Manufacturing
In the battery pack manufacturing industry, the role of quality assurance department leaders is crucial.
Their responsibilities include ensuring that every product meets safety standards and performs efficiently over its lifespan.
One critical element in achieving these goals is the careful selection of materials used in battery pack construction.
Material selection impacts not only the safety and reliability of battery packs but also their longevity and performance.
By choosing the appropriate materials, manufacturers can prevent common issues such as overheating, leakage, and reduced lifespan.
Additionally, the selection of high-quality materials can enhance the overall performance of the battery pack, leading to increased consumer satisfaction and safety.
Understanding the Various Components of a Battery Pack
To make informed material selection decisions, it’s essential to understand the components that make up a battery pack.
These include the anode, cathode, separator, electrolyte, and casing.
Each component plays a unique role in the function and efficiency of the battery pack.
Anode and Cathode Materials
The anode and cathode are vital to the chemical reactions that occur within a battery pack.
Common materials for anodes include graphite and various metals like lithium, while cathodes often include lithium-ion compounds.
The choice of materials for these components must consider factors such as energy density, cost, and environmental impact.
Graphite, for instance, is popular for anodes due to its excellent conductivity and stability.
However, innovations such as silicon-based anodes are being explored for higher capacity.
For cathodes, lithium cobalt oxide and nickel manganese cobalt are frequently used, offering a balance between performance and cost.
Separator Materials
The separator’s role is to keep the anode and cathode apart, preventing short circuits while allowing ions to pass through.
Materials like polyethylene and polypropylene are commonly used due to their chemical stability and mechanical strength.
Advancements in technology are leading to the development of more robust and thermally stable separators to enhance safety.
Electrolyte Composition
The electrolyte is responsible for ion transport between the anode and cathode.
Liquid electrolytes are standard, but solid-state options are gaining traction.
The choice of electrolyte material affects the battery’s conductive properties and operational safety.
Lithium salts dissolved in organic solvents are commonly used, but developers are exploring safer alternatives to reduce flammability.
Casing Materials
Battery casing materials must protect internal components from environmental factors and mechanical damage.
Aluminum and stainless steel are typical choices for their strength and light weight.
Advanced coatings and composite materials are also used to improve heat resistance and prevent corrosion.
Factors to Consider When Selecting Materials
Material selection involves careful consideration of several factors that impact the safety and longevity of battery packs.
Thermal Stability
Thermal stability is crucial in preventing overheating, which can lead to battery failure or hazards.
Materials must withstand temperature fluctuations without compromising performance.
Enhanced thermal management systems can significantly improve the safety of battery packs.
Chemical Compatibility
Ensuring that materials are chemically compatible with each other is vital to prevent reactions that could degrade performance or cause leaks.
Chemical stability extends the lifespan of battery packs and maintains consistent performance.
Mechanical Strength
Durability is another key consideration.
Materials must provide sufficient mechanical strength to withstand physical stress during use and transport.
This ensures the integrity of the battery pack over time.
Cost-Effectiveness
While quality is paramount, cost must also be considered to keep products competitive.
Balancing premium materials with cost-effective alternatives is necessary to achieve both safety and economic feasibility.
Environmental Impact
Sustainability is becoming increasingly important in material selection.
Choosing materials that are abundant, recyclable, and have a minimal environmental footprint can enhance a company’s reputation and contribute to global sustainability efforts.
Conclusion: The Role of Quality Assurance Leaders
Quality assurance leaders in the battery pack manufacturing industry have a critical role in guiding material selection processes.
Their expertise ensures that materials align with safety and performance standards, ultimately protecting consumers and enhancing product longevity.
Through ongoing research and innovation, the industry is continually exploring new materials and technologies.
Quality assurance teams must stay informed of these advancements and adapt their strategies accordingly.
By prioritizing material selection, quality assurance leaders can support the development of battery packs that are safe, reliable, and long-lasting, meeting the demands of a rapidly evolving market.
資料ダウンロード
QCD調達購買管理クラウド「newji」は、調達購買部門で必要なQCD管理全てを備えた、現場特化型兼クラウド型の今世紀最高の購買管理システムとなります。
ユーザー登録
調達購買業務の効率化だけでなく、システムを導入することで、コスト削減や製品・資材のステータス可視化のほか、属人化していた購買情報の共有化による内部不正防止や統制にも役立ちます。
NEWJI DX
製造業に特化したデジタルトランスフォーメーション(DX)の実現を目指す請負開発型のコンサルティングサービスです。AI、iPaaS、および先端の技術を駆使して、製造プロセスの効率化、業務効率化、チームワーク強化、コスト削減、品質向上を実現します。このサービスは、製造業の課題を深く理解し、それに対する最適なデジタルソリューションを提供することで、企業が持続的な成長とイノベーションを達成できるようサポートします。
オンライン講座
製造業、主に購買・調達部門にお勤めの方々に向けた情報を配信しております。
新任の方やベテランの方、管理職を対象とした幅広いコンテンツをご用意しております。
お問い合わせ
コストダウンが利益に直結する術だと理解していても、なかなか前に進めることができない状況。そんな時は、newjiのコストダウン自動化機能で大きく利益貢献しよう!
(Β版非公開)