- お役立ち記事
- Roller preventive maintenance and abnormality detection methods that new leaders of equipment maintenance departments in the steel industry should know
Roller preventive maintenance and abnormality detection methods that new leaders of equipment maintenance departments in the steel industry should know
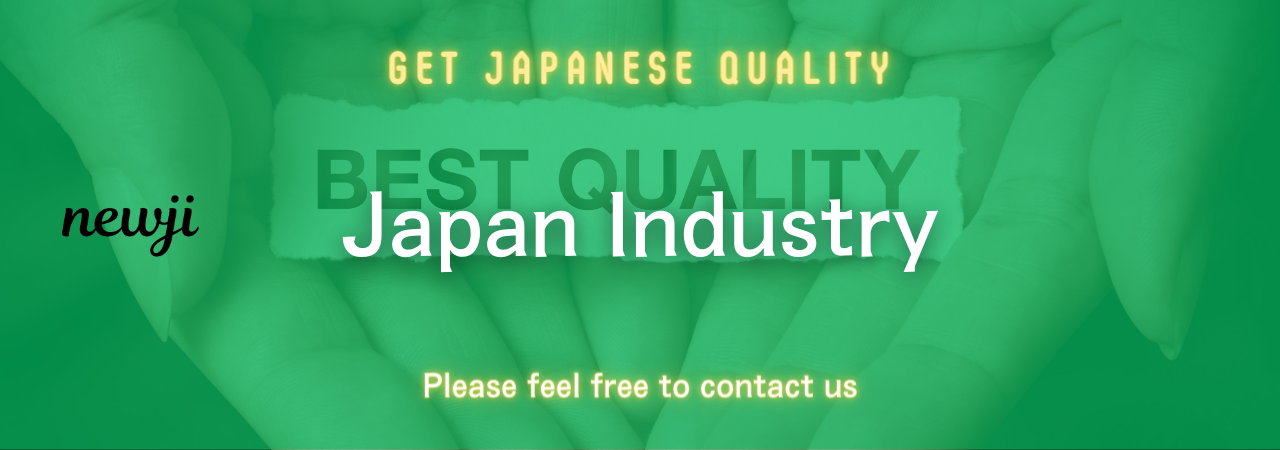
目次
Understanding Roller Preventive Maintenance
Roller preventive maintenance is a fundamental aspect of equipment management in the steel industry.
For new leaders in the equipment maintenance department, having a solid grasp of this concept is crucial.
Preventive maintenance aims to keep industrial rollers in optimal condition, reducing the likelihood of unexpected failures.
By implementing regular maintenance routines, companies can minimize downtime and extend the lifespan of their equipment.
The implementation of a preventive maintenance plan involves several steps.
First, it is essential to conduct a thorough inspection of the rollers.
This inspection should focus on identifying signs of wear, misalignment, and any irregular vibrations.
Key areas to inspect include the roller surface, bearings, and lubrication systems.
Once the inspection is complete, the next step is to perform necessary maintenance activities.
This could include cleaning, lubricating, and tightening any loose components.
Regular lubrication is key to ensuring smooth operation and preventing unnecessary friction and wear.
Adjustments or replacements of worn parts should be made promptly to prevent further deterioration.
A preventive maintenance schedule should be established and adhered to.
This schedule will be based on the manufacturer’s recommendations, machine usage, and historical data from previous inspections.
Regular maintenance will decrease the risk of sudden breakdowns and enhance roller performance.
Abnormality Detection in Rollers
Detecting abnormalities in rolling equipment is another critical responsibility for maintenance leaders.
Timely identification of potential issues can prevent minor problems from escalating into major failures.
Abnormality detection typically involves the use of advanced monitoring technologies and diagnostic tools.
One common method for detecting abnormalities is vibration analysis.
Excessive vibrations often indicate misalignments or bearing damages.
By monitoring vibrations, maintenance teams can identify issues early and schedule the necessary interventions before the roller suffers significant damage.
Thermal imaging is another effective technique in detecting abnormalities.
By measuring temperature variations across the roller surface, maintenance teams can quickly identify areas of concern.
Excessive heat often signals excessive friction or a failing component, warranting immediate attention.
Ultrasonic testing is also valuable for detecting internal defects.
It can identify issues such as cracks or voids within the material that might not be visible through a standard visual inspection.
Regular checks using ultrasonic technology can ensure that rollers are structurally sound and ready for operation.
The Importance of Staff Training
Staff training is a pivotal component in the successful execution of maintenance strategies.
New leaders should ensure that their teams are well-versed in both preventive maintenance procedures and abnormality detection techniques.
Regular training sessions and workshops can help maintain a skilled and informed workforce.
Training should cover basic roller maintenance tasks, proper use of diagnostic tools, and adherence to safety standards.
Complex analysis methods like vibration analysis or ultrasonic testing should be taught by experienced professionals to ensure accuracy and reliability.
Encouraging open communication within the maintenance department is beneficial.
A culture of teamwork and shared responsibility can lead to quicker identification and resolution of potential issues.
Staff should feel empowered to report any suspected abnormalities or inefficiencies immediately.
Utilizing Technology in Maintenance
The integration of technology in maintenance processes can significantly improve efficiency and accuracy.
Many steel companies are now adopting Industry 4.0 solutions, including the Internet of Things (IoT) and data analytics, to optimize maintenance practices.
IoT devices can be fitted to rollers to collect real-time data on performance metrics such as speed, temperature, and vibrations.
This data can be analyzed to predict potential failures and schedule maintenance activities proactively.
Such predictive maintenance helps reduce unscheduled downtime and enhances the reliability of the equipment.
Advanced software solutions can help manage maintenance schedules, track inventories for spare parts, and record past maintenance work.
These tools provide maintenance leaders with a comprehensive overview of equipment condition and streamline maintenance operations.
Building a Culture of Continuous Improvement
Fostering a culture of continuous improvement within the maintenance department is another key responsibility for leaders.
Encouraging innovative thinking and the adoption of new methodologies can lead to better maintenance outcomes.
Regular review meetings should be conducted to assess the effectiveness of current maintenance practices.
These sessions can identify areas of improvement, set new objectives, and align the team towards achieving them.
Encouraging feedback from maintenance staff can also uncover practical insights that might not be visible from a management perspective.
Partnering with equipment manufacturers for regular updates and training on new technologies can keep the maintenance department at the cutting edge.
Adapting to new techniques and tools will ensure that maintenance practices keep pace with technological advancements in the industry.
Conclusion
Roller preventive maintenance and abnormality detection are critical aspects of maintaining operational efficiency in the steel industry.
For new leaders in equipment maintenance, understanding these concepts is vital for ensuring reliable and efficient plant operations.
By focusing on proper maintenance schedules, effective abnormality detection, continuous staff training, and leveraging modern technology, maintenance departments can achieve exceptional performance and productivity.
Embracing a culture of continuous improvement will not only enhance equipment longevity but also contribute to the overall success of the organization.
資料ダウンロード
QCD調達購買管理クラウド「newji」は、調達購買部門で必要なQCD管理全てを備えた、現場特化型兼クラウド型の今世紀最高の購買管理システムとなります。
ユーザー登録
調達購買業務の効率化だけでなく、システムを導入することで、コスト削減や製品・資材のステータス可視化のほか、属人化していた購買情報の共有化による内部不正防止や統制にも役立ちます。
NEWJI DX
製造業に特化したデジタルトランスフォーメーション(DX)の実現を目指す請負開発型のコンサルティングサービスです。AI、iPaaS、および先端の技術を駆使して、製造プロセスの効率化、業務効率化、チームワーク強化、コスト削減、品質向上を実現します。このサービスは、製造業の課題を深く理解し、それに対する最適なデジタルソリューションを提供することで、企業が持続的な成長とイノベーションを達成できるようサポートします。
オンライン講座
製造業、主に購買・調達部門にお勤めの方々に向けた情報を配信しております。
新任の方やベテランの方、管理職を対象とした幅広いコンテンツをご用意しております。
お問い合わせ
コストダウンが利益に直結する術だと理解していても、なかなか前に進めることができない状況。そんな時は、newjiのコストダウン自動化機能で大きく利益貢献しよう!
(Β版非公開)