- お役立ち記事
- A must-see for equipment managers in the electronic equipment manufacturing industry! Site improvement guide for electrostatic discharge (ESD) countermeasures
A must-see for equipment managers in the electronic equipment manufacturing industry! Site improvement guide for electrostatic discharge (ESD) countermeasures
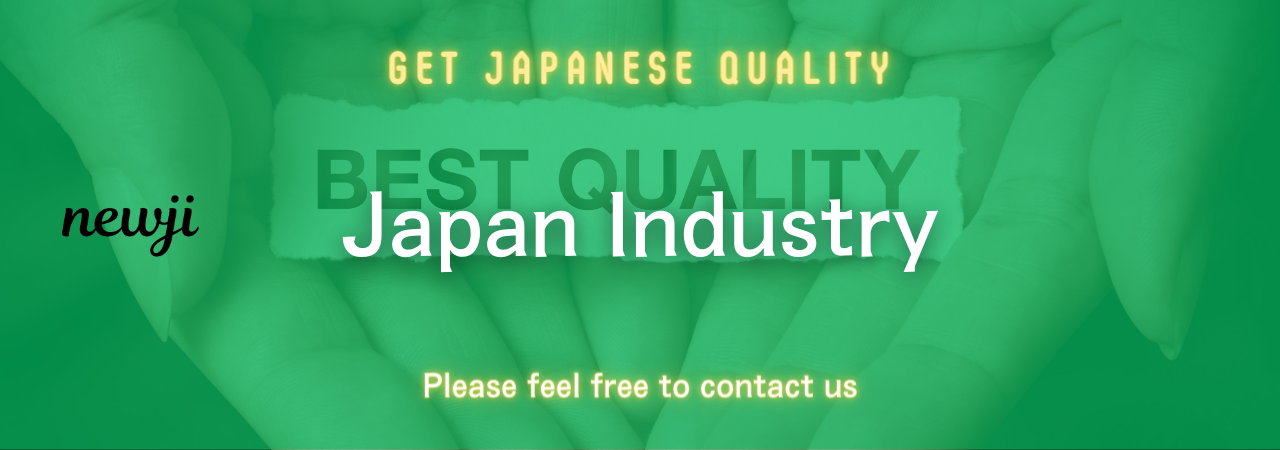
目次
Understanding Electrostatic Discharge (ESD)
Electrostatic Discharge (ESD) is a sudden flow of electricity between two electrically charged objects caused by contact, an electrical short, or dielectric breakdown.
In the realm of electronic equipment manufacturing, ESD is a pervasive issue that can lead to severe consequences such as damaged components, malfunctioning devices, and costly repairs.
It is essential for equipment managers in this industry to understand ESD and implement effective countermeasures to prevent its adverse effects.
The Importance of ESD Control
ESD can cause the failure of electronic devices or systems, often rendering them unusable or leading to subtle faults that cause intermittent problems.
These failures can occur during manufacturing, handling, or even use, impacting quality and reliability.
Implementing ESD control measures helps minimize the risk of these problems, ensuring the longevity and performance of electronic components and devices.
Equipment managers play a critical role in developing and enforcing ESD control procedures, which is why understanding the foundation and necessity of these measures is vital.
Key ESD Countermeasures
1. ESD-Safe Workstations
Creating ESD-safe workstations is a fundamental step in mitigating ESD risks.
This involves using specialty work surfaces and grounding systems designed to safely dissipate static charges.
ESD-safe materials, such as mats, table coverings, and wrist straps, are essential, as they prevent the accumulation of static electricity.
2. Grounding
Grounding is a primary method for controlling ESD.
By connecting personnel and equipment to a common electrical ground, static charges accumulated can be safely dissipated.
All surfaces, equipment, and even personnel should be properly grounded to minimize the possibility of a static discharge.
3. Environmental Controls
The environment has a significant impact on static electricity generation.
Maintaining optimal humidity levels (typically between 40% and 60%) helps reduce static charge buildup.
Incorporating ionizers in your facility can also help neutralize static-laden air.
These ionizers emit both positive and negative ions, which attach to charge carriers, neutralizing potential ESD threats.
4. Personnel Training
Personnel working in the electronic manufacturing environment should undergo regular ESD training.
Training should cover how ESD occurs, its potential impacts, and best practices for preventing ESD damage.
Educated employees become the first line of defense against ESD events.
5. ESD-Proof Packaging
Utilizing ESD-proof packaging during transportation and storage is crucial for protecting sensitive components.
Materials such as antistatic bags or conductive and dissipative containers safeguard components from ESD occurrences and reduce the likelihood of generating static.
6. Regular Audits and Monitoring
Conducting regular audits of ESD practices and environments is necessary to ensure compliance.
This includes monitoring grounding systems, verifying the effectiveness of ESD control materials, and ensuring employees adhere to established guidelines.
Updating equipment and strategies as new technologies and information become available is also vital for maintaining a robust ESD control program.
Site Improvement Techniques for ESD Management
Identify Static-Prone Areas
Start by identifying locations within your site that are most susceptible to static buildup.
This can include areas where synthetic materials are prevalent, or where there is frequent movement of people or machinery.
Prioritize these areas for ESD control implementation.
Enhance ESD Awareness
Increasing ESD awareness within your organization can lead to more proactive management of ESD risks.
Consider implementing informational campaigns and visual reminders to reinforce the importance of ESD prevention among all personnel.
Utilize Advanced Technology
With technological advancements, new solutions for ESD control are continually being developed.
These innovations might include wearable technology for real-time ESD monitoring or dynamic flooring systems that adjust according to detected static levels.
Incorporating such technologies can enhance the overall effectiveness of your ESD countermeasures.
Optimize Production Flows
Review and optimize production flows to ensure that ESD-sensitive processes occur in controlled environments.
Segregate high-risk ESD areas from other operations and establish clear protocols for handling sensitive components within these zones.
Conclusion
By understanding the importance of ESD and implementing comprehensive countermeasures, equipment managers can significantly reduce the risk of ESD-related damage in electronic equipment manufacturing.
Integrating ESD control measures into daily operations not only ensures compliance but also enhances the reliability and quality of electronic products.
Continual education, innovation, and vigilance are key to maintaining effective ESD protection in today’s rapidly advancing electronic industry.
資料ダウンロード
QCD調達購買管理クラウド「newji」は、調達購買部門で必要なQCD管理全てを備えた、現場特化型兼クラウド型の今世紀最高の購買管理システムとなります。
ユーザー登録
調達購買業務の効率化だけでなく、システムを導入することで、コスト削減や製品・資材のステータス可視化のほか、属人化していた購買情報の共有化による内部不正防止や統制にも役立ちます。
NEWJI DX
製造業に特化したデジタルトランスフォーメーション(DX)の実現を目指す請負開発型のコンサルティングサービスです。AI、iPaaS、および先端の技術を駆使して、製造プロセスの効率化、業務効率化、チームワーク強化、コスト削減、品質向上を実現します。このサービスは、製造業の課題を深く理解し、それに対する最適なデジタルソリューションを提供することで、企業が持続的な成長とイノベーションを達成できるようサポートします。
オンライン講座
製造業、主に購買・調達部門にお勤めの方々に向けた情報を配信しております。
新任の方やベテランの方、管理職を対象とした幅広いコンテンツをご用意しております。
お問い合わせ
コストダウンが利益に直結する術だと理解していても、なかなか前に進めることができない状況。そんな時は、newjiのコストダウン自動化機能で大きく利益貢献しよう!
(Β版非公開)