- お役立ち記事
- The relationship between density and durability that new employees in the quality control department of the sponge manufacturing industry should understand
The relationship between density and durability that new employees in the quality control department of the sponge manufacturing industry should understand
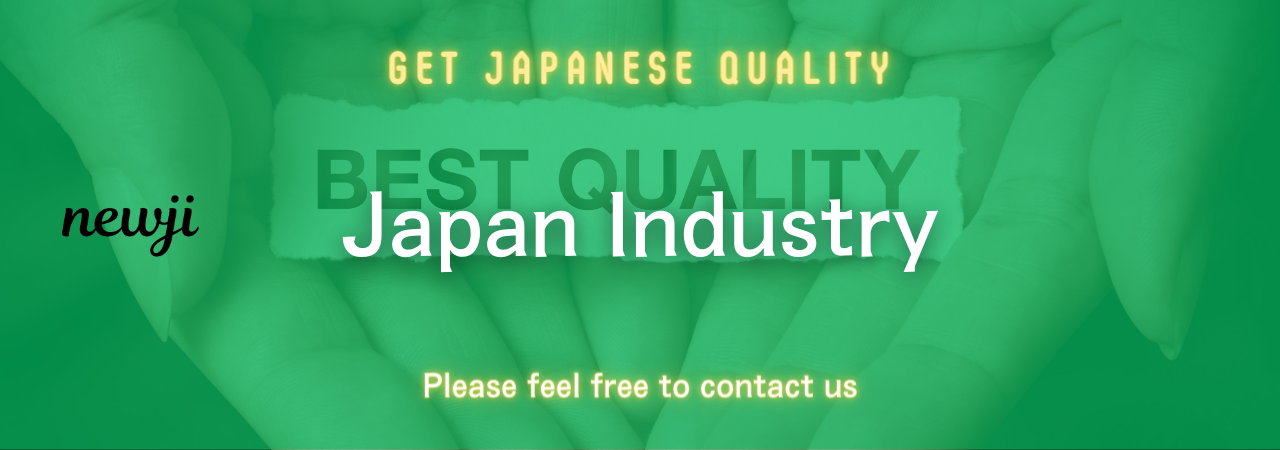
目次
Understanding Density in Sponge Manufacturing
Sponge manufacturing is an intricate process, especially when it comes to understanding how the properties of a sponge, like density, relate to its overall quality and durability.
As a new employee in the quality control department, it’s crucial to grasp these concepts to ensure the production of high-quality and durable sponges.
The density of a sponge is a fundamental characteristic that directly impacts its properties and potential uses.
In simple terms, density refers to how much mass is contained in a given volume.
For sponges, this means how tightly the sponge material is packed together.
The measurement is typically expressed in kilograms per cubic meter (kg/m³).
Higher density often translates to increased durability, but it’s important to understand the nuances of this relationship.
The Importance of Density in Sponges
Density significantly affects several attributes of sponges, including cushioning, flexibility, absorption capacity, and overall durability.
Sponges with higher density generally have less air space within them, which can make them firmer and more resilient under compression.
This increased firmness can also mean that the sponge will maintain its shape over time, lending to greater durability.
In contrast, a sponge with low density may feel softer and more cushioned, which can be ideal for applications requiring high levels of comfort or absorption.
However, these sponges may not withstand wear and tear as effectively as their denser counterparts.
Understanding the balance between density, comfort, and application is vital for quality control in sponge manufacturing.
Factors Influencing Sponge Density
Several factors influence the density of sponges during manufacturing.
These include the type of raw materials used, the manufacturing process parameters, and the specific formulation of the sponge.
The choice of raw materials is pivotal.
Natural sponges, typically harvested from the sea, have different density properties compared to synthetic sponges made from materials like polyurethane.
The cellular structure, size of pores, and the rigidity of the material all contribute to the final density.
Manufacturing processes such as the mixing, foaming, and curing phases also play significant roles.
Processes that result in more compact cell structures produce higher-density sponges.
For instance, controlling the amount of gas or foaming agent used can determine the density by adjusting the number of air pockets within the sponge.
Balancing Density and Performance
For quality control professionals, the challenge lies in balancing density to align with the desired performance characteristics.
A sponge’s intended use will dictate this balance.
For instance, kitchen sponges intended for scrubbing might require a different density than those designed for car cleaning or use in medical applications.
Durability is a priority for sponges used in more abrasive applications, requiring higher density.
These sponges must withstand continuous pressure and friction.
Conversely, applications that prioritize softness and absorption might benefit from lower-density sponges.
Quality control involves testing and assessing sponges to ensure they meet these diverse needs.
Testing Durability in Sponges
Durability testing is a critical aspect of quality control.
It involves simulating conditions that sponges will encounter during their lifespan to assess their resilience and longevity.
Common tests include compression tests, which measure how well a sponge retains its shape after being compressed, and abrasion tests, which determine how well a sponge resists wear and tear.
Higher-density sponges often outperform in these tests due to their compact structure.
However, it’s crucial to interpret these results with the understanding that higher density may reduce flexibility and increase weight, which are important considerations in certain applications.
Therefore, understanding the optimal density is important to create a product that meets durability expectations without compromising on other essential qualities.
Real-Life Applications and Considerations
In the real world, sponges are used in countless applications, each with its particular density and durability requirements.
Medical sponges, for instance, require precise density specifications to ensure safety and effectiveness.
These sponges often need to be both absorbent and soft, yet maintain enough durability to withstand specific medical procedures.
Similarly, sponges used in industrial cleaning need to balance high durability with ease of use.
Their density must allow for efficient scrubbing without falling apart under stress.
In automotive manufacturing, sponges used in interior applications must remain soft and pliable, yet durable enough to handle repeated use.
These applications underscore the necessity for ongoing density research and development in sponge manufacturing.
Conclusion: The Role of Quality Control in Sponge Manufacturing
As a new employee in quality control, understanding the interplay between density and durability is vital.
This knowledge ensures that the sponges produced meet high standards and are fit for their intended purposes.
By considering factors like raw materials, manufacturing processes, and application-specific requirements, quality control teams maintain the balance necessary for creating superior sponge products.
A focus on proper testing and understanding application scenarios helps ensure that density parameters are not just met but optimized for performance.
This expertise allows for the continuous improvement of sponges, addressing evolving consumer needs and industry standards.
In essence, mastering the relationship between density and durability in sponges is a stepping stone to success in quality control within the sponge manufacturing industry.
資料ダウンロード
QCD調達購買管理クラウド「newji」は、調達購買部門で必要なQCD管理全てを備えた、現場特化型兼クラウド型の今世紀最高の購買管理システムとなります。
ユーザー登録
調達購買業務の効率化だけでなく、システムを導入することで、コスト削減や製品・資材のステータス可視化のほか、属人化していた購買情報の共有化による内部不正防止や統制にも役立ちます。
NEWJI DX
製造業に特化したデジタルトランスフォーメーション(DX)の実現を目指す請負開発型のコンサルティングサービスです。AI、iPaaS、および先端の技術を駆使して、製造プロセスの効率化、業務効率化、チームワーク強化、コスト削減、品質向上を実現します。このサービスは、製造業の課題を深く理解し、それに対する最適なデジタルソリューションを提供することで、企業が持続的な成長とイノベーションを達成できるようサポートします。
オンライン講座
製造業、主に購買・調達部門にお勤めの方々に向けた情報を配信しております。
新任の方やベテランの方、管理職を対象とした幅広いコンテンツをご用意しております。
お問い合わせ
コストダウンが利益に直結する術だと理解していても、なかなか前に進めることができない状況。そんな時は、newjiのコストダウン自動化機能で大きく利益貢献しよう!
(Β版非公開)